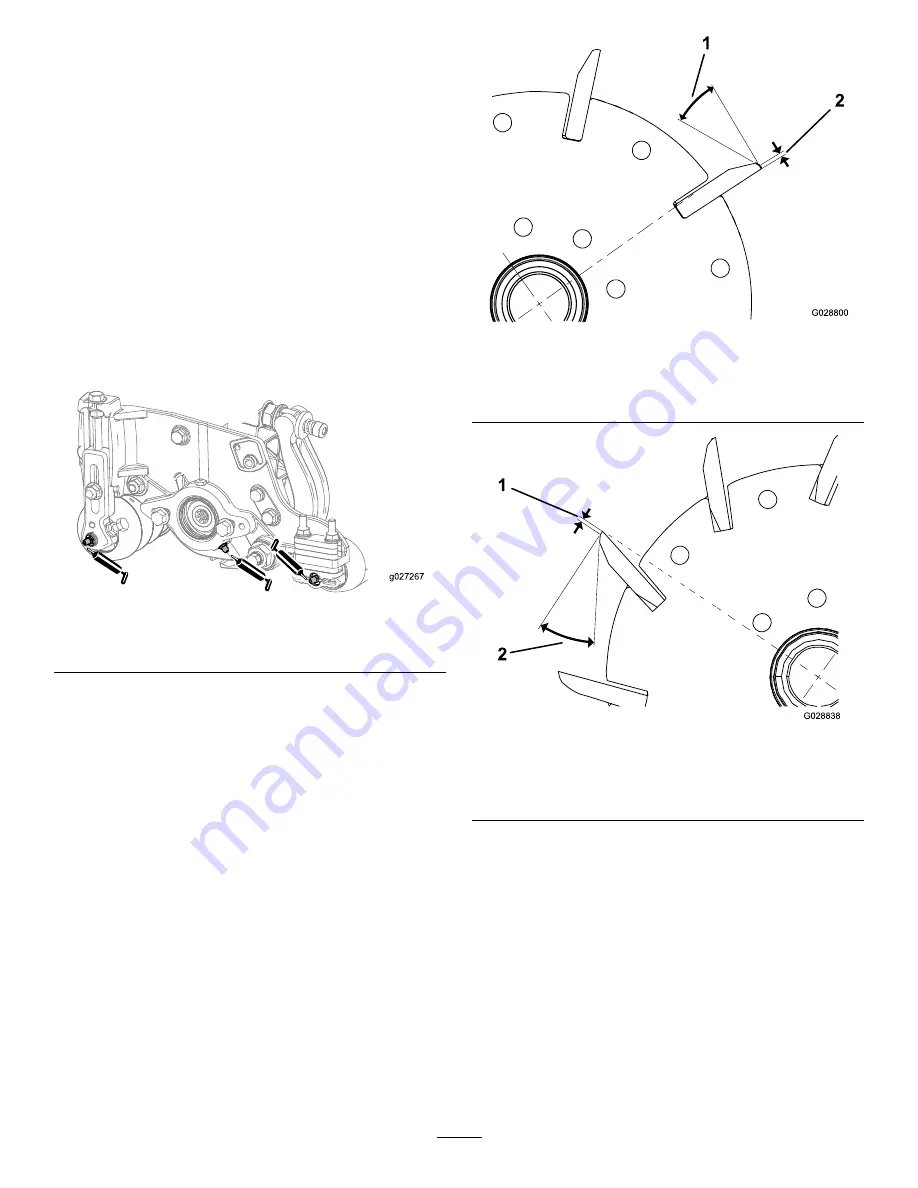
Maintenance
Lubricating the Machine
Regularly lubricate the 5 grease fittings of each cutting
unit (
) with No. 2 lithium grease.
There are 2 lubrication points on the front roller, 2 on
the rear roller, and 1 at the reel-motor spline.
Note:
Lubricating the cutting units immediately
after washing helps purge water out of the
bearings and increases bearing life.
1.
Wipe each grease fitting with a clean rag.
2.
Apply grease until clean grease comes out of
the roller seals and the bearing relief valve.
3.
Wipe any excess grease away.
g027267
Figure 22
Grease fittings on the reel-motor side
Relief-Grinding the Reel
The reel has a land width of 1.3 to 1.5 mm (0.050 to
0.060 inch) and a 30-degree relief grind.
When the land width gets larger than 3 mm (0.120
inch) wide, do the following:
1.
Apply a 30 degree relief grind on all reel blades
until the land width is 1.3 mm (0.050 inch) wide
(
and
).
g028800
Figure 23
Models 03485 and 03487
1.
30 degrees
2.
1.3 mm (0.050 inch)
g028838
Figure 24
Models 03486 and 03488
1.
1.3 mm (0.050 inch)
2.
30 degrees
2.
Spin grind the reel to achieve <0.025 mm (0.001
inch) reel run-out.
Note:
This causes the land width to grow
slightly.
Note:
To extend the longevity of the sharpness of the
edge of the reel and the bedknife—after grinding the
reel and/or the bedknife—check the reel-to-bedknife
contact again after cutting 2 fairways, as any
burrs will be removed, which may create improper
reel-to-bedknife clearance and thus accelerate wear.
16