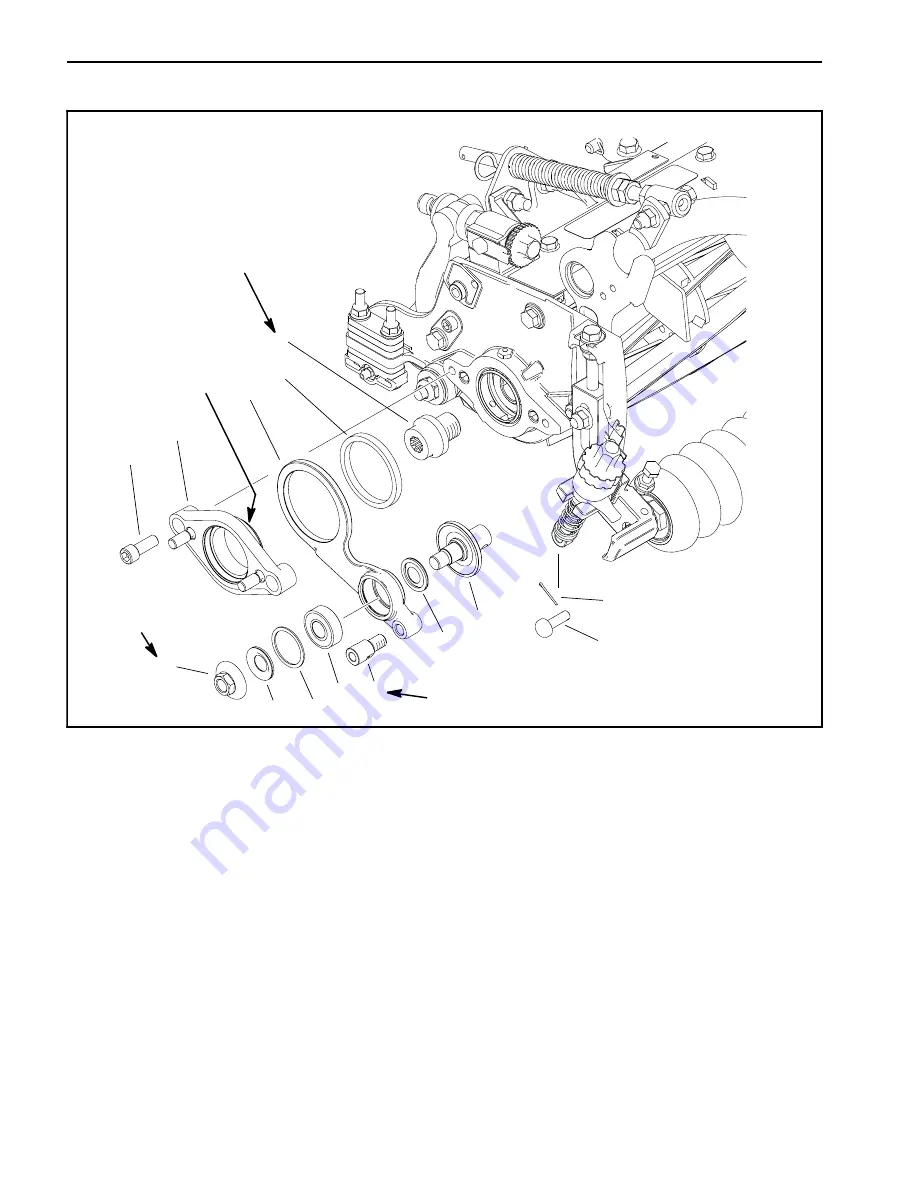
Reelmaster 7000--D
Universal Groomer (Optional)
Page 11 -- 12
Idler Assembly
1
2
3
4
5
6
7
8
9
9
10
13
11
12
Figure 9
1. Socket head screw (2)
2. Pivot hub
3. Idler arm
4. Bushing
5. Threaded insert
6. Cotter pin
7. Clevis pin
8. Stub shaft and shield
9. Bearing shield (2)
10. Bearing
11. Retaining ring
12. Flange nut
13. Collar
Antiseize
Lubricant
85 to 95 ft--lb
(115 to 129 N--m)
Loctite #242
27 to 33 ft--lb
(37 to 45 N--m)
24 to 30 ft--lb
(33 to 41 N--m)
NOTE:
The groomer idler assembly is located on the
same side of the cutting unit as the cutting unit hydraulic
motor.
Removal (Fig. 9)
1. Park machine on a clean and level surface, lower
cutting units completely to the ground, stop engine, en-
gage parking brake and remove key from the ignition
switch.
2. Remove hydraulic reel motor from cutting unit (see
Hydraulic Reel Motor Removal in Chapter 9 -- Cutting
Units in this manual).
3. Remove the groomer reel assembly (see Groomer
reel in this chapter).
4. Remove the cotter pin and clevis pin from the height
adjustment rod at the front of the idler arm. Discard cot-
ter pin.
5. Remove the socket head cap screws securing the
pivot hub to the cutting unit and remove the pivot hub
and idler assembly from the cutting unit.
6. Inspect shields, bearing and bushing in idler assem-
bly. Remove and discard damaged or worn compon-
ents.
Содержание 03781
Страница 1: ...Form No 15214SL Rev D Reelmaster 7000 D Models 03780 A and 03781 Original Instructions EN ...
Страница 4: ...NOTES _ ...
Страница 6: ...Reelmaster 7000 D This page is intentionally blank ...
Страница 8: ...Reelmaster 7000 D This page is intentionally blank ...
Страница 10: ...Reelmaster 7000 D This page is intentionally blank ...
Страница 16: ...Reelmaster 7000 D Page 1 6 Safety This page is intentionally blank ...
Страница 18: ...0 09375 Reelmaster 7000 D Page 2 2 Product Records and Maintenance Equivalents and Conversions ...
Страница 40: ...Reelmaster 7000 D Page 3 18 Yanmar Diesel Engine This page is intentionally left blank ...
Страница 61: ...Reelmaster 7000 D Page 4 15 Kubota Diesel Engine This page is intentionally left blank Kubota Engine ...
Страница 67: ...Reelmaster 7000 D Page 4 21 Kubota Diesel Engine This page is intentionally left blank Kubota Engine ...
Страница 70: ...Reelmaster 7000 D Page 4 24 Kubota Diesel Engine This page is intentionally blank ...
Страница 80: ...Reelmaster 7000 D Hydraulic System Page 5 10 This page is intentionally blank ...
Страница 107: ...Reelmaster 7000 D Hydraulic System Page 5 37 This page is intentionally blank Hydraulic System ...
Страница 113: ...Reelmaster 7000 D Hydraulic System Page 5 43 This page is intentionally blank Hydraulic System ...
Страница 119: ...Reelmaster 7000 D Hydraulic System Page 5 49 This page is intentionally blank Hydraulic System ...
Страница 123: ...Reelmaster 7000 D Hydraulic System Page 5 53 This page is intentionally blank Hydraulic System ...
Страница 131: ...Reelmaster 7000 D Hydraulic System Page 5 61 This page is intentionally blank Hydraulic System ...
Страница 135: ...Reelmaster 7000 D Hydraulic System Page 5 65 This page is intentionally blank Hydraulic System ...
Страница 139: ...Reelmaster 7000 D Hydraulic System Page 5 69 This page is intentionally blank Hydraulic System ...
Страница 151: ...Reelmaster 7000 D Hydraulic System Page 5 81 This page is intentionally blank Hydraulic System ...
Страница 155: ...Reelmaster 7000 D Hydraulic System Page 5 85 This page is intentionally blank Hydraulic System ...
Страница 169: ...Reelmaster 7000 D Hydraulic System Page 5 99 This page is intentionally blank Hydraulic System ...
Страница 173: ...Reelmaster 7000 D Hydraulic System Page 5 103 This page is intentionally blank Hydraulic System ...
Страница 187: ...Reelmaster 7000 D Hydraulic System Page 5 117 This page is intentionally blank Hydraulic System ...
Страница 195: ...Reelmaster 7000 D Hydraulic System Page 5 125 This page is intentionally blank Hydraulic System ...
Страница 203: ...Reelmaster 7000 D Hydraulic System Page 5 133 This page is intentionally blank Hydraulic System ...
Страница 205: ...Reelmaster 7000 D Hydraulic System Page 5 135 This page is intentionally blank Hydraulic System ...
Страница 209: ...Reelmaster 7000 D Hydraulic System Page 5 139 This page is intentionally blank Hydraulic System ...
Страница 226: ...Reelmaster 7000 D Hydraulic System Page 5 156 This page is intentionally blank ...
Страница 230: ...Reelmaster 7000 D Page 6 4 Electrical System This page is intentionally blank ...
Страница 263: ...Reelmaster 7000 D Page 6 37 Electrical System This page is intentionally blank Electrical System ...
Страница 299: ...Reelmaster 7000 D Page 7 5 Axles Planetaries and Brakes This page is intentionally blank Axles Planetaries and Brakes ...
Страница 311: ...Reelmaster 7000 D Page 7 17 Axles Planetaries and Brakes This page is intentionally blank Axles Planetaries and Brakes ...
Страница 315: ...Reelmaster 7000 D Page 7 21 Axles Planetaries and Brakes This page is intentionally blank Axles Planetaries and Brakes ...
Страница 337: ...Reelmaster 7000 D Page 8 3 Chassis This page is intentionally blank Chassis ...
Страница 349: ...Reelmaster 7000 D Page 8 15 Chassis This page is intentionally blank Chassis ...
Страница 354: ...Reelmaster 7000 D Page 8 20 Chassis This page is intentionally blank ...
Страница 369: ...Reelmaster 7000 D DPA Cutting Units Page 9 15 This page is intentionally blank DPA Cutting Units ...
Страница 391: ...Reelmaster 7000 D DPA Cutting Units Page 9 37 This page is intentionally blank DPA Cutting Units ...
Страница 413: ...Reelmaster 7000 D Belt Driven Groomer Optional Page 10 9 This page is intentionally blank Belt Driven Groomer ...
Страница 425: ...Reelmaster 7000 D Universal Groomer Optional Page 11 5 This page is intentionally left blank Universal Groomer ...
Страница 440: ...Reelmaster 7000 D Universal Groomer Optional Page 11 20 This page is intentionally left blank ...
Страница 451: ...Page 12 11 Reelmaster 7000 D Main Wire Harness Drawing Model 03780 30781 Serial numbers below 316000000 ...
Страница 458: ...Page 12 18 122 1729 Rev A Reelmaster 7000 D Main Wire Harness Diagram Model 03780 03781 Serial numbers above 405700000 ...
Страница 459: ...Page 12 19 Reelmaster 7000 D Engine Wire Harness Drawing Model 03780 Yanmar Engin ...
Страница 461: ...Page 12 21 Reelmaster 7000 D Engine Wire Harness Drawing Model 03781 Kubota Engine ...
Страница 463: ...Page 12 23 Reelmaster 7000 D Seat and Console Wire Harness Drawing Model 03780 30781 ...
Страница 465: ...Page 12 25 Reelmaster 7000 D Power Center Wire Harness Drawing Model 03780 30781 Serial numbers below 403350000 ...