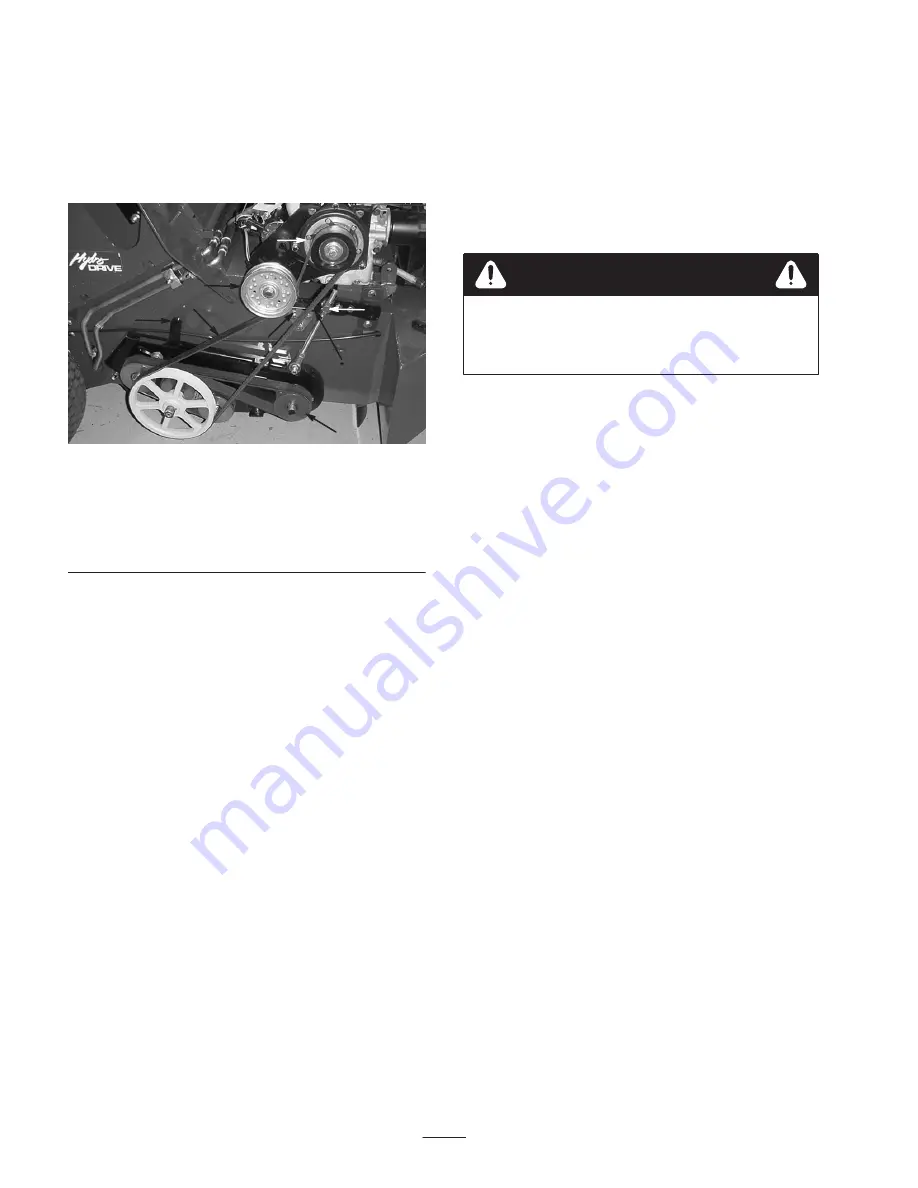
26
6.
Adjust the left–hand side. It is very important that the
left side and right side are adjusted equally (from the
frame). Do not use the floor to adjust the
perpendicularity of the reel shaft to the sweeper frame.
7.
Verify that there is no interference when the PTO
engagement handle is in OFF position.
1
2
3
4
5
6
7
8
Figure 25
1. Reel height adjusting nut
(right hand side)
2. Upper idler
3. Idler adjusting arm
4. Front reel pulley
5. Clutch switch adjustment
6. Electric clutch/brake
7. Upper drive belt
8. Clutch switch flag
Belt Removal/Installation
1.
Position machine on a level surface, shut the engine off,
set the parking brake and remove the key from the
ignition switch.
2.
Remove belt guards.
3.
The upper or lower belt can be removed or installed
without removing both belts.
4.
To remove the upper belt, loosen the upper idler
(Fig. 25) and remove belt from machine.
5.
To install upper belt, first verity that the upper idler
(Fig. 25) is loosened and slides freely. Install belt on
machine. To tighten idler, push down on idler with
approximately 30 lbs. of force and tighten idler bolt. Do
not use a lever for mechanical advantage.
Do not over
tension belt. An over–tensioned belt can cause
premature failure or wear. The electric clutch and
other reel drive components are subject to damage
when belts are over–tensioned.
6.
To remove lower reversing belt, loosen the two bolts on
the rear idler adjustment arm (Fig. 25). Move
adjustment arm forward and remove belt.
7.
To install lower reversing belt, push idler adjustment
arm forward. Install reversing belt.
Note:
The inside and outside of the belt are not the same.
When looking at the front reel pulley (Fig. 25), with the
belt installed, there should be two wide grooves on either
side visible. Tighten the idler adjustment arm by pulling
rearward with approximately 30 lbs. Torque both clamping
bolts to 48 ft–lbs. Do not use a lever or a pry–bar for
mechanical advantage when tensioning the belt with the
idler adjustment arm.
8.
Re–tension new belts after l0 hours of operation.
An incorrectly adjusted reel switch may cause
unintended engagement of the reels and could
cause injury.
Caution
Clutch Switch Adjustment
The clutch switch should never need adjusting. If the clutch
fails to engage or disengage according to the position of the
Reel PTO Engagement Handle, adjust the clutch switch.
1.
Position machine on a level surface, shut the engine off,
set parking brake and remove the key from the ignition
switch.
2.
Inspect the complete reel lift system including the reel
engagement handle. Look for any worn or bent
components that may cause the engagement switch to
be out of adjustment.
3.
Replace or repair any damaged components.
If all reel lift system components are in proper condition,
adjust the reel switch bracket.
1.
Place the PTO engagement handle in the OFF position.
2.
Loosen the three bolts on the clutch switch bracket
(Fig. 25).
3.
Slide the clutch switch bracket until there is 1/8” of the
clutch switch flag (Fig. 25) protruding through the
bottom of the clutch switch bracket.
4.
Tighten the three bolts and reassemble in reverse order.
Electric Brake Clutch
Adjustment
Every 200 hours check for proper air gap on the electric
clutch brake. Failure to maintain the correct air gap could
result in clutch not engaging even though it is electrically
energized.
1.
Position machine on a level surface, shut the engine off,
set the parking brake and remove the key from the
ignition switch.
Содержание 44044
Страница 31: ...31 Hydraulic Schematic...
Страница 32: ...32 Electrical Schematic...