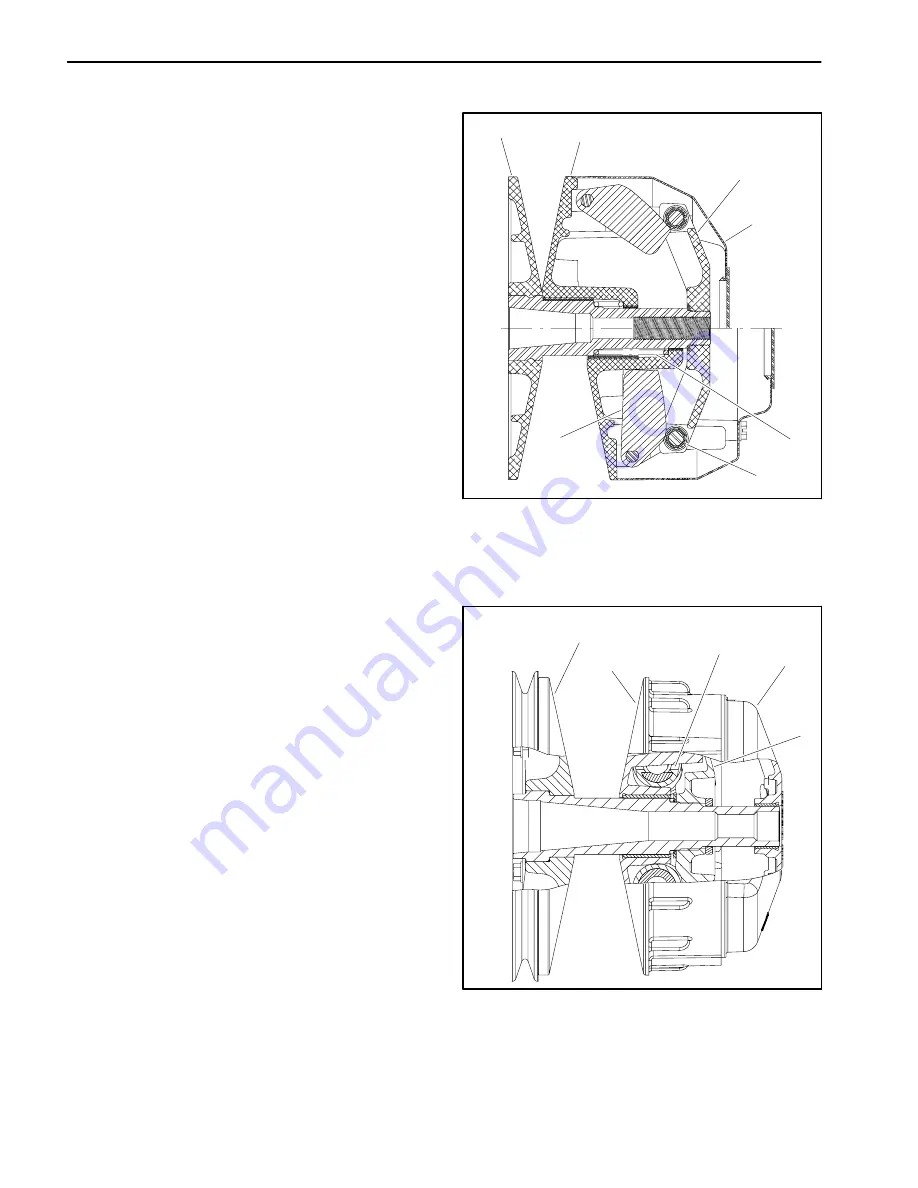
Rev. A
Workman MD/MDX
Drive Train
Page 5 -- 4
Drive Clutch Operation
The operation of the drive clutch is affected by engine
shaft speed. When the engine is off and not turning, the
drive belt rests low within the drive clutch sheaves as the
clutch sheaves are spaced apart. As the engine is
started and increases in speed, the clutch weights move
outward as they spin about the engine drive shaft. The
outward movement of the weights against the spider as-
sembly forces the moveable sheave closer to the fixed
sheave. This inward movement of the moveable sheave
engages the drive belt which begins to rotate.
With increasing engine speed, the moveable sheave
continues to move inward. This sheave movement
forces the drive belt to ride towards the outer diameter
of the drive clutch sheaves which increases the drive
belt speed.
When engine speed is decreased, the weights exert
less force on the moveable sheave. The reduced force
causes the moveable sheave to shift away from the fixed
sheave and slows the drive belt speed. As engine speed
continues to decrease, the drive belt disengages from
the clutch sheaves.
The drive clutch used on vehicles with serial numbers
below 310000000 (Fig. 2) includes three (3) rollers,
three (3) cam weights and a spring to control operation
of the moveable sheave.
The drive clutch used on vehicles with serial numbers
above 310000000 (Fig. 3) controls moveable sheave
operation with six (6) weighted rollers and ramp sur-
faces in the moveable sheave.
1. Fixed sheave
2. Moveable sheave
3. Spider assembly
4. Cover
5. Spring
6. Cam weight (3 used)
7. Roller (3 used)
Figure 2
1
2
3
4
7
5
6
1. Fixed sheave
2. Moveable sheave
3. Spider assembly
4. Cover
5. Roller (6 used)
Figure 3
5
4
3
2
1
Содержание Workman MD
Страница 2: ...Workman MD MDX This page is intentionally blank...
Страница 4: ...Workman MD MDX This page is intentionally blank...
Страница 12: ...0 09375 Workman MD MDX Page 2 2 Product Records and Maintenance Equivalents and Conversions...
Страница 36: ...Workman MDX Page 3 20 Briggs Stratton Gasoline Engine This page is intentionally blank...
Страница 42: ...Workman MD Page 4 6 Single Cylinder Gasoline Engine This page is intentionally blank...
Страница 54: ...Workman MD Page 4 18 Single Cylinder Gasoline Engine This page is intentionally blank...
Страница 62: ...Rev A 6 2 Workman MD MDX Drive Train Page 5 This page is intentionally blank...
Страница 71: ...Rev A 13 2 Workman MD MDX Drive Train Page 5 This page is intentionally blank Drive Train...
Страница 77: ...Rev A 15 2 Workman MD MDX Drive Train Page 5 This page is intentionally blank Drive Train...
Страница 81: ...Workman MD MDX Drive Train Page 5 19 This page is intentionally blank Drive Train...
Страница 135: ...Workman MD MDX Page 6 25 Electrical System This page is intentionally blank Electrical System...
Страница 148: ...Workman MD MDX Page 6 38 Electrical System This page is intentionally blank...
Страница 173: ...Workman MD MDX Page 7 25 Chassis This page is intentionally blank Chassis...
Страница 183: ...Workman MD MDX Page 7 35 Chassis This page is intentionally blank Chassis...
Страница 196: ...Page 7 48 Workman MD MDX Chassis This page is intentionally blank Rev A...
Страница 198: ...Workman MD MDX Electrical Drawings Page 8 2 This page is intentionally blank...
Страница 199: ...Page 8 3 Electrical Schematic Workman MD Solenoid is shown de energized F3 F4 F2 F1 10A 20A 15A 30A AUTO RESETTING...
Страница 200: ...Page 8 4 Electrical Schematic Workman MDX Solenoid is shown de energized F3 F4 F2 F1 10A 20A 15A 30A AUTO RESETTING...
Страница 203: ...Rev A Page 8 7 Main Electrical Harness Drawing Workman MD and MDX Serial Number Below 280999999...
Страница 205: ...Rev A Page 8 9 Main Electrical Harness Drawing Workman MD and MDX Serial Number From 290000001 to 310000800...
Страница 207: ...Rev A Page 8 11 Main Electrical Harness Drawing Workman MD and MDX Serial Number Above 310000800...
Страница 209: ...Rev A Page 8 13 Engine Electrical Harness Workman MD WHITE BLUE BROWN BLACK GREEN BROWN WHITE BROWN...
Страница 210: ...Rev A Page 8 14 Engine Electrical Harness Workman MDX WHITE BLUE BROWN BLACK GREEN BROWN WHITE...