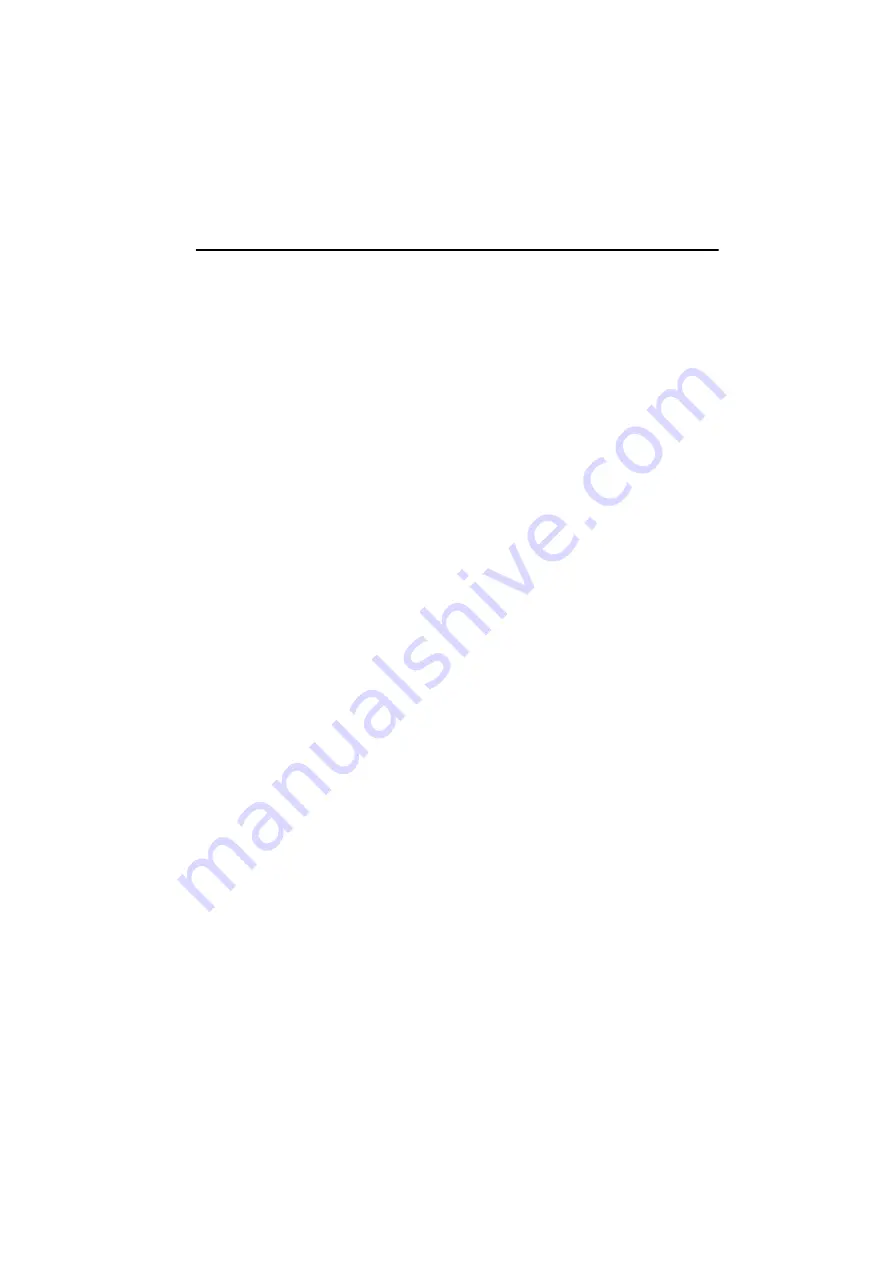
7+25/$%6
Products and Customer Support
Optical and Opto-mechanical
Components
Optical mounts and rails
Lenses, prisms and filters
Polarization-optics
Laser diodes
Standard and specialized optical fibers
Optics, laser & fiber accessories
Test- and Measurement Systems
High precision current and TEC
controllers for laser diodes
Highly stable, tunable laser diodes with
integrated electronics
Optical powermeters
Fabry-Perot interferometer and spectrum
analyzers
Polarization analyzer and controller
systems
Optical Tables and Vibration Control
Optical tables and protection systems
Vibration damping systems
Optical breadboards and vibration
isolated workstations
Nanopositioning Systems
Manual, motor- and piezo-driven
translators, stages and mounts
Electronic stepper motor and piezo
controllers
Integrated multi-axis positioning systems
at sub-micron to nanometer scale
Laser Systems
External cavity laser sources
Ultra broadband laser sources
Femtosecond laser sources
Optical amplifiers
HeNe lasers
Technical Support
Thorlabs provide a comprehensive after
sales service. Contact us through your
local representative, or at the address
below:
Thorlabs Ltd
Saint Thomas Place
Ely
Cambridgeshire CB7 4EX, UK
Tel: +44 (0) 1353 654440
Fax: +44 (0) 1353 654444
email: [email protected]
Product Warranty
All Thorlabs products are covered by a
manufacturers warranty against faulty
workmanship and materials, valid for 12
months from the date of original purchase.
All products returned under warranty must
be returned in their original packaging.
Prior to installation, the equipment
referred to in this handbook must be
stored in a clean, dry environment, in
accordance with any instructions given.
Periodic checks must be made on the
equipment’s condition.
Customer Feedback
It is always helpful to have detailed and
accurate information about any problems
encountered by customers
We welcome comments or suggestions
about any aspect of the equipment and
instruction handbooks.