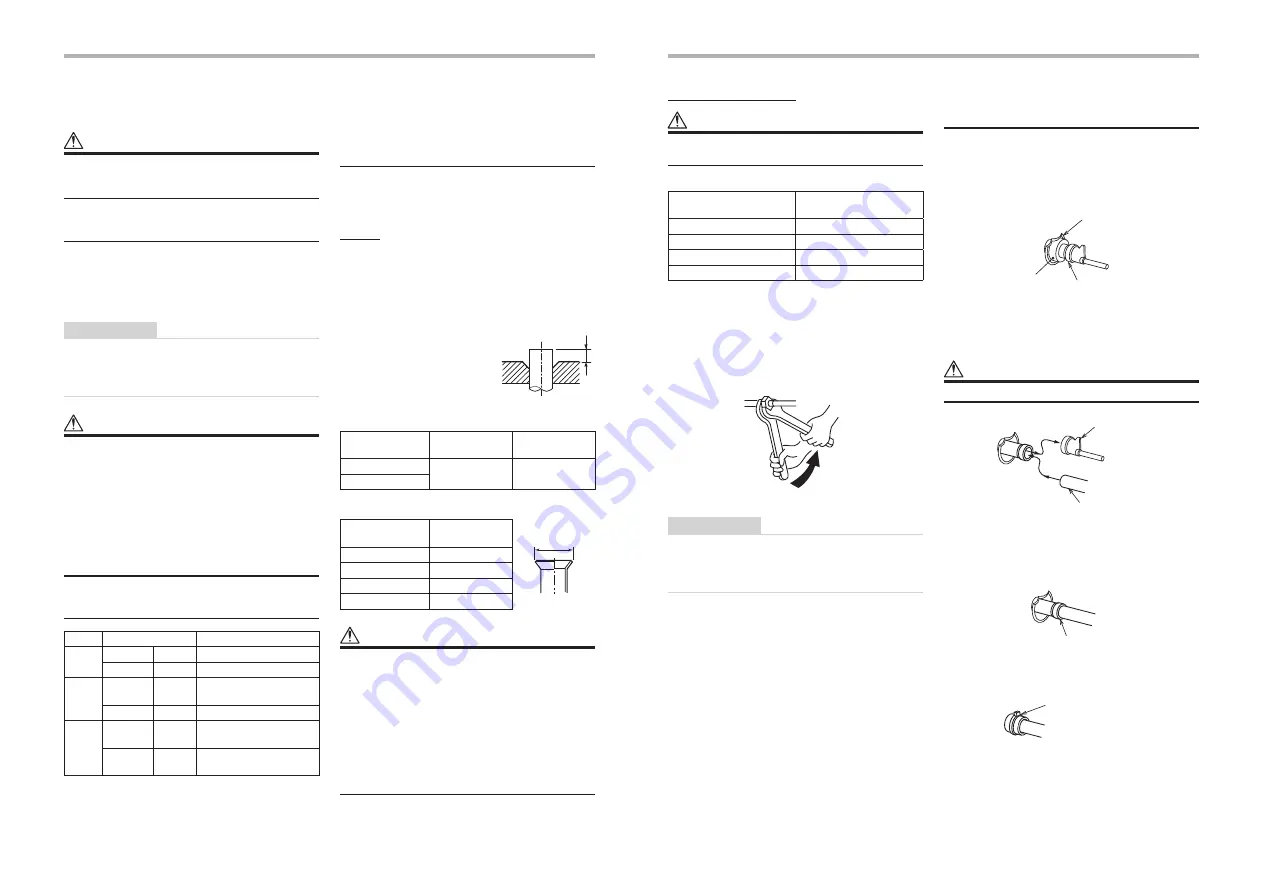
38-EN
37-EN
– 19 –
8
Refrigerant piping
CAUTION
Use
fl
are nuts that are included with the unit. Using
different
fl
are nuts may cause refrigerant gas
leakage.
Refrigerant piping
Use the following item for the refrigerant piping.
Material: Seamless phosphorous deoxidized
copper pipe.
6.35, 9.52 and 12.7 Wall thickness 0.8 mm or more
15.88,wall thickness 1.0 mm or more.
REQUIREMENT
When the refrigerant pipe is long, provide support
brackets at intervals of 2.5 - 3 m to clamp the
refrigerant pipe. Otherwise, abnormal sound may
be generated.
CAUTION
IMPORTANT 4 POINTS FOR PIPING WORK
1. Reusable mechanical connectors and
fl
ared
joints are not allowed indoors. When mechanical
connectors are reused indoors, sealing parts
shall be renewed.
When
fl
ared joints are reused indoors, the
fl
are
part shall be refabricated.
2. Tight connection (between pipes and unit)
3. Evacuate the air in the connecting pipes by
using VACUUM PUMP.
4. Check the gas leakage. (Connected points)
Pipe size
Model
Pipe size
Remarks
0721
0961
A(Gas)
Dia22.2
B(Liquid) Dia12.7
1121
A(Gas)
Dia28.6
Use the SOCKET
(Accessory)
B(Liquid) Dia12.7
1281
A(Gas)
Dia28.6
Use the SOCKET
(Accessory)
B(Liquid) Dia15.9
Use the LIQUID JOINT
PIPE (Accessory)
Permissible piping length and
height difference
They vary according to the outdoor unit.
For details, refer to the Installation Manual attached to
the outdoor unit.
Flaring
1. Cut the pipe with a pipe cutter.
Remove burrs completely.
Remaining burrs may cause gas leakage.
2. Insert a
fl
are nut into the pipe, and
fl
are the pipe.
As
the
fl
aring sizes of R410A differ from those of
refrigerant R22, the
fl
are tools newly manufactured
for R410A are recommended.
However, the conventional
tools can be used by adjusting
projection margin of the copper
pipe.
B
q
Projection margin in
fl
aring: B (Unit: mm)
RIDGID
(Clutch type)
Outside diameter
size (mm)
R410A tool
used
Conventional
tool used
6.4, 9.5
0 - 0.5
1.0 - 1.5
12.7, 15.9
q
Flaring dia. meter size: A (Unit: mm)
Outside diameter
size (mm)
A
+0
-0.4
A
6.4
9.1
9.5
13.2
12.7
16.6
15.9
19.7
CAUTION
y
Do not scratch the inner surface of the
fl
ared part
when removing burrs.
y
Flare processing under the condition of scratches
on the inner surface of
fl
are processing part will
cause refrigerant gas leak.
y
Check that the
fl
ared part is not scratched,
deformed, stepped, or
fl
attened, and that there
are no chips adhered or other problems, after
fl
are processing.
y
Do not apply refrigerating machine oil to the
fl
are
surface.
Tightening connection
CAUTION
Do not apply excessive torque. Otherwise, the nut
may crack depending on the conditions.
(Unit: N•m)
Outside diameter size
(mm)
Tightening torque
6.4 mm
14 - 18
9.5 mm
34 - 42
12.7 mm
49 - 61
15.9 mm
68- 82
q
Tightening torque of
fl
are pipe connections
Incorrect connections may cause not only a gas leak,
but also a trouble of the refrigeration cycle.
Align the centres of the connecting pipes and tighten
the
fl
are nut as far as possible with your
fi
ngers. Then
tighten the nut with wrenches and torque wrench as
shown in the
fi
gure.
Work using two wrenches
REQUIREMENT
Tightening with an excessive torque may crack the
nut depending on installation conditions.
Tighten the nut within the speci
fi
ed tightening
torque.
Gas side refrigerant pipe
connection
y
Be careful of
fi
re when brazing the pipes a bove
the ceiling.
y
Turn up the pipe heat insulator to the unit side.
y
Wrap the pipe with wet cloth.
Turn up pipe heat
insulator
Wet cloth
Remove the all
brazed part.
y
Remove the cup on the gas side piping by using a
burner.
CAUTION
y
Do not burn the pipe heat insulator.
Remove the cap
Connection pipe
Locally procured
Ø22.2 mm
y
Braze the connection piping to the joint part.
(procure locally)
Braze all around
y
Turn back the pipe heat insulator and tie up with a
banding band.
Tie up with a banding
band.