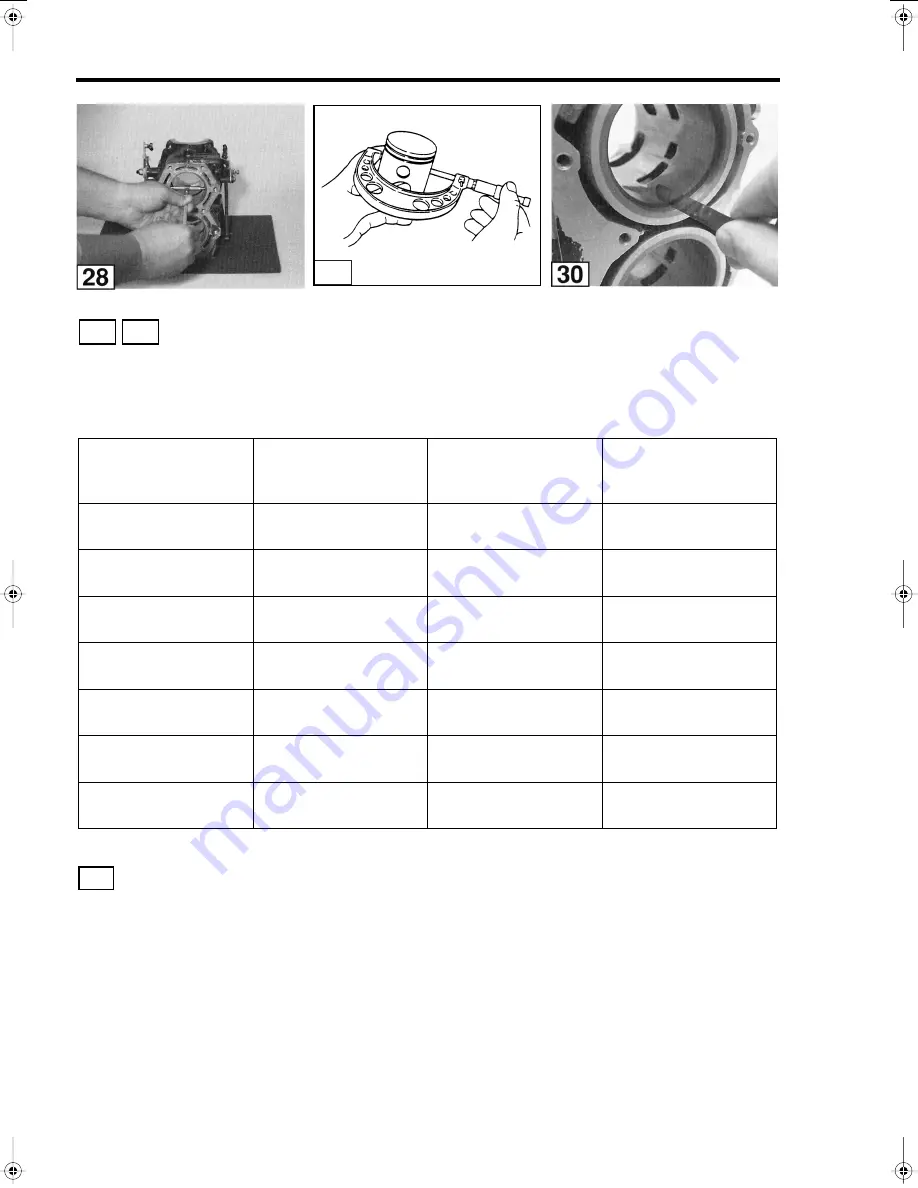
SECTION 4
4-32
1-/ 2-Cylinder
7. Measure and record the diameter of each cylinder
bore and the outside diameter of its respective piston.
Subtract the values to calculate the piston clearances. lf any bore
diameter or piston clearance exceeds the specified limit, the cylinder
must be professionally bored oversize for use with an oversize piston.
8. Complete the following inspection for new or used piston
ring sets. Inspect each ring separately:
• Place ring in its respective cylinder bore.
• Use a piston to square the ring in the bore.
• Use the thickness gauge set (Part No. 353-72251-0) to measure
the ring end gap.
Model
Standard
Bore Diameter
in [mm]
Standard
Piston Clearance
in [mm]
Repair Limit
Piston Clearance
in [mm]
2.5 / 3.5
1.85 [47]
0.0024 - 0.0035
[0.06 - 0.09]
0.006 or over
[0.15 or over]
5
2.16 [55]
0.008 - 0.020
[0.02 - 0.05]
0.006 or over
[0.15 or over]
8 / 9.8
1.97 [50]
0.008 - 0.020
[0.02 - 0.05]
0.006 or over
[0.15 or over]
9.9 / 15
2.16 [55]
0.0020 - 0.0035
[0.05 - 0.09]
0.006 or over
[0.15 or over]
18
2.36 [60]
0.0020 - 0.0035
[0.05 - 0.09]
0.006 or over
[0.15 or over]
25 / 30
2.68 [68]
0.0024 - 0.0039
[0.06 - 0.10]
0.006 or over
[0.15 or over]
40
2.76 [70]
0.0020 - 0.0039
[0.05 - 0.10]
0.006 or over
[0.15 or over]
28 29
30
T2027
T2028
29
T1235
Содержание 2 Stroke Cylinder Series
Страница 1: ...PNo 003 21035 1 0509 NB 1000 Printrd in Japan 1 05 8 23 1 33 PM 1...
Страница 99: ...SECTION 4 4 18 1 2 Cylinder T2201 16...
Страница 103: ...POWERHEAD 4 23 1 2 Cylinder POWERHEAD Typical 1 Cylinder T1676...
Страница 104: ...SECTION 4 4 24 1 2 Cylinder Typical 2 Cylinder T1677...
Страница 140: ...SECTION 5 5 22 1 2 Cylinder 8 T1620...
Страница 162: ...SECTION 6 6 10 1 2 Cylinder GEARCASE Typical Gearcase 2 5 3 5 T1709...
Страница 165: ...GEARCASE 6 13 1 2 Cylinder Typical Gearcase 3 5B T1714...
Страница 169: ...GEARCASE 6 17 1 2 Cylinder Typical Gearcase 8 9 8 9 9 15 18 25 30 40 T1723...
Страница 214: ...SECTION 7 7 22 1 2 Cylinder Ignition System Performance Testing Flow Chart 1 T1557 1...