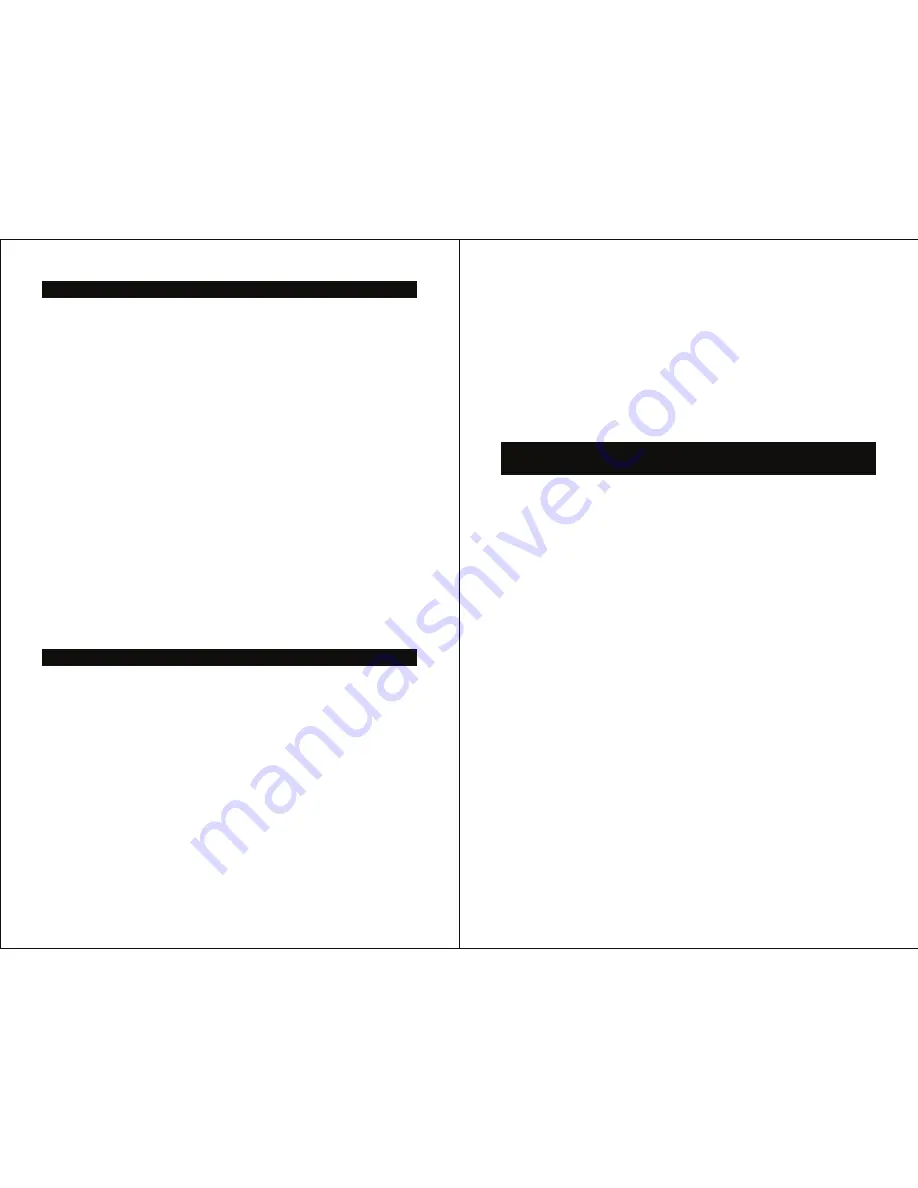
12
13
15.0 SUB-CONTRACTOR DEVELOPMENT
With the increasing demands of Tippmann
®
’s customers for higher
quality at a lower cost, the entire supply chain is responsible for
increasing quality and contribution to a lower overall cost. By
developing and improving sub-contractors, Tippmann
®
’s external
production suppliers could obtain substantial savings to themselves
and ultimately, to Tippmann
®
.
It is Tippmann
®
’s expectations that all approved Tippmann
®
external
production suppliers work closely with their supply base to insure
that the quality level of received product meets our requirements
and expectations.
The primary area of focus is in the communication and documentation
of customer requirements, which is achieved through APQP
(Advanced Product Quality Planning).
Through the APQP process, the subcontractor is informed of customer
requirements and expectations and develops the process foundation.
Tippmann
®
conducts Quality Reviews (QR) meetings at the
Tippmann
®
production facility and corporate levels. Top problem
suppliers are required to attend and present containment / corrective
actions and are identified based on the following:
• Performance History of Repetitive Quality Issues
• Responsiveness to Concerns
• Severity of Issues
• Warranty Issues
16.0 COST RECOVERY POLICY
External Production Suppliers are liable for all costs (as outlined
below) incurred by Tippmann
®
when the root cause is determined to
be the supplier’s responsibility.
• EXTERNAL PRODUCTION SUPPLIERS –
Charges to external
production suppliers will be based on rates of $75.00 (US) per hour.
Refer to the guidelines below regarding applicable chargeback’s to
external suppliers.
• ADMINISTRATIVE CHARGE -
Each Supplier Discrepancy Report
(SDR) has an administrative charge of 2 hours minimum covering
the collection of data and documentation of the quality incident/spill.
• OTHER CHARGES -
the following types of charges will be
calculated on the actual time incurred for the associated action:
EXAMPLES OF COSTS THAT CAN BE CHARGED BACK TO
THE SUPPLIER:
• Rework / Repair Supplier Fault
•Premium Freight Costs including Air Charter if Required
•Overtime to Avoid Production Interruption
•Disposition of Supplier Fault Scrap
•Production Down Time for Tippmann
®
and Customer Charge Backs
•Sorting of Suspect Material In-House, at Customer Location or
Third Party Warehouse and Contractor Costs
•On-line Containment
•Tear-Down (Minor, Major, and Complete) and Outside Lab Testing
•Customer Returns including Hourly Charges, Transportation and
On-Site Inspection Services
•Receiving Inspection, Material Handling and Freight Associated
with Scrap and Replacement Material
17.0 QUALIFICATION / DEVELOPMENT OF ALL DIRECT
MATERIAL SUPPLIERS
Process Steps
• Supplier downloads the
Supplier Self Assessment Survey
from
• Supplier prints out and fills in the Supplier Self Assessment Survey
and E-mails it to:
• Quality, Diversity, Environmental, and any other Certifications are
submitted by supplier
• A Dunn & Bradstreet Report may be generated
• On-site audits/visits may be scheduled
• A Master Supplier Agreement may be initiated
17.1 Evaluation
Commodity Manager makes qualification decision. If the supplier is
qualified, a new supplier request is generated. If the supplier is not
qualified, the information is filed in Corporate Supply Chain files.
17.2 Supplier Status
Suppliers currently in our system and newly qualified suppliers will
be defined as follows:
Preferred
• Qualified supplier meeting qualification objectives
• Given first opportunity at manufacturing new parts
Probationary
• New supplier with no history at Tippmann Sports
• Current supplier requiring additional inspections or qualifications
• Actively working on corrective actions to improve
Disqualified
• Failure to meet performance expectations
• Failure to respond and work through Corrective Actions
Reference Supplier Qualifications Matrix for further detail
www.tippmann.com/usa/cust_service/supplier.aspx.