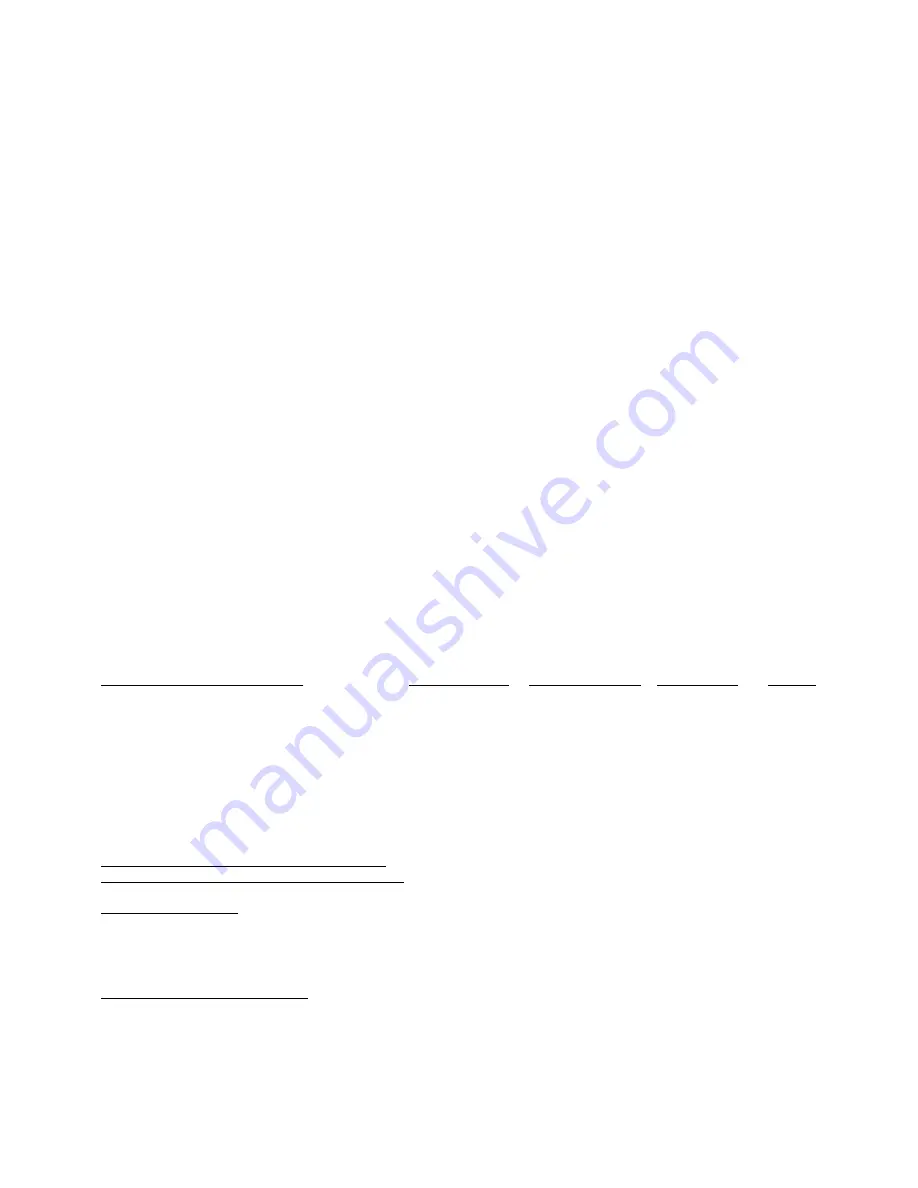
7
GENERAL INFORMATION
1.08 Statement of Warranty
LIMITED WARRANTY:
Thermal Dynamics
®
Corporation (hereinafter “Thermal”) warrants that its products will be free of
defects in workmanship or material. Should any failure to conform to this warranty appear within the time period applicable to
the Thermal products as stated below, Thermal shall, upon notification thereof and substantiation that the product has been
stored, installed, operated, and maintained in accordance with Thermal’s specifications, instructions, recommendations and
recognized standard industry practice, and not subject to misuse, repair, neglect, alteration, or accident, correct such defects by
suitable repair or replacement, at Thermal’s sole option, of any components or parts of the product determined by Thermal to be
defective.
THIS WARRANTY IS EXCLUSIVE AND IS IN LIEU OF ANY WARRANTY OF MERCHANTABILITY OR FITNESS FOR A
PARTICULAR PURPOSE.
LIMITATION OF LIABILITY:
Thermal shall not under any circumstances be liable for special or consequential damages, such
as, but not limited to, damage or loss of purchased or replacement goods, or claims of customers of distributor (hereinafter
“Purchaser”) for service interruption. The remedies of the Purchaser set forth herein are exclusive and the liability of Thermal
with respect to any contract, or anything done in connection therewith such as the performance or breach thereof, or from the
manufacture, sale, delivery, resale, or use of any goods covered by or furnished by Thermal whether arising out of contract,
negligence, strict tort, or under any warranty, or otherwise, shall not, except as expressly provided herein, exceed the price of the
goods upon which such liability is based.
THIS WARRANTY BECOMES INVALID IF REPLACEMENT PARTS OR ACCESSORIES ARE USED WHICH MAY IMPAIR
THE SAFETY OR PERFORMANCE OF ANY THERMAL PRODUCT.
THIS WARRANTY IS INVALID IF THE PRODUCT IS SOLD BY NON-AUTHORIZED PERSONS.
The limited warranty periods for Thermal products shall be as follows (with the exception of CutMaster 80XL , Cougar and
DRAG-GUN): A maximum of three (3) years from date of sale to an authorized distributor and a maximum of two (2) years from
date of sale by such distributor to the Purchaser, and with the further limitations on such two (2) year period (see chart below).
The limited warranty period for CutMaster 80XL shall be as follows: A maximum of four (4) years from date of sale to an
authorized distributor and a maximum of three (3) years from date of sale by such distributor to the Purchaser, and with
the further limitations on such three (3) year period (see chart below).
The limited warranty period for Cougar and DRAG-GUN shall be as follows: A maximum of two (2) years from date of
sale to an authorized distributor and a maximum of one (1) year from date of sale by such distributor to the Purchaser, and
with the further limitations on such two (2) year period (see chart below).
PARTS
PARTS
PARTS
PAK UNITS, POWER SUPPLIES
CutMaster 80XL
Cougar/Drag-Gun
All OTHERS
LABOR
Main Power Magnetics
3 Years
1 Year
2 Years
1 Year
Original Main Power Rectifier
3 Years
1 Year
2 Years
1 Year
Control PC Board
3 Years
1 Year
2 Years
1 Year
All Other Circuits And Components Including,
1 Year
1 Year
1 Year
1 Year
But Not Limited To, Starting Circuit,
Contactors, Relays, Solenoids, Pumps,
Power Switching Semi-Conductors
CONSOLES, CONTROL EQUIPMENT, HEAT
1 Year
1 Year
1 Year
EXCHANGES, AND ACCESSORY EQUIPMENT
TORCH AND LEADS
Maximizer 300 Torch
N/A
1 Year
1 Year
All Other Torches
180 Days
180 Days
180 Days
180 Days
REPAIR/REPLACEMENT PARTS
90 Days
90 Days
90 Days
None
Warranty repairs or replacement claims under this limited warranty must be submitted by an authorized Thermal Dynamics®
repair facility within thirty (30) days of the repair. No transportation costs of any kind will be paid under this warranty.
Transportation charges to send products to an authorized warranty repair facility shall be the responsibility of the customer. All
returned goods shall be at the customer’s risk and expense. This warranty supersedes all previous Thermal warranties.
Effective October 9, 1998
Содержание Pak Master 100XL
Страница 2: ......
Страница 6: ......
Страница 14: ...GENERAL INFORMATION 8...
Страница 30: ...OPERATION 24 Manual 0 2581...
Страница 36: ...SERVICE 30 Manual 0 2581...
Страница 40: ...PARTS LISTS 34 Manual 0 2581...
Страница 43: ...Manual 0 2581 37 APPENDIX...
Страница 44: ...APPENDIX 38 Manual 0 2581 APPENDIX III SYSTEM SCHEMATIC A 01360...
Страница 45: ...Manual 0 2581 39 APPENDIX A 01360 B EC 8055 HAS 11 23 98...
Страница 46: ......