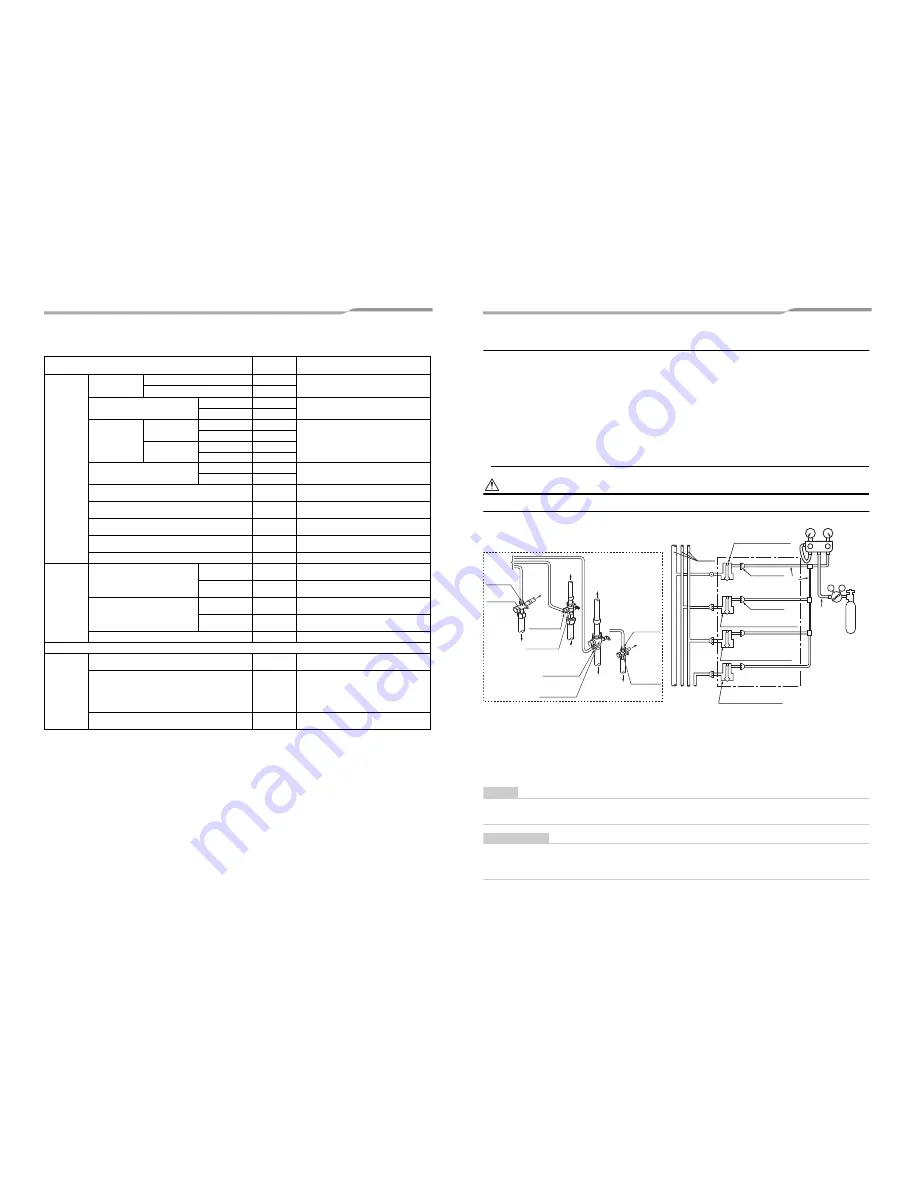
– 15 –
◆
Allowable length and allowable height difference of refrigerant piping
*1: Farthest outdoor unit from the first branch: (C), farthest indoor unit: (o)
*2: Run wires to one indoor unit and flow selector unit linked with one of those remote controllers if flow selector unit is connected to multiple
indoor units.
*3: Allowable values for length equivalent to furthest pipe are shown below and they vary according to performance rank of outdoor unit.
22.4 to 40.0: 185 m, 45.0 to 78.5: 195 m, 85.0 to 118.0: 200 m
*4: When system capacity is greater than 28 HP, height difference between indoor units is limited to 3 m. If the piping exceeds 3 m with a
capacity greater than 28 HP there may be a case of capacity shortage in cooling.
*5: Ensure that the header unit is installed below all connected follower outdoor unit(s).
Possible product failure may occur if header unit is installed above any follower unit(s).
Item
Allowable
value
Pipes
Pipe length
Total extension of
pipe (liquid pipe,
real length)
Less than 34 HP or less
300 m
LA + La + Lb + Lc + L1 + L2 + L3 + L4 + L5 + L6
+ L7 + L8 + a + b + c + d + e + f + g + h + i + j +
k + l + m + n + o
34 HP or more
500 m
Farthest piping length L (*1, *3)
Equivalent length
200 m
LA + Lc + L1 + L3 + L4 + L5 + L6 + L7 + o
Real length
180 m
Max. equivalent
length of Main
piping
H2 > 3 m
Equivalent length
100 m
L1
Real length
85 m
H2
≤
3 m
Equivalent length
120 m
Real length
100 m
Farthest equivalent piping length from
the first branch Li (*1)
H2 > 3 m
50 m
L3 + L4 + L5 + L6 + L7 + o
H2
≤
3 m
65 m
Farthest equivalent piping length between outdoor units L0
(*1)
15 m
LA + Lc (LA + Lb)
Maximum equivalent piping length of pipes connected to
outdoor units
10 m
Lc (La, Lb)
Maximum real length of terminal branching section to
indoor units
30 m
a + f, b + g, c + h, d + l, e + j, k, l
Maximum real length of between Flow Selector unit and
indoor unit
15 m
f, g, h, l, j
Maximum equivalent length between branching sections
50 m
L2, L3, L4, L8
Height
difference
Height between outdoor and indoor
units H1
Upper outdoor
units
50 m
–
Lower outdoor
units
30 m
–
Height between indoor units H2
Upper outdoor
units
40 m
–
Lower outdoor
units (*4)
15 m
–
Height between outdoor units H3 (*5)
5 m
–
<In case of connecting flow selector unit to multiple indoor units>
Maximum equivalent length indoor units in group control by
one Flow Selector unit Ln
30 m
L5 + L6 + L7 + o
Maximum real length between Flow Selector unit and
indoor unit (*2)
15 m
To run wires to indoor unit (m):
L6 + m
≤
15 m, L5 + L6 + L7 + n
≤
30 m,
L5 + L6 + L7 + o
≤
30 m
To run wires to indoor unit (n):
L5 + L6 + m
≤
30 m, L6 + L7 + n
≤
15 m,
L5 + L6 + L7 + o
≤
30 m
Height difference between indoor units in group control by
one Flow Selector unit H4
0.5 m
–
Airtightness test
After the refrigerant piping has been finished, execute an airtight test.
For an airtight test, connect a nitrogen gas canister as shown in the figure below and apply pressure.
• Be sure to apply pressure from the service ports of the packed valves (or ball valves) at the liquid side, discharge
gas side, suction gas side and balance pipe side.
• An airtight test can only be performed at the service ports at the liquid side, gas side and balance pipe side on
header unit.
• Close the valves fully at the gas side, liquid side and balance pipe side. As there is a possibility that the nitrogen
gas will enter into the cycle of outdoor units, re-tighten the valve rods at the liquid side and balance pipe side
before applying pressure.
• For each refrigerant line, apply pressure gradually in steps at the liquid side, discharge gas side, suction gas side
and balance pipe side.
Be sure to apply pressure at the discharge gas side, suction gas side, liquid side, and balance pipe side.
WARNING
Never use oxygen, flammable gases, or noxious gases in an airtight test.
Able to detect a serious leakage
1. Apply pressure 0.3 MPa (3.0 kg/cm²G) for 5 minutes or more.
2. Apply pressure 1.5 MPa (15 kg/cm²G) for 5 minutes or more.
Available to detect slow leakage
3. Apply pressure 3.73 MPa (38 kg/cm²G) for approx. 24 hours.
• If there is no pressure decrease after 24 hours, the test is passed.
NOTE
However, if the environmental temperature changes from the moment of applying pressure to 24 hours after that, the pressure
will change by about 0.01 MPa (0.1 kg/cm²G) per 1 °C. Consider the pressure change when checking the test result.
REQUIREMENT
When pressure decrease is detected in steps 1-3, check the leakage at the connecting points.
Check the leakage using a foaming agent or other measures and seal the leak with re-brazing, flare retightening or other
methods. After sealing, execute an airtight test again.
V
L
V
H
Connected to
indoor unit
Main
piping
Suction gas side
valve fully closed
Low pressure gauge High pressure gauge
Brazed
Header outdoor unit
Fully
closed
Fully
closed
Connected to
other follower units
Balanced pipe side
valve fully closed
Liquid side valve fully closed
Service port
Ø6.4 copper pipe
Ø6.4
copper
pipe
Nitrogen
gas
Reducing
valve
Gauge
manifold
To gauge
manifold
Liquid-side
service port
Packed valve
of balance
pipe side
Service port of
discharge gas side
Piping at
site
Ball valve of
suction gas side
Service port of
suction gas side
Piping
at site
To outdoor unit
To
outdoor
unit
Liquid-side
valve
Packed valve
details
To outdoor
unit
Service port
of balance
pipe side
Fully
closed
Discharge gas side valve fully closed
Service port
To
gauge
manifold
To
outdoor
unit
Ball valve of
discharge gas side
Piping
at site
Piping
at site
29-EN
30-EN
Содержание MMY-MAP0804FT8-E
Страница 37: ...EH99889397 ...