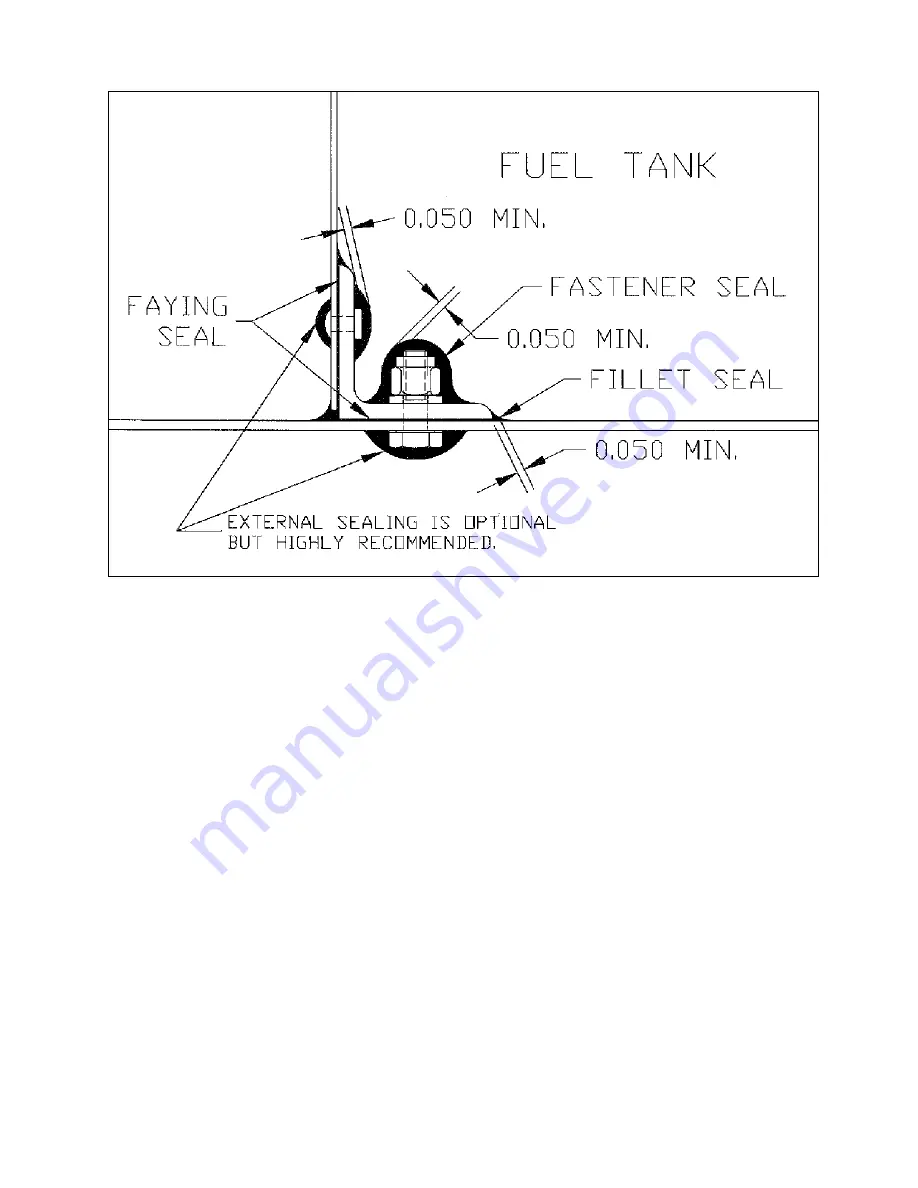
THRUSH AIRCRAFT INC – MODEL S2R R1340
AIRCRAFT MAINTENANCE MANUAL
5-10
Effective: 01/01/08
Figure 5-4: Proper Application of Fuel Proof Sealant
When working with fuel tank sealer,
cleanliness is mandatory. Something as
simple as a fingerprint or a piece of lint
can result in a fuel tank leak down the
road. Rule one is to get all the cutting,
drilling, grinding, etc. out of the way
before you start trying to seal. Having to
add a hole after sealing has begun is a
recipe for a leak. Deburr all holes and
edges and clean out all shavings.
Faying seals involve a layer of “B” type
sealant between mating surfaces.
Sealant is spread on both mating
surfaces before joining. If working on
mating surfaces that are pried apart, use
a pressure applicator to be sure sealant
gets all the way between the mating
surfaces where they are still attached.
When the fasteners are tightened,
starting at one end and working to the
other, the faying sealant is squeezed out
along the edges. If a small bead does
not squeeze out, not enough sealant was
used. Ideally the faying seal should end
up .015” or about 1/64” thick.
Fillet seals are continuous lines of
sealant along the joints between two
parts. The bead squeezed out from the
faying seal is a good start, and may be
sufficient when formed into a fillet. If the
bead material is not enough to get the
coverage thickness specified in Figure 5-
4, add more “B” sealant. Use a tool or a
latex gloved finger for smoothing, not a
bare finger. Do not try to clean up
excess sealant with solvent.
LEAK SEALING
Determine the approximate location of
the leak by visual inspection through the
cover plates in the lower surface of the
wing. After leak area is determined,
drain all fuel from affected tank. See
Section 2 for defueling procedures.
Содержание S2R-R1340
Страница 180: ...THRUSH AIRCRAFT INC MODEL S2R R1340 AIRCRAFT MAINTENANCE MANUAL 8 4 Effective 01 01 08 Figure 8 1 Pitot Static System...
Страница 201: ...THRUSH AIRCRAFT INC MODEL S2R R1340 AIRCRAFT MAINTENANCE MANUAL Effective 01 01 08 9 7 Figure 9 5 Agitator and Spreader...
Страница 216: ...THRUSH AICRAFT INC MODEL S2R R1340 AIRCRAFT MAINTENANCE MANUAL 10 14 Effective 01 01 08 Figure 10 2 Stall Warning System...
Страница 220: ...THRUSH AICRAFT INC MODEL S2R R1340 AIRCRAFT MAINTENANCE MANUAL 10 18 Effective 01 01 08 Figure 10 2 Starting System...
Страница 221: ...THRUSH AICRAFT INC MODEL S2R R1340 AIRCRAFT MAINTENANCE MANUAL Effective 01 01 08 10 19 Figure 10 2 Engine Ignition...
Страница 222: ...THRUSH AICRAFT INC MODEL S2R R1340 AIRCRAFT MAINTENANCE MANUAL 10 20 Effective 01 01 08 Figure 10 2 Power Distribution...