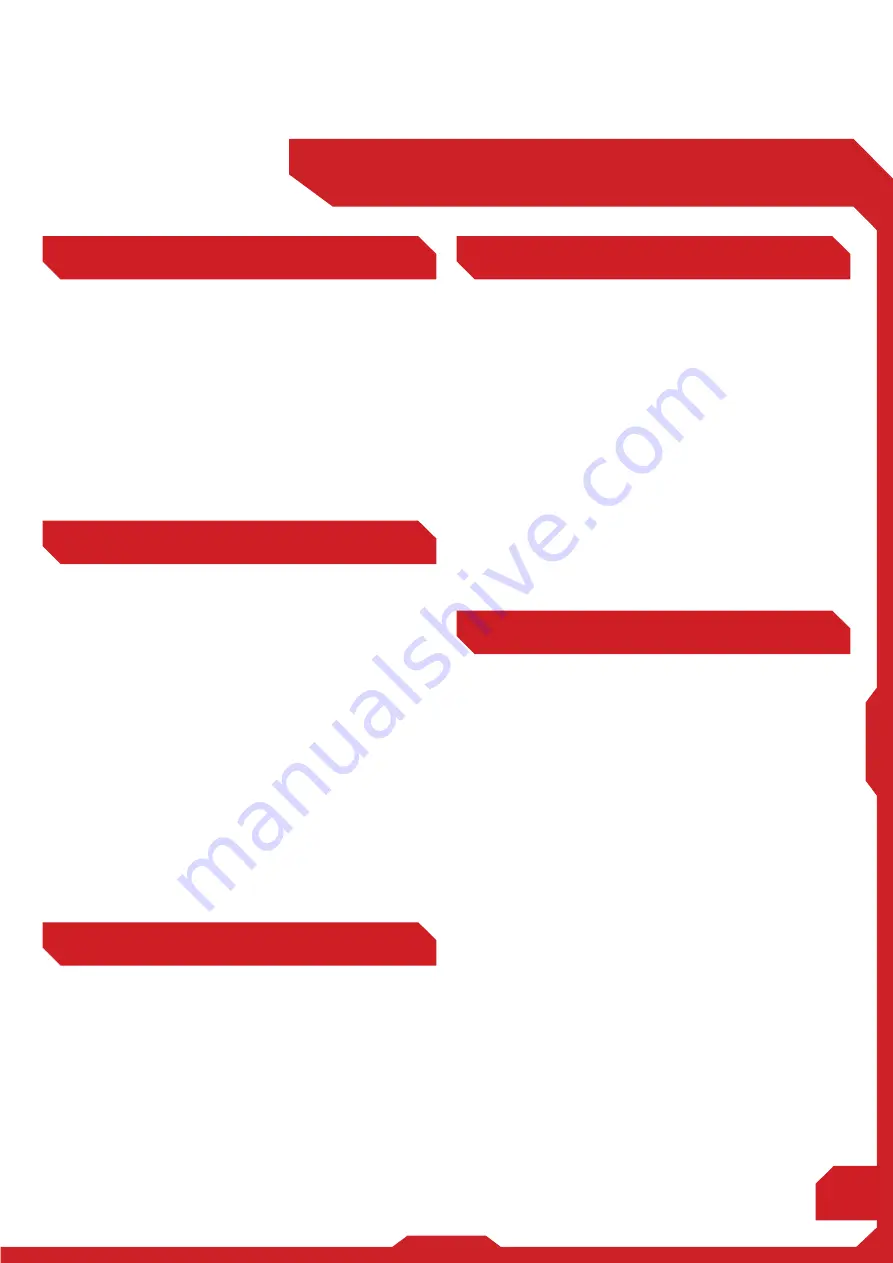
5
ARC Welding Technique
FOR BEGINNERS
A Word To Beginners
Striking An Arc
Arc Length
The Welder
Rate of Travel
For those who have not yet done any welding, the simplest way to
commence is to run beads on a piece of scrap plate. Use a mild
steel plate, around 6mm thick and a 3.2mm electrode.
Clean any paint, loose scale or other contaminants from the plate,
and set it firmly on the workbench so that welding can be carried
out in the downhand position.
Make sure that the work clamp is making good electrical contact
with the work piece, either directly or through the work table.
For light gauge material, always clamp the work lead directly to
the job, otherwise a poor circuit may result.
Practice this on a piece of scrap plate before going on to more
exacting work. You may at first experience difficulty due to the
tip of the electrode “sticking” to the workpiece. This is caused by
making too heavy a contact with the work and failing to withdraw
the electrode quickly enough. A low amperage will accentuate
this. The freezing-on of the tip may be overcome by scratching the
electrode along the surface of the workpiece in the same way a
match is struck.
As soon as the arc is established, maintain a 1.6mm to 3.2mm gap
between the burning electrode end and the parent metal. Draw
the electrode slowly along as it melts down.
Another difficulty you may encounter is the tendency that after
the arc is “struck”, to withdraw the electrode so far that the arc is
broken again.
A little practice will remedy both the aforementioned faults.
The securing of an arc length necessary to produce a neat weld,
soon becomes almost automatic.
You will find that a long arc produces more heat. A very long arc
produces a crackling or spluttering noise and the weld metal
comes across in large, irregular blobs. The weld bead is flattened
and spatter will increase.
A short arc is essential if a high quality weld is to be obtained
although if it is too short, there is the danger of it being blanketed
by slag and the electrode tip being solidified in.
If this should happen, give the electrode a quick twist back over
the weld to detach it. Contact or “touch-weld” electrodes do not
stick in this way, and make welding much easier.
Place yourself in a comfortable position before beginning to weld.
Get a seat of suitable height and do as much work as possible
sitting down comfortably. Don’t hold your body tense. A taut
attitude of mind and a tense body will soon make you feel tired.
Relax and you will find that the job becomes much easier. You
can add much to your peace of mind by wearing a leather apron
and gauntlets. You won’t be worrying then about being burnt or
sparks setting your clothes alight.
Place the work so that the direction of welding is across, rather
than to or from your body. The electrode holder lead should be
clear of any obstructions so that you can move your arm freely
along as the electrode burns down. If the lead is slung over your
shoulder, it allows greater freedom of movement and takes a lot
of weight off your hand.
Be sure the insulation on your cable and electrode holder is not
faulty, otherwise you are risking an electric shock.
After the arc is struck, your next concern is to maintain it, and this requires moving the electrode tip towards the molten pool at the same
rate as it is melting away. At the same time, the electrode has to move along the plate to form a bead. The electrode is directed at the pool
at about 20’ from the vertical plane.
The rate of travel has to be adjusted so that a well-formed bead is produced. If the travel is too fast, the bead will be narrow and strung out
and may even be broken up into individual globules. If the travel is too slow, the weld metal piles up and the bead will be too large.
Содержание ARC 145WR
Страница 1: ...Manual Guide TOPGUNWELDING COM AU MMA STICK WELDER ARC 145WR ARC 186WR Manual Guide TOPGUNWELDING COM...
Страница 2: ......
Страница 15: ...This page has been intentionally left blank...
Страница 16: ......