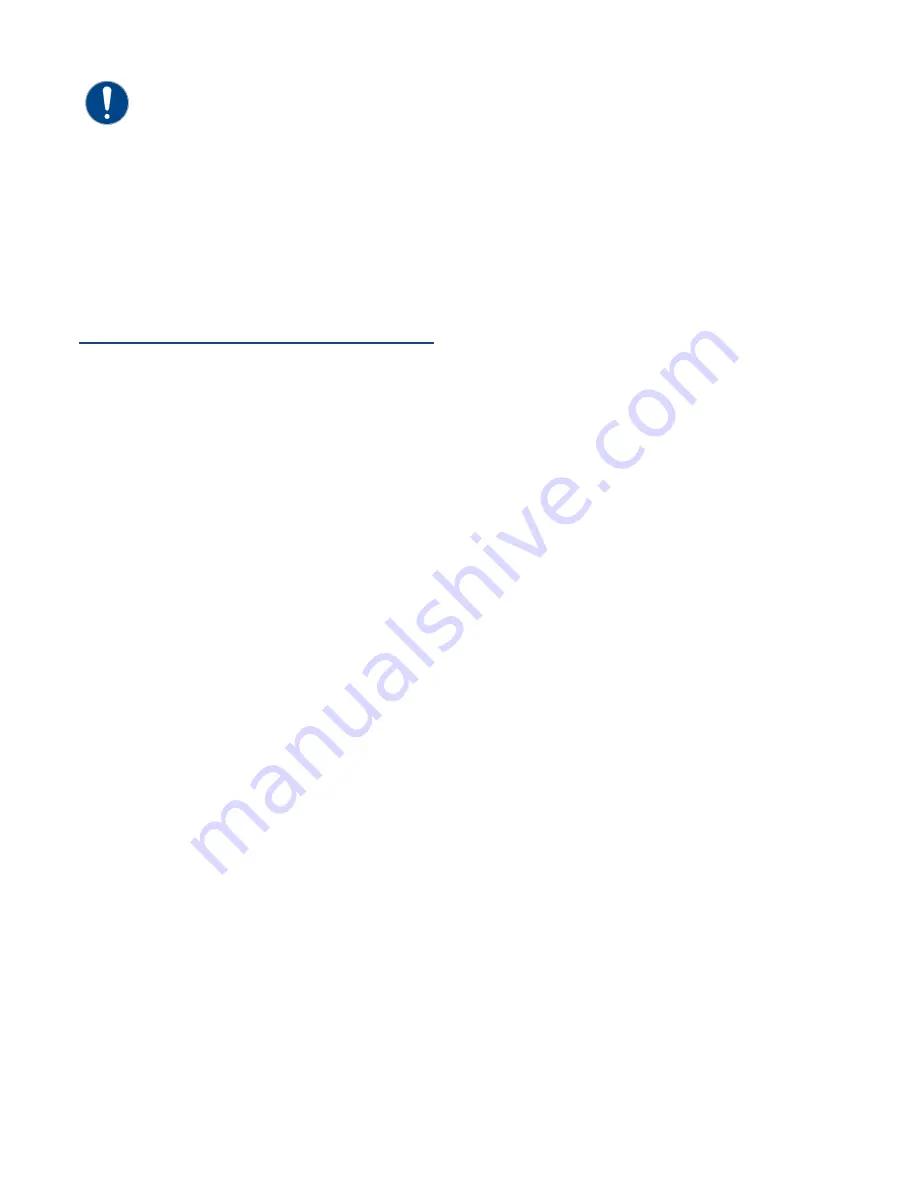
63
CAUTION: A clear sight glass alone does not
mean that the system is properly charged. Also,
check system superheat, sub-cooling, and unit
operating pressures. If both suction and
discharge pressures are low but sub-cooling is
normal, a problem other than refrigerant
shortage exists. Do not add refrigerant, as this
may result in overcharging the circuit.
Once proper flow and temperature are achieved,
press the Stop button. The unit is now ready to be
placed into service.
Preventive Maintenance
Once your portable chiller has been placed into
service, the following maintenance procedures
should be adhered to as closely as possible. The
importance of a properly established preventive
maintenance program cannot be overemphasized.
Taking the time to follow these simple procedures
will result in substantially reduced downtime,
reduced repair costs, and an extended useful lifetime
for the chiller. Any monetary costs of implementing
these procedures will almost always more than pay
for it.
To make this as simple as possible, a checklist should
be prepared which lists the recommended service
operations and the times at which they are to be
performed. At the end of this section we have
included a checklist that can be used for this
purpose. Notice that there are locations for voltage
readings, amperages, etc. so that they can be
monitored over time. With this information,
maintenance personnel may be able to correct a
potential problem before it causes any downtime.
For best results, these readings should be taken with
a full heat load from process, preferably with similar
operating conditions each time. The following is a
list of suggested periodic maintenance.
Once a Week
1.
(Air-Cooled Units Only) Check the surface of the
air-cooled condenser coil for dirt and debris. To
clean, rinse thoroughly with water. Mild
detergent can be used to remove smoke and or
grease stains.
2.
Check to make sure that the To Process
temperature is maintained reasonably close to
the Set Point temperature. If the temperature
stays more than 5°F away from the set point,
there may be a problem with the chiller. If this is
the case, refer to the Troubleshooting Chart or
contact the Customer Service Department.
3.
Check the pump discharge pressure on the
gauge on the back panel of the chiller.
Investigate further if the pressure starts to stray
away from the normal operating pressure.
4.
Check the coolant level in the reservoir.
Replenish if necessary making sure to take
proper precautions to maintain the appropriate
glycol concentration.
5.
Check coolant circulation pump for leaks in the
seal area. Replace pump seal if necessary.
6.
Check refrigerant sight glass for air bubbles or
moisture indication. If the sight glass indicates
that there is a refrigeration problem, have the
unit serviced as soon as possible.
Once a Month
7.
With the main disconnect shut off and locked
out, check the condition of electrical connections
at all contactors, starters and controls. Check for
loose or frayed wires.
8.
Check the incoming voltage to make sure it is
within 10% of the design voltage for the chiller.
9.
Check the amp draws to each leg of the
compressor (fans or blowers on air-cooled units)
and pump to confirm that they are drawing the
proper current.
Every Three Months
10.
Units are equipped with a Y-strainer between
the return connection and the evaporator inlet.
The strainer basket should be removed and
cleaned if necessary. This may be required more
often if contaminants can easily get into the
process water.
11.
Have a qualified refrigeration technician inspect
the operation of the entire unit to ensure that
everything is operating properly. Have
condenser cleaned out if necessary.
Содержание NQ Series
Страница 1: ...Installation Operation Manual NQ Series Portable and Remote Condenser Chillers...
Страница 2: ...Page Intentionally Blank...
Страница 75: ...Notes...