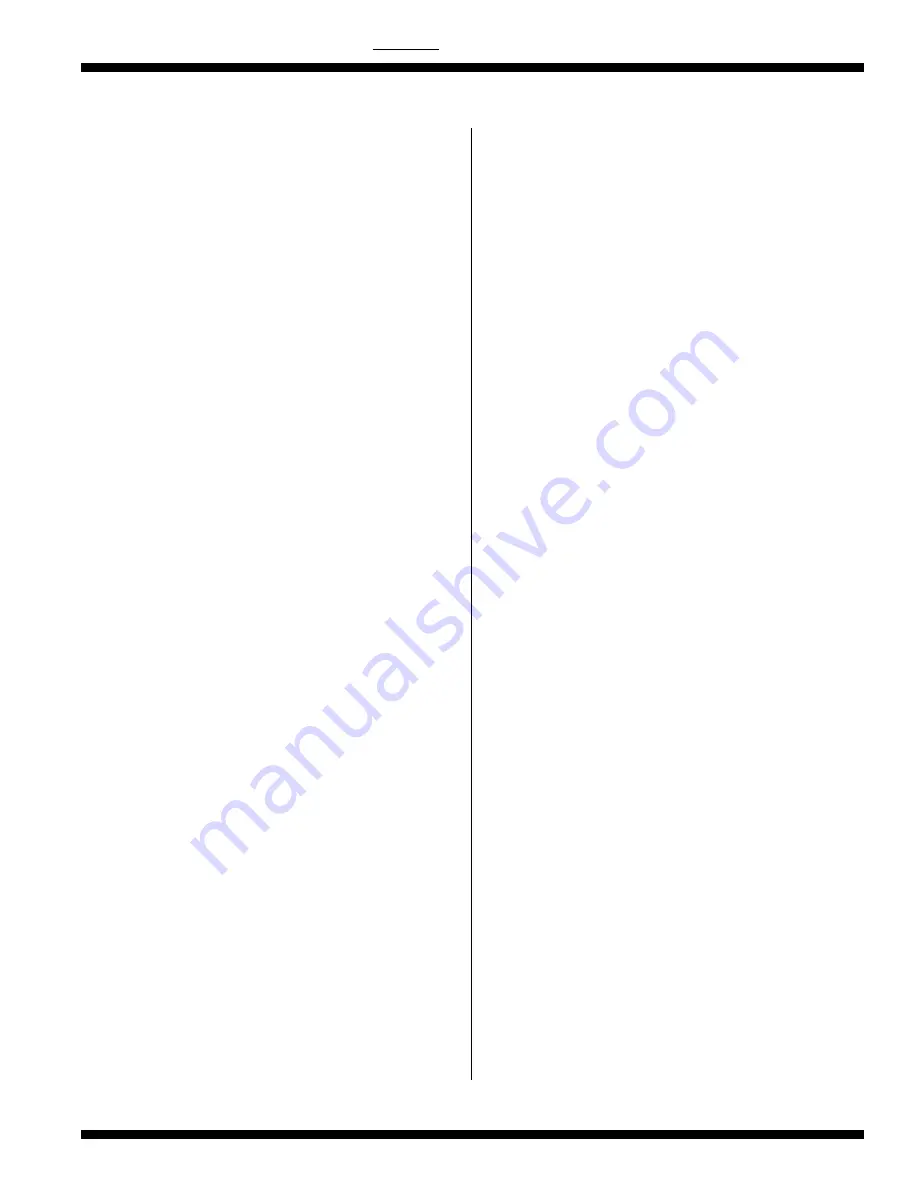
Tolomatic • URL: http://www.tolomatic.com • Email: [email protected] • Fax: (763) 478-8080 • Toll Free: 1-800-328-2174
Disassembly and Assembly Instructions
POWER-BLOCK2 DISASSEMBLY
1. To remove the Tooling Plate (#4) and Shafts (#21 or #23) first remove
the Button Head Screw (#2). Note, for later reassembly, that the cupped
surface of the Belleville Spring (#3) faces toward the Tooling Plate. Pull
on the Tooling Plate (#5). The Tooling Plate and Shafts (#21 or #23) will
slide out of the assembly.
2. Push Head (#8) into bore to expose a gap between Head and Retaining
Ring (#7). To remove the Head use a screwdriver to remove the
Retaining Ring. The Head is now free to be removed.
3. Remove the Piston/Piston Shaft Assembly from the Base (#16). Loosen
Socket Flat Head Screw (#15) to remove the Piston Shaft (#10) from the
Piston (#13). When removing the two U-Cups (#11) from the Piston
note that the flare of the U-Cups face away from each other. In looking
at the piston from the side view the two U-Cups form a “V” shape.
4. Push Cap (#18) into bore to expose a gap between Cap and Retaining
Ring (#7). Using a screwdriver remove the Retaining Ring from the Cap
side of the Base (#16). Remove the Cap from the Base.
5. To remove the Linear Bearings (#20) or the Composite Bearings (#22)
use a screwdriver to remove the two Retaining Rings (#19) from the
shaft bores of the Base (#16). The Bearings (#20 or #22) may now be
pushed out, with a screwdriver.
POWER-BLOCK2 ASSEMBLY PROCEDURE
Clean work bench and area, check that all parts are there and without any
visual damage or defects.
1. Base Assembly
PB208 and PB210 Models
(Composite and Linear Bearings) By hand press new Composite
Bearing (#22) or Linear Bearing (#20), outside chamfered side down,
into each of the two bearing bores in the Base (#16). Press an addition-
al Bearing (#22) or (#20) outside chamfered side down, into the same
two bearing holes in the Base. Bearing must be recessed to allow for
retaining ring. Using a ring spreader insert two Retaining Rings (#19) to
retain the Bearings.
PB217 Models
(Composite Bearings) Press new Composite Bearing (#22), outside
chamfered side down, into each of the two bearing bores in the Base
(#16). Press an additional Bearing (#22) outside chamfered side down,
into the same two bearing holes in the Base with an arbor press until
the bearing is flush with the front surface of the base.
(Linear Bearings) Place new Linear Bearing (#20) into each of the bear-
ing bore holes in the Base (#16). Place second Linear Bearing into each
of the bearing bore holes. Install the Retaining Rings (#19) into the
grooves in the bores to hold the Bearings in place.
2. Cap Assembly
a. Thoroughly lubricate the center bore of the base.
b. Apply Loctite #495 to the recess in the Cap (#18) then press in the
Bumper (#17) with the grooves in the Bumper facing away from the
Cap.
c. Install an O-Ring (#9) into the cap. Place a thin coat of Magnalube
®
-G
over the O-Ring. Push the Cap (#18); Bumper side in, into the counter-
bore on the back side of the Base (#16). (Note: the mounting holes on
the base are closest to the front side.)
d. Install a Retaining Ring (#7) in the groove behind the Cap (#18).
3. Piston Assembly
PB208, PB210 and PB217 Models
a. Install the two U-Cups (#11) into the two grooves on the Piston (#13)
with the flares of each U-Cup facing away from each other.
b. Apply Loctite #271 to the Piston Shaft (#10) threads and screw Shaft
into the end of the Piston (#13) which is counterbored. Hand tighten.
c. Apply Loctite #271 to the Socket Head Flat Screw (#15) and attach the
Magnet to the Piston (#13) with secured Shaft and tighten nut with the
appropriate hand wrench. DO NOT OVERTIGHTEN.
d. Place a Bumper (#12) over the Piston Shaft (#10) so that the flat side is
against the Piston.
e. Place a thin coat of Magnalube
®
-G on the Piston Shaft (#10) and
U-Cups (#11).
f. Push the Piston Rod assembly, Piston first, into the front side of the
center bore on the Base (#16).
PB220 Models
a. Apply Loctite #271 to the Socket Flat Head Screw (#15) and attach the
Piston (#13) to the flat end of the Piston Shaft (#10).
b. Install the two U-Cups (#11) into the two remaining grooves in the
Piston (#13) note that the flare of the U-Cups must face away from
each other. In looking at the piston from the side view the two U-Cups
form a “V” shape.
c. Place a Bumper (#12) over the Piston Shaft (#10) so that the flat side is
against the Piston (#13)
d. Place a thin coat of Magnalube
®
-G on the Piston Shaft (#10) and the
U-Cups (#11).
e. Push the Piston/Piston Shaft Assembly, Piston first, into the front side of
the center bore of the Base (#16).
4. Head Assembly
a. Lubricate the Quad Ring (#6) with Magnalube
®
-G and insert into the
center of the Head (#8).
b. Press the Retaining Ring (#7) flush into the center of the Head (#8).
c. Install an O-Ring (#9) onto the Head. Place a thin coat of
Magnalube
®
-G over the O-Ring and Quad Ring (#6). Guide the Head
over the Piston Shaft (#10) and push the Head (#8), flat surface in, into
the counterbore on the front side of the Base (#16).
d. Install a Retaining Ring in the groove in the counterbore in front of the
Head (#8).
5. Tooling Plate and Bearing Rod Installation
PB208 and PB210 Models
a. Clean the Hex Nut (#5) and Socket Head Flat Screw (#15) and apply
Loctite #242 to the Piston Shaft (#10) threads
b. Attach the Tooling Plate (#4) to the Piston Shaft (#10) with the Hex Nut
and Shoulder Nut. The Shoulder Nut goes on the outside of the Tooling
Plate. Adjust the position so that the end of the piston shaft is flush with
the outer surface of the Hex Nut. Tighten with the appropriate wrench-
es.
PB217 Models
a. On units with Composite Bearings only, apply a small amount of
Magnalube
®
-G into the bearings on the base. No additional lubricant is
needed with the Linear Bearings. Insert the Guide Shafts (#21 or #23)
with the drilled and tapped holes towards the Tooling Plate (#4) through
the bearings. Apply Loctite #271 to the threads of the two SHCS (#1)
and attach the Tooling Plate to the Guide Shafts (#21 or #23).
b. Apply Loctite #242 to the threads of the Button Head Screw (#2).
Attach the Tooling Plate (#4) to the Piston Shaft (#10) with the Button
Head Screw and Belleville Spring (#3). Note that the cupped surface of
the Belleville Spring (#3) faces toward the Tooling Plate. Tighten all
screws.
c. Cycle the assembly back and forth by hand to seat the Bumpers, End
Cap and Head.
6. Switch Option
Clamp for switch will fit in either of the two grooves on the top (porting)
side of the Base (#16). Secure Switch to the Base with Clamp and Set
Screw. Note the scored surface of the Switch housing should face the
base of the Power-Block2.
NOTE:
Form A Reed Switches should not be used in TTL logic cir-
Parts Sheet #2500-4012_07_PB208_10_17ps
PB208, PB210, PB217
Instructions – 3
Parts Sheet #2500-4012_07_PB208_10_17ps