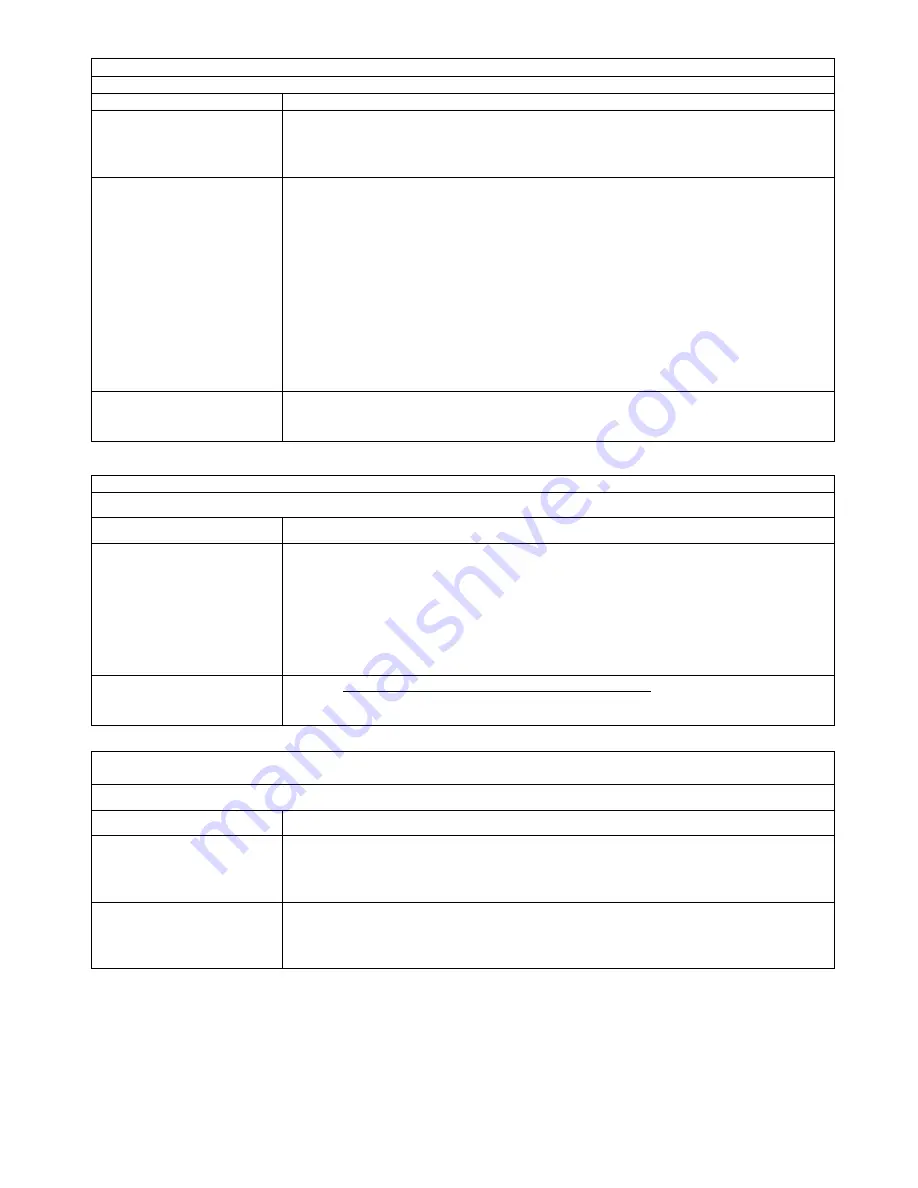
31 .
3. Problem – Liftgate will not lower
Cause
Correction
a. Defective or improperly
wired lower switch
Check voltage on the black wire of the control cord near the switch. If no voltage is
present, the black wire from the motor start solenoid is loose or broken and needs
repaired. If voltage is present, then check for voltage at the green wire on the switch
with the switch in the “DOWN” position. If no voltage is present, replace the switch.
b. Defective lowering
solenoid coil or valve
With the “DOWN” switch engaged, check for voltage on the green wire on the lower
solenoid valve coil terminal. If no voltage is present, the green wire from the
“DOWN” switch is loose or broken and needs replaced. Check for proper ground at
the purple wire on the lowering solenoid coil. Repair or replace ground as required. If
there is voltage (minimum of 9.5 volts) and proper ground at the lowering coil, and
the valve is not opening to allow the gate to lower, either the lower coil is bad or the
entire lower coil/valve assembly is bad. To check to see if the coil is defective,
remove the green and purple wires from the spade terminals on the lower coil and
check the resistance between these spade terminals (3.6 - 4.4 Ohm is acceptable).
Note: Low resistance can cause the 20-amp fuse to blow (see Problem 1, part b)
and high resistance will lower the coils magnetic force and may not shift the valve. If
proper resistance does not exist, replace the defective coil, otherwise replace the
defective lower coil/valve assembly.
c. Clogged or defective
hydraulic lines, fittings or
flow controls
Remove any obstruction in the hoses, fittings, and flow controls or replace any hose,
fitting or flow control which does not allow fluid to flow through freely.
4. Problem – Oil or foamy oil/air mixture flowing from reservoir breather
Cause
Correction
a. Air is present in the
system
This can occur if air enters the system if the fluid level is low, see problem 2, part a,
or if the suction tube is disconnected, see problem 2, part f. Also, air may enter
through fittings which are not tightened properly, so check for any leaks around
fittings or hoses. Once the source of the air is determined, the cylinders must be
bled of all air. Most air can be removed from the system by lowering the gate to the
ground to relieve all pressure from the cylinders, unpinning the cylinders, and cycling
them back and forth several times from fully extended to fully retracted and allowing
the pump to bypass through the relief valves for a few seconds in each direction.
e. Reservoir was overfilled
or filled with liftgate in
wrong position.
See the
MONTHLY INSPECTION AND MAINTENANCE
in the “Maintenance
Guide” section of this manual to find out what position the liftgate should be in when
checking the reservoir level and how full the reservoir should be in that position.
5. Problem – Platform difficult to unfold to horizontal position OR platform hard to fold up from horizontal
position
Cause
Correction
a. Torsion bar broke
TT15 liftgates with platform load depths of 38 inches or greater are equipped with a
torsion bar to assist unfolding and folding the platform. If the platform suddenly
becomes heavier to fold and unfold, the torsion bar is likely broken. Replace the
torsion bar if broken.
b. Platform pivot pins are
seizing up in platform
pivots
Check that the platform pivot pins turn freely in the platform pivots. Any tightness in
these pivots will result in additional force required when folding or unfolding the
platform. If the platform gradually became harder to fold and unfold, it is likely due
to stiffness in the pivots. Replace worn bushings or corroded pins as necessary.
If you have any questions or problems that are not covered in this guide please call Thieman’s Engineering
Department at 1 800-524-5210.
27. Rev. 11-26-2019
Содержание TopLifter TT-15
Страница 15: ...15...
Страница 23: ...23...
Страница 25: ...25...
Страница 27: ...27...
Страница 28: ...28 ELECTRICAL PICTORIAL...
Страница 32: ...Rev 5 22 1 5M MP110223...