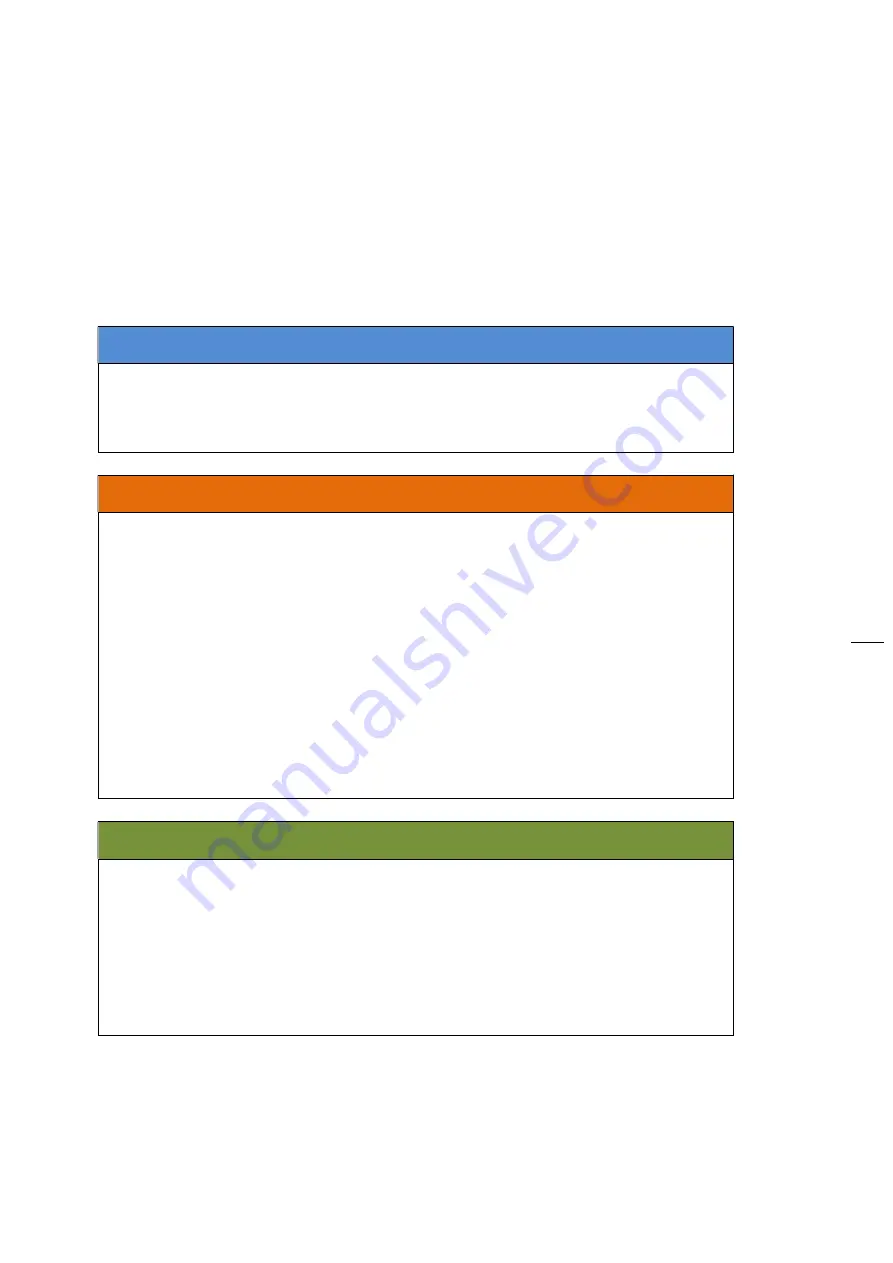
Cortina S manuel Ver.01
12
For correct sizing of closed expansion tank, refer to calculations supplied by the manufacturer.
Nevertheless, the volume of closed expansion tank should not be less than:
12 liters for Cortina 12
12 liters for Cortina 18
18 liters for Cortina 24
24 liters for Cortina 32
30 liters for Cortina 40
NOTICE
Safety of heating circuitg
•
Install a ½” safety valve with a maximum relief pressure of 3 bars.
•
Install a manometer to follow and check water pressure in the system. When
water is cold, system pressure should be set at 1 – 1,5 bars.
WARNING
Risk of corrosion on boiler and heating circuit
•
Your boiler is quite a strong design against corrosion. However, all metal
surfaces in whole heating circuit should be protected against corrosion like
piping and radiators. The oxygen in heating water will cause rust and then
material loss on iron-based metal surfaces by means of oxidation.
•
During the first water make-up, oxygen must be fully discharged from the
system. Generally, oxidation will not be a problem, if all measures are taken
into account during first water make-up. Oxidation will take place because of
fresh water addition to the system during operation of the boiler. Leak
points in a system will cause oxygen to be absorbed inside the heating water.
For this reason, minimum water pressure in a pressurized heating circuit
must be above atmospheric pressure. Besides, pressure levelshould always
be checked periodically.
CAUTION
For new installations
•
System should be sized and designed accordingly, in order to minimize fresh
water addition. Make sure that no part of the system is made of material
that is permeable to gases. The original system filling water and any topping-
up water must always be filtered (using synthetic or metal mesh filters with a
filtration rating of no less than 50 microns) to prevent sludge from forming
and triggering deposit induced corrosion. Minimum water pressure in a
pressurized heating circuit must always be kept above atmospheric pressure
Содержание Cortina 12 S
Страница 1: ...CORTİNA S INSTALLATION USER MANUAL ...
Страница 7: ...Cortina S manuel Ver 01 7 4 TECHNICAL DATA ...