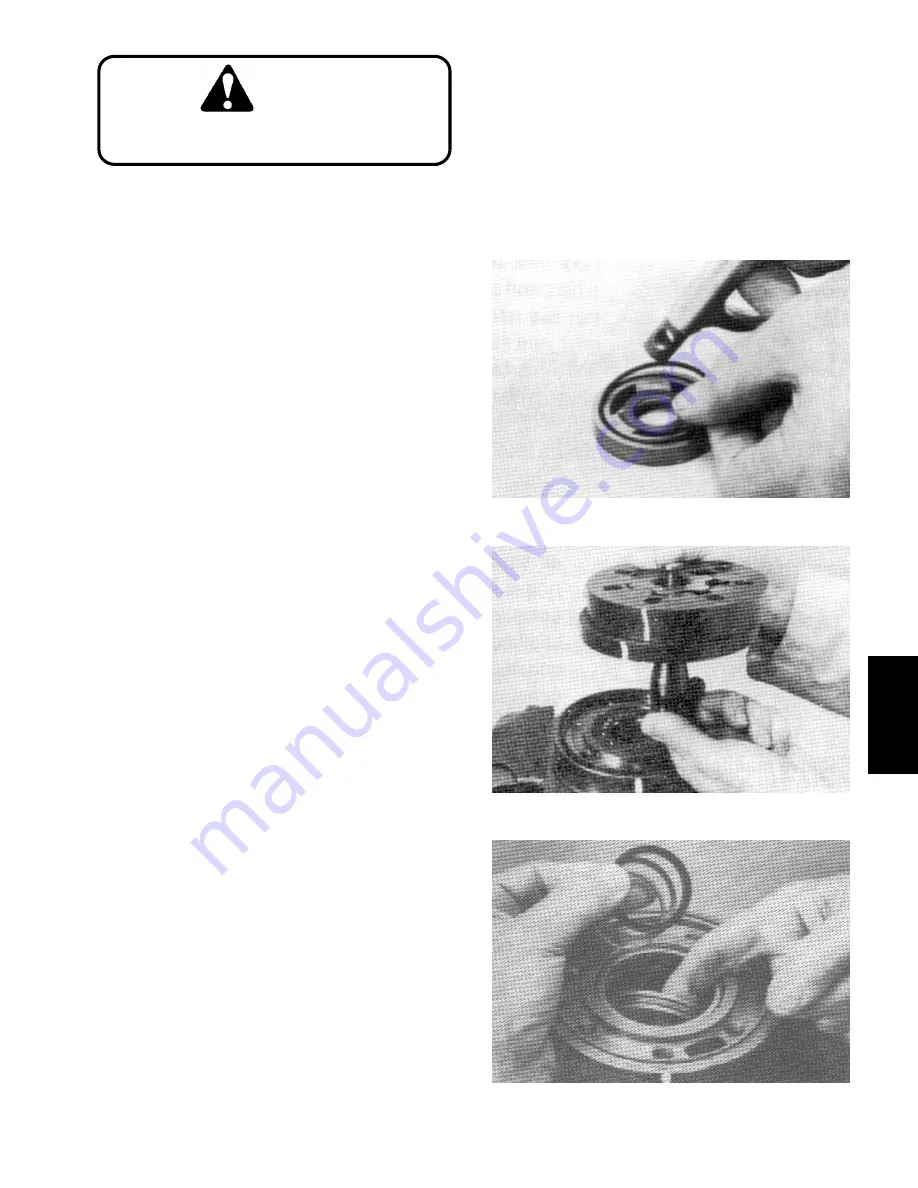
CAUTION
Use eye protection such as goggles when
using compressed air
5. Remove commutator (16) and commutator seal
(15). Remove commutator seal from the commutator
using an air hose to blow air into the ring groove until the
commutator seal is lifted out (Fig. 30).
Note: The manifold (22) is constructed of plates
bonded together to form an integral component not sub-
ject to further disassembly for service. Compare config-
uration of both sides of the manifold to make sure that
the same surface is reassembled against the rotor set.
6. Remove manifold (22). Remove seal rings (5) that
are on both sides of the manifold.
Note: The rotor set consists of the rotor (19), vanes
(20), and stator (21). Rotor set components may be-
come disassembled during service procedures. Do not
serviced separately.
Note: Marking all rotor set components and mating
spline components for exact repositioning at assembly
will make sure maximum wear life and performance of
rotor set and wheel motor.
7. Mark surface of rotor (19) and stator (21) that is fac-
ing up with etching ink or a grease pencil before remov-
ing from the wheel motor. This will make sure correct
reassembly of the rotor into the stator and the rotor set
into wheel motor.
8. Remove rotor set and wearplate (18) together, and
retain the rotor set in its assembled form with the same
vane (20) to stator (21) contact surfaces. The drive link
(13) may come away from the coupling shaft (11) with
the rotor set and wearplate. You may have to shift the ro-
tor set on the wearplate to work the drive link out of the
rotor (19) and wearplate (Fig. 31).
9.
Remove seal ring (5) that is between the rotor set
and wearplate.
10. Remove drive link (13) from the coupling shaft (11)
if it was not removed with rotor set and wear plate (18).
Remove seal ring (5) from housing (3).
11. Remove thrust bearing (12) from the top of the cou-
pling shaft (11).
12. Check exposed portion of coupling shaft (11) to be
sure you have removed all signs of rust and corrosion
which might prevent its withdrawal through the dirt and
water seal (1) and outer bearing (2). Crocus cloth or fine
emery paper may be used.
13. Remove coupling shaft (11); push on the output end
of the shaft.
14. Remove inner seal (7) and back–up washers (4 and
6) from the housing by working them around the un-
seated thrust washers (8) and thrust bearing (9) (Fig.
32). Do not remove the thrust washer.
15. Remove housing (3) from the vise and invert it. Re-
move dirt and water seal (1). A blind hole bearing or seal
puller is required.
Figure 30
Figure 31
Figure 32
Hydraulic
System
Greensmaster 3200/3200–D
Page 5 – 55
Hydraulic System
Содержание 3200
Страница 2: ...Greensmaster 3200 3200 D ...
Страница 4: ...Greensmaster 3200 3200 D ...
Страница 6: ...Greensmaster 3200 3200 D ...
Страница 12: ...Safety Page 1 6 Greensmaster 3200 3200 D ...
Страница 14: ...Equivalents and Conversions Product Records and Maintenance Page 2 2 Greensmaster 3200 3200 D ...
Страница 17: ...Product Records and Maintenance Page 2 6 Greensmaster 3200 3200 D ...
Страница 72: ...Perkins Diesel Engine Page 4 30 Greensmaster 3200 D ...
Страница 113: ...Hydraulic System Greensmaster 3200 3200 D Page 5 41 Hydraulic System ...
Страница 161: ...Hydraulic System Greensmaster 3200 3200 D Page 5 89 Hydraulic System ...
Страница 173: ...Hydraulic System Greensmaster 3200 3200 D Page 5 101 Hydraulic System ...
Страница 234: ...Wheels and Brakes Page 7 12 Greensmaster 3200 3200 D ...
Страница 261: ...Cutting Units Greensmaster 3200 3200 D Page 8 27 Cutting Units ...
Страница 273: ......
Страница 274: ...Commercial Products FORM 96 900 SL E The Toro Company 1997 Printed in U S A ...