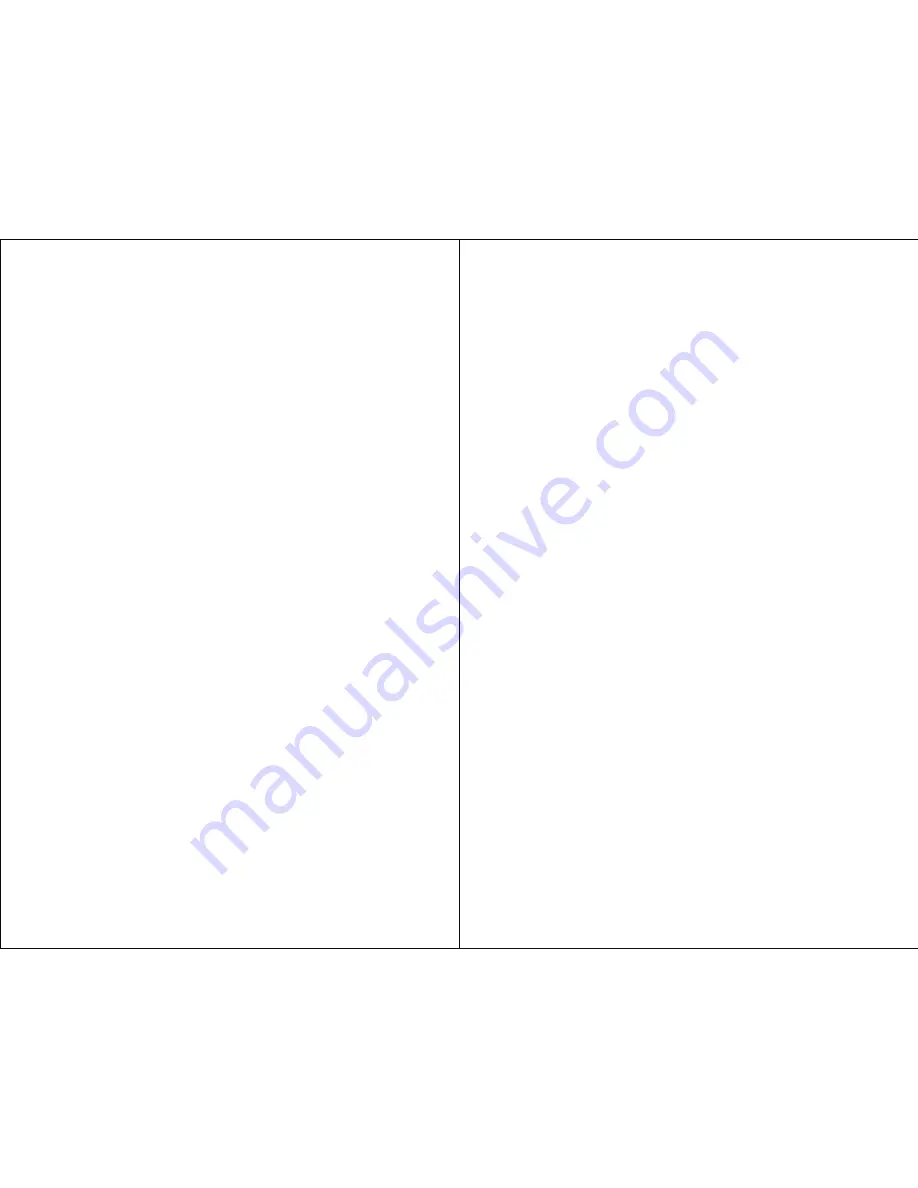
10
11
• New product / complexity for Tippmann
®
• Product Environmental Impact
• Past product / process concerns
• Supplier launch history
• Impact on final product
• New supplier production location
• Past warranty concerns
• New supplier
• New product / process for supplier
• Mergers, Acquisitions or Affiliations associated with a Supplier
14.2 Component Review Meeting (CRM):
Component Review Meetings are held with selected sub-suppliers
to identify key product/process characteristics that are statistically
monitored to ensure stability. Suppliers are required to conduct
CRM’s with their own sub-suppliers to highlight/identify customer
specific requirements.
14.3 Production Part Approval Process (PPAP):
All suppliers must provide evidence of product data submission
acceptance by Tippmann
®
with every PPAP submission, or as
requested. The part numbers in the acceptance note must match
the part numbers submitted for PPAP or other approval. PPAP or
other approvals will not be granted for the parts not accompanying
this documentation. Tippmann
®
suppliers are responsible for
cascading this requirement and collecting data from their respective
sub-suppliers. Failure to do so will be reflected in the supplier’s
monthly scorecard performance as measured in “Customer
Satisfaction.”
14.3.1
All external production suppliers are required to obtain full
approval from Tippmann
®
, according to the latest revision level.
14.3.2
Annual PPAPs are required to verify continuing conformance
on all parts & components unless waived
in writing
by Tippmann
®
.
• At that time, all PPAPs over one year old are to be updated UPON
WRITTEN REQUEST from Tippmann
®
.
14.4 Supplier Document / Process Review:
All external production suppliers are required to complete and return
a Supplier Document and Process Review sheet for each
representative part number that is scheduled to launch for the current
year at the supplier’s manufacturing location.
• It is the responsibility of the Tippmann
®
Engineer and the supplier
to identify each representative part number that will be supported
by the Supplier Document and Review sheets prior to PPAP
submission (reference 14.6).
• The cross-functional Tippmann
®
Program Team identifies high risk
suppliers and Document and Process Reviews are conducted by
the Engineer.
• It is a Tippmann
®
requirement that
the supplier will perform
similar
Supplier Document and Process Review audits with their sub
suppliers and provide that information to Tippmann
®
upon request.
• Tippmann
®
Engineering has the authority to request this information
or conduct an on site Supplier Document and Process Review audit
at any time for existing parts produced by a supplier for Tippmann
®
.
The Supplier Document and Process Review is utilized to
demonstrate a supplier’s compliance to and the continued
improvement of their overall product quality plan.
14.5 Pre-Launch Production Trial Run:
• All suppliers are required to perform a Run @ Rate prior to PPAP,
to verify that the supplier’s actual production process is able to
meet program volumes at an acceptable quality level.
• Tippmann
®
Supplier Development will coordinate the Run @ Rate
with the supplier in accordance with Tippmann
®
Run @ Rate
Procedures.
• The supplier’s process must be able to produce 115% of the quoted
volume using production tools and equipment and within the actual
manufacturing site and process.
• Suppliers are required to assure that Run @ Rate is conducted for
all sub-suppliers and provide supporting documentation to
Tippmann
®
upon request.
14.6 Launch Support:
During any program launch at a Tippmann
®
production facility,
selected suppliers may be required to provide on-site representation.
The supplier’s launch support representative must be knowledgeable,
capable and empowered to make decisions. Coverage must be
provided for all shifts.
• Suppliers will be selected based on past quality performance and
or complexity of components or assemblies being supplied.
• Any component or assembly that is identified as a safety or critical
item or contains any special record retention requirements must
have additional inspection implemented prior to Tippmann
®
receiving
the component or assembly for launch. Each component or
assembly shipment must be certified for 30 days or 6 shipments of
defect free product, which ever is the longest period of time. It is
the responsibility of Tippmann
®
Quality to approve part
certification plans.
• Supplier’s may be required to attend key event builds prior to
production launch.