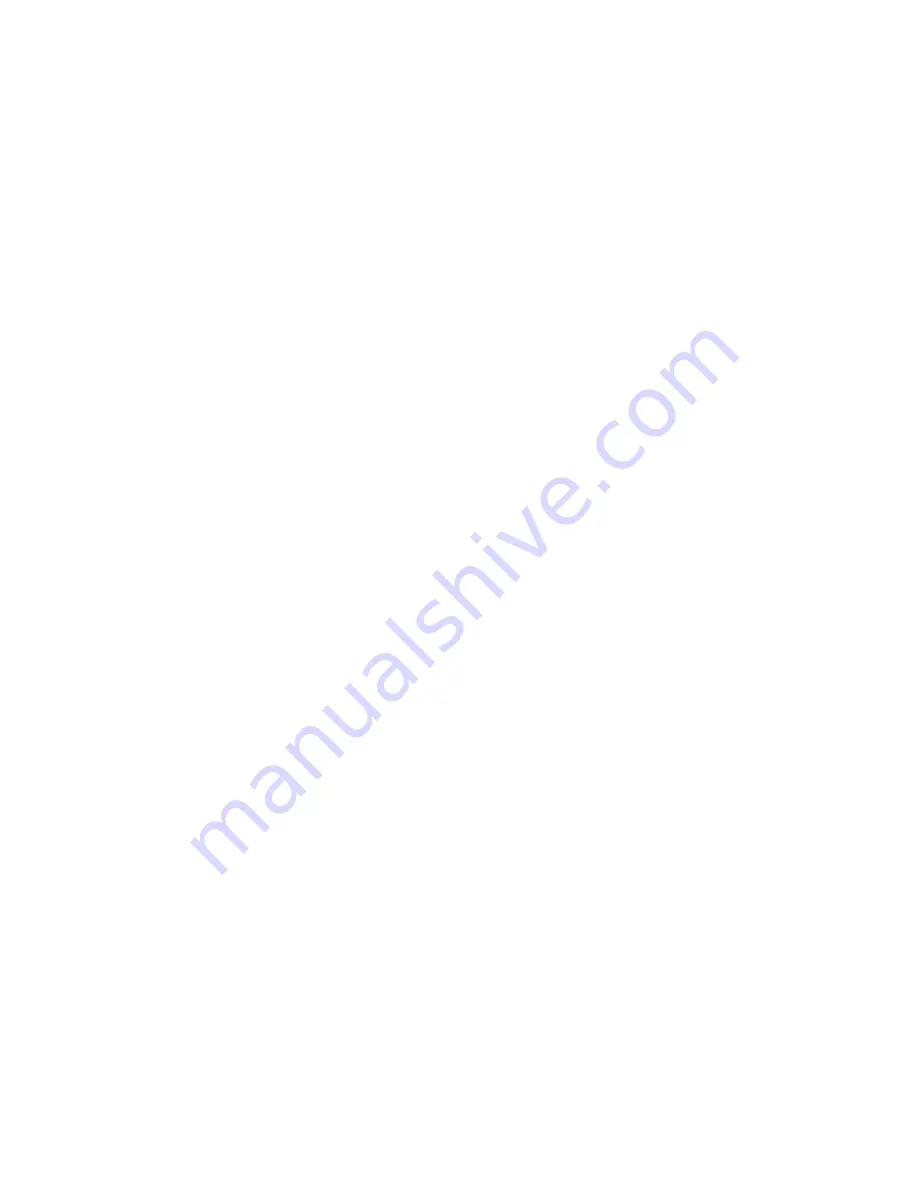
28
9.
Check the amp draws to each leg of the
compressor(s) to confirm that it is drawing the
proper current.
10.
Check the system superheat and sub-cooling.
The normal superheat is approximately 10°F and
should not be more than 15°F. The normal sub-
cooling range is from 10°F to 20°F.
Once Every 6 Months
Repeat items 1 through 10 and continue with the
following.
11.
Check for visible mechanical damage to the
compressor.
12.
Check for excessive vibration from other rotating
equipment.
13.
Check for signs of hot spot/discoloration on
power cables.
14.
Check all communication cables are secure and
tight.
15.
Check all electrical modules are secure.
16.
Check system refrigerant charge and verify the
system is still full charged.
17.
Check the operation of the compressor
crankcase heater. Energize the heater while the
compressor is off. Taking an amp reading of the
heater leads is the best way to determine the
correct operation. Another way is to feel if there
is localized heat around the crankcase heater
when the heater is on.
Once a Year
Repeat items 1 through 17 land continue with the
following.
18.
Check the condition of the chilled water for
algae and particulate fouling. Back flush the
evaporator with water or another suitable
cleaning agent. The frequency at which this task
is required depends on specific site conditions.
19.
(MXW Models) Check the condition of the
condenser water for algae, scale, and particulate
fouling. Rod out the tubes and back flush the
condensers. If scaling exists on the condenser
tubes, chemical cleaning of the tubes may also
be necessary. If a chemical cleaning agent is
used, it should be suitable with the internal
components composed of copper, steel, and
cast iron. The frequency at which this task is
required depends on specific site conditions.
20.
(MXR Models) Check the condition of the air
coils of the remote condensers for dirt and
debris. If the coils are dirty or clogged, use a
compressed air source to blow the contaminants
out of the air coil. The frequency at which this
task is required depends on specific site
conditions.
21.
Have a qualified laboratory perform a
compressor oil analysis to determine system
moisture content and acid level.