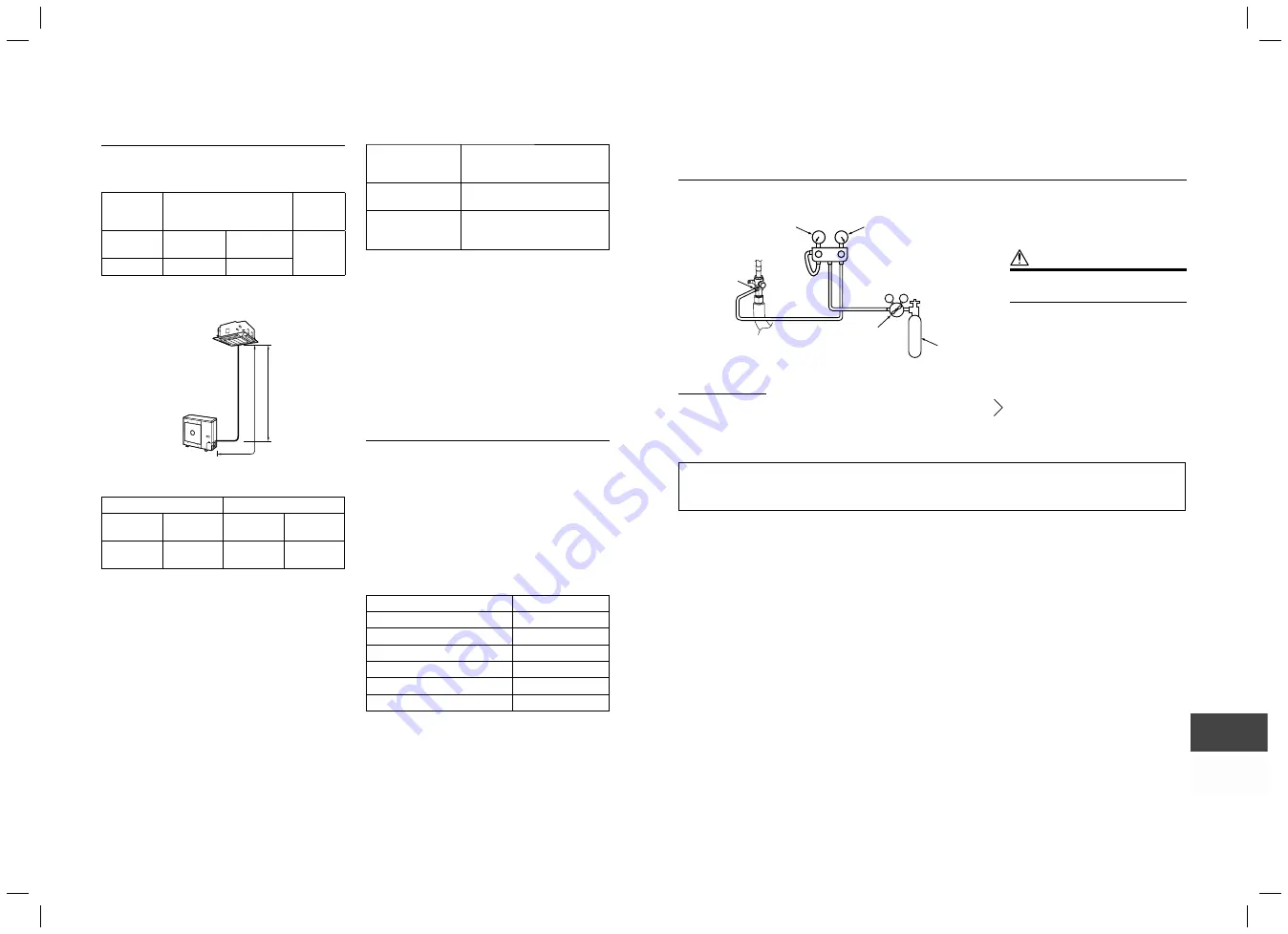
– 10 –
■
System Requirements
•
Minimum refrigerant line length between the outdoor
unit and indoor unit is 16
’
5” (5 m)
•
Maximum pipe lengths
Allowable
pipe length
(ft (m))
Height difference
(Indoor-outdoor H)
(ft (m))
Number
of bent
portions
Total length
L
Indoor unit:
Upper
Outdoor unit:
Lower
10 or less
164’1” (50)
98’5” (30)
98’5” (30)
Figure of Single
H
L
Indoor Unit
Outdoor Unit
Refrigerant sizes
Liquid side
Gas side
Outer
diameter
Thickness
Outer
diameter
Thickness
Ø3/8”
(9.5 mm)
0.03”
(0.8 mm)
Ø5/8”
(15.9 mm)
0.04”
(1.0 mm)
Flare nuts and
fl
aring
•
The
fl
are nuts and
fl
aring are different from those for
the conventional refrigerant.
Use the flare nuts supplied with the air conditioner or
those for R410A.
•
Before performing
fl
aring, carefully read
“REFRIGERANT PIPING”
Insulation (Local supplied)
Both lines need to be insulated. Use a minimum 0.4”
(10 mm) wall thickness.
Refrigerant charge
Length of refrigerant
pipe connected to
indoor/outdoor unit
Additional refrigerant
16’5” - 98’5”
(5 - 30 m)
None
*98’5” - 246’1”
(30 - 75 m)
Add 0.43 oz/ft (40 g/m) of
refrigerant for piping that exceeds
98’5” (30 m) up to 246’1” (75 m).
*
Caution during addition of refrigerant
Max. amount of additional refrigerant is 1.8 lbs
(800 g).
Charge the refrigerant accurately. Overcharging
may cause serious trouble with the compressor.
*
Minimum refrigerant pipe is 16’5” (5 m).
This may cause a malfunction of the compressor or
other devices.
Metering Device is an electronic EXV (PMV) in
outdoor unit.
■
Connecting power and control
cables (Field supplied)
•
The main power is supplied to the outdoor unit.
The
fi
eld supplied connecting cables from the
outdoor unit to the indoor unit consist for 4 wires
and provides the power for the indoor unit as well as
the communication signal between the outdoor and
indoor unit.
•
System interconnection wire size must be AWG16.
•
Breaker must have a capacity speci
fi
ed in the
following table.
•
All wiring must comply with local electric codes and
NEC (National Electric Code) or CEC (Canadian
Electric Code).
Model RAV-
SP242
Power supply
208/230 V, 60 Hz
MCA
17 A
MOCP (MAX Fuse/CB)
25 A
Breaker
20 A
System interconnection wires
AWG16
Field power supply wire
AWG12
MCA = Minimum Circuit Amps
MOCP = Maximum Over Protection Device Amps.
6
Vacuum
■
Vacuum test
After completing the refrigerant piping work, perform a vacuum test. Connect a nitrogen gas cylinder and
pressurize the pipes with nitrogen gas as follows to conduct the vacuum test.
CAUTION
Never use oxygen, flammable gas,
or noxious gas for the airtight test.
V
L
V
H
Low pressure gauge
Charge port
High pressure gauge
Pressure reducing
valve
Nitrogen gas
Gauge manifold
Gas leak check
Step 1....Pressurize to
0.5 MPa
(5 kg/cm²G) for 5 minutes or longer.
Major leaks can be discovered.
Step 2....Pressurize to
1.5 MPa
(15 kg/cm²G) for 5 minutes or longer.
Step 3....Pressurize to
4.15 MPa
(42 kg/cm²G) for 24 hours. ................ Micro leaks can be discovered.
(However, note that when the ambient temperature differs during pressurization and after 24 hours, the pressure
will change by approximately 0.01 MPa (0.1 kg/cm²G) per 1°C, so this should be compensated.)
If the pressure drops in steps 1 through 3, check the connections for leakage.
Check for leaks with foaming liquid, etc., take steps to fix the leaks such as brazing the pipes again and
tightening the flare nuts, and then perform the airtight test again.
*
After the vacuum test is completed, evacuate the nitrogen gas.
EN
TH
ID
19-EN
20-EN
1131601101 EN FR ES.indb 10
1131601101 EN FR ES.indb 10
4/8/2565 BE 10:14
4/8/2565 BE 10:14