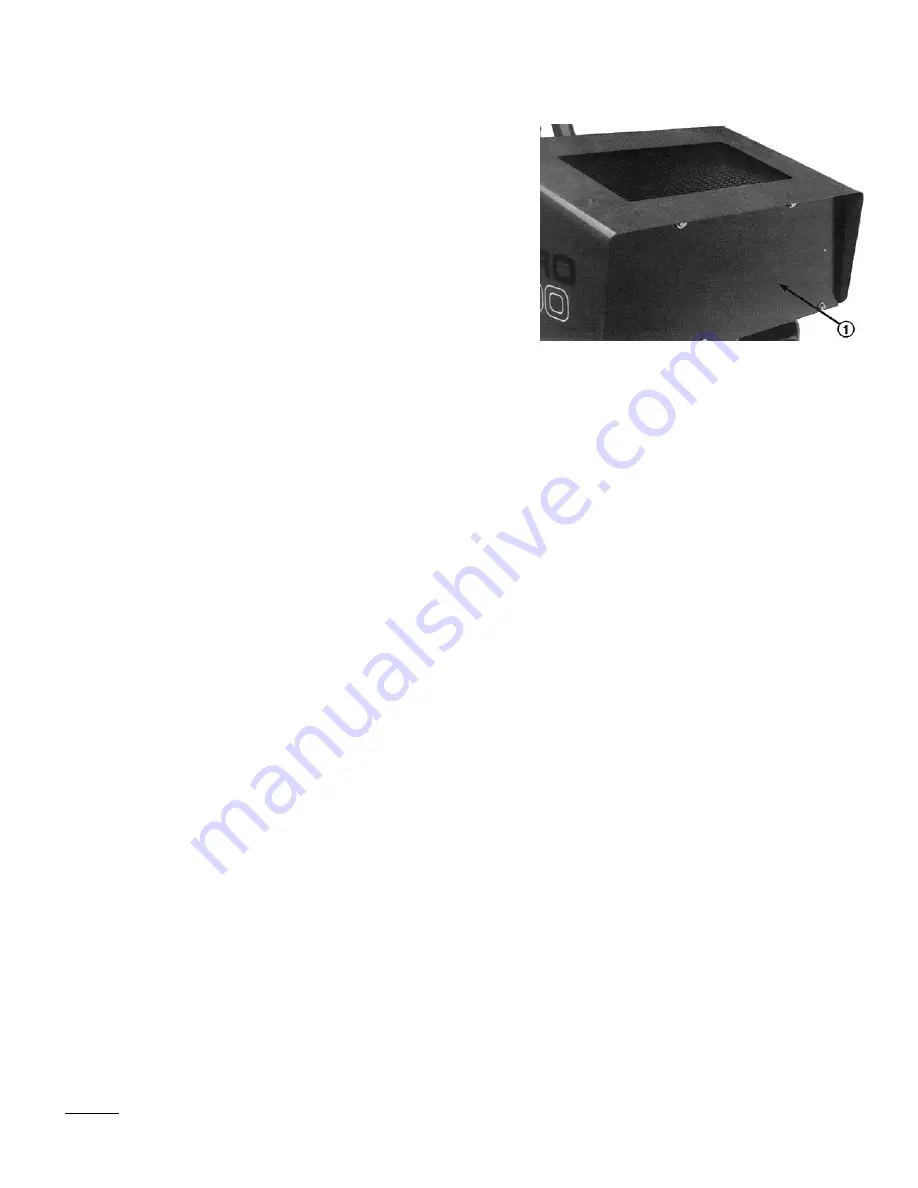
16
Figure 10
1.
Front Panel
LUBRICATION (Fig. 10)
The steering shaft grease fitting must be lubricated regularly with
No. 2 General Purpose Lithium Base Grease.
1.
Remove the (5) screws securing the front panel to the frame
(Fig. 10). Locate grease fitting through the opening in the
frame.
NOTE: We do not recommend lubricating the steering chain
unless it becomes stiff because of rust. If the chain rusts, it may
be lubricated lightly with a DRY-TYPE LUBRICANT.
CHANGING CRANKCASE OIL
For new engines, change the oil after the first 5 operating hours.
Thereafter, under normal conditions, change the oil after every 25
hours of engine operation. However, an engine operated in dusty or
dirty conditions requires more frequent oil changes. If possible, run
the engine just before changing oil. Warm oil flows more freely and
carries more contaminants than cold oil.
1.
Place an oil drain pan below the drain plug on bottom of
crankcase. Clean the area around drain plug.
2.
Remove the drain plug and allow oil to flow into drain pan. After
the oil is drained, reinstall the oil drain plug.
3.
Remove the dipstick/filler cap and pour approximately 2.5 l of
oil having the APl “service classification” SF into the filler neck.
Oil viscosity is selected according to anticipated ambient tem-
perature. Temperature/viscosity recommendations are:
A.
Above 32° F (0°C)—Use SAE 30. The use of multi-weight
oil above 32° F (0°C) is not recommended due to increased
oil consumption an excessive combustion chamber deposits.
B.
Below 32° F (0° C)—Use SAE 5W-20 or 5W-30, and if
they are not available, 10W-30 or 10W-40 are acceptable
substitutes.
4.
Check the oil and make sure the level is up to the FULL mark on
the dipstick. Add more oil if the level is low; however, DO NOT
OVERFILL.
5.
Dispose of oil properly.
Maintenance