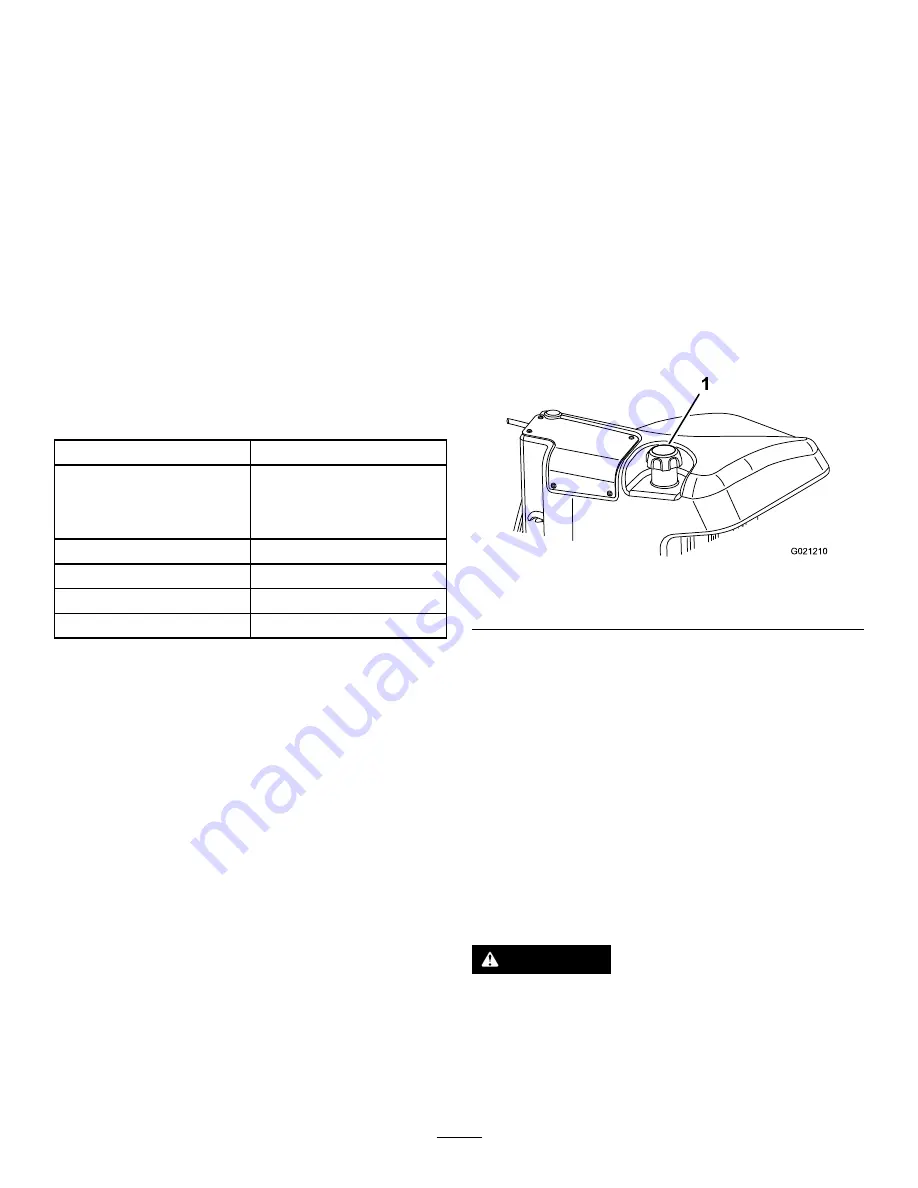
Fuel Specification
Important:
Use only ultra-low sulphur diesel fuel.
Fuel with higher rates of sulfur degrades the diesel
oxidation catalyst (DOC), which causes operational
problems and shortens the service life of engine
components.
Failure to observe the following cautions may damage
the engine.
•
Never use kerosene or gasoline instead of diesel fuel.
•
Never mix kerosene or used engine oil with the diesel
fuel.
•
Never keep fuel in containers with zinc plating on the
inside.
•
Do not use fuel additives.
Petroleum Diesel
Cetane rating:
45 or higher
Sulfur content:
Ultra-low sulfur (<15 ppm)
Fuel Table
Diesel fuel specification
Location
ASTM D975
No. 1-D S15
No. 2-D S15
USA
EN 590
European Union
ISO 8217 DMX
International
JIS K2204 Grade No. 2
Japan
KSM-2610
Korea
•
Use only clean, fresh diesel fuel or biodiesel fuels.
•
Purchase fuel in quantities that can be used within 180
days to ensure fuel freshness.
Use summer-grade diesel fuel (No. 2-D) at temperatures
above -7°C (20°F) and winter-grade fuel (No. 1-D or No.
1-D/2-D blend) below that temperature.
Note:
Use of winter-grade fuel at lower temperatures
provides lower flash point and cold flow characteristics
which eases starting and reduces fuel filter plugging.
Using summer-grade fuel above -7°C (20°F) contributes
toward longer fuel pump life and increased power compared
to winter-grade fuel.
Biodiesel
This machine can also use a biodiesel blended fuel of up to
B20 (20% biodiesel, 80% petroleum diesel).
Sulfur content:
Ultra-low sulfur (<15 ppm)
Biodiesel fuel specification:
ASTM D6751 or EN14214
Blended fuel specification:
ASTM D975, EN590, or JIS
K2204
Important:
The petroleum diesel portion must be
ultra-low sulfur.
Observe the following precautions:
•
Biodiesel blends may damage painted surfaces.
•
Use B5 (biodiesel content of 5%) or lesser blends in
cold weather.
•
Monitor seals, hoses, gaskets in contact with fuel as
they may be degraded over time.
•
Fuel filter plugging may be expected for a time after
converting to biodiesel blends.
•
Contact your authorized Toro distributor for more
information on biodiesel.
Adding Fuel
1.
Park the machine on a level surface, lower the cutting
units, engage the parking brake, shut off the engine,
and remove the key.
2.
Using a clean rag, clean area around fuel-tank cap.
3.
Remove the cap from the fuel tank (
).
g021210
Figure 49
1.
Fuel-tank cap
4.
Fill the tank until the level is 6 to 13 mm (1/4 to 1/2
inch) below the bottom of the filler neck.
5.
Install the fuel-tank cap tightly after filling the tank.
Note:
If possible, fill the fuel tank after each use.
This minimizes possible buildup of condensation
inside the fuel tank.
Performing Daily Maintenance
Service Interval:
Before each use or daily
Before starting the machine each day, perform the Each
Use/Daily procedures listed in
Maintenance (page 49)
.
Checking the Interlock Switches
Service Interval:
Before each use or daily
CAUTION
If safety interlock switches are disconnected or
damaged, the machine could operate unexpectedly,
causing personal injury.
•
Do not tamper with the interlock switches.
•
Check the operation of the interlock switches
daily and replace any damaged switches before
operating the machine.
30