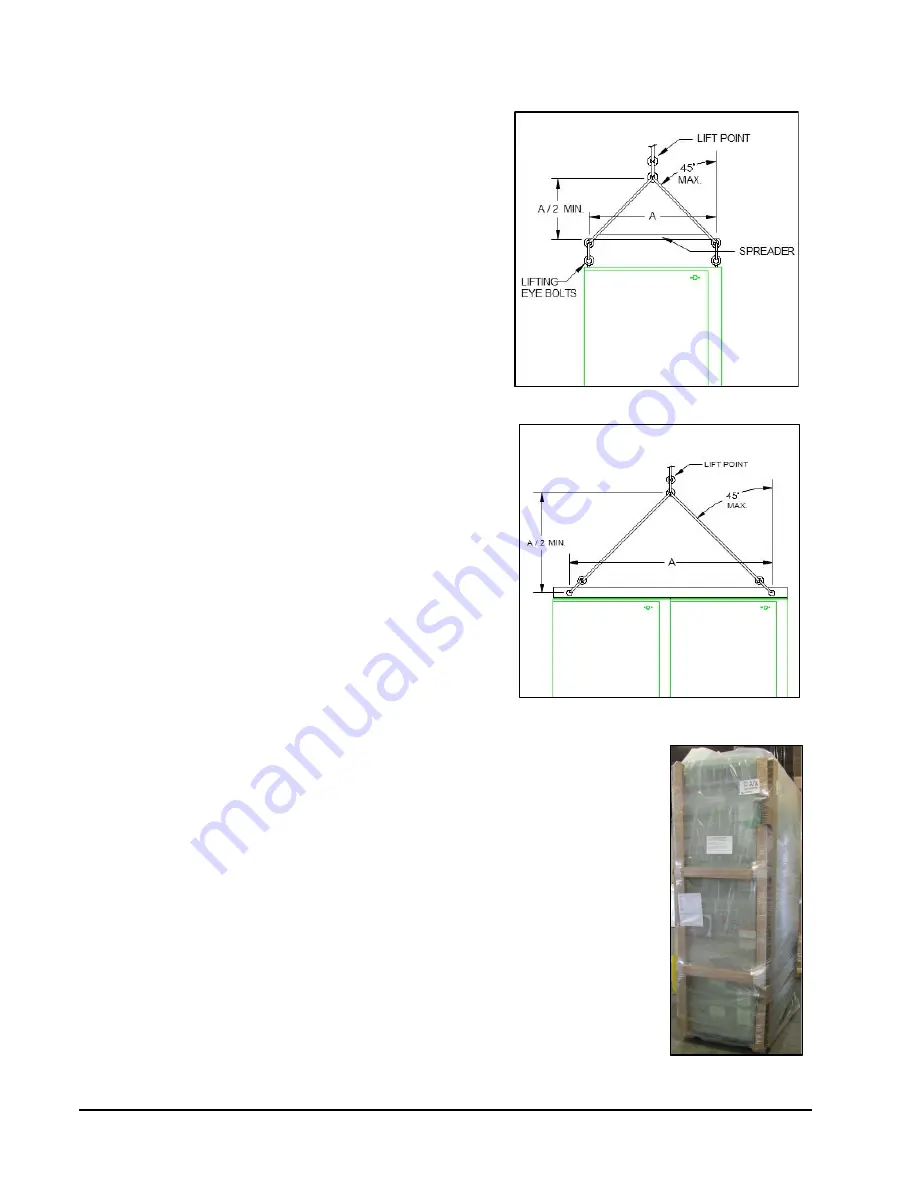
Basic Installation and Operation Guide
JK 400 Series Fixed Controllers
TOSHIBA
2
Overhead Lifting
When it is necessary to move the equipment between
elevations, overhead hoisting may be required. Lifting angles
(for multiple controller sections) are provided on top of the
enclosure for this purpose. Spreaders (Fig.
2) should be used to
provide the vertical lift on single controllers to prevent eye-bolt
failure. Always keep the controller upright while lifting. Some
controller sections may contain heavy or special equipment that
will cause the center of gravity to be off-center. Rigging lengths
should be adjusted to maintain the controller in an upright
position. The angle between the lifting cables and vertical should
not be allowed to exceed 45 degrees (Fig.
3). Ropes or cables
should not pass through the holes in lifting angles or eye-bolts.
Slings with safety hooks or shackles of adequate load rating
should be used.
Fig. 2 Use of Spreader Bar - Single Section
Initial Inspection
•
Make a complete visual check of the unit for damage which
may have occurred during shipping and handling. Do not
attempt to continue installation or start up the unit if it is
damaged.
•
Check for loose mechanical assemblies or broken wires
which may have occurred during transportation or handling.
Loose electrical connections will increase resistance and
cause the unit to function improperly.
•
Prior to beginning the installation, verify that the load and
JK unit are rated for the proper amperage and voltage.
Fig. 3 Lifting Multiple Sections
LOCATION
Storage
If the controller is to be stored for any length of time prior to installation, the packing
should be restored for protection during that period. Where conditions permit, the
packing should be left intact until the controller is at the final installation position. If the
packing
(Fig. 4)
is removed, the top and openings of the controller should be covered
during the construction period to protect it against dust and debris.
Indoor Equipment
Controllers designed for indoor installation (e.g. Type 1, 12) that are not to be installed
and energized immediately should be stored in a clean, dry space where a uniform
temperature prevents condensation. Preferably, the controller should be stored in a
heated building, with adequate air circulation and protected from dirt and water.
Equipment should be stored where it is not subject to mechanical damage, especially
Fig. 4 Storage
Содержание JK400 Series
Страница 2: ...Basic Installation and Operation Guide JK Series 400 Series Fixed Controllers ...
Страница 9: ...Basic Installation and Operation Guide JK 400 Series Fixed Controllers TOSHIBA ...
Страница 46: ......
Страница 47: ......