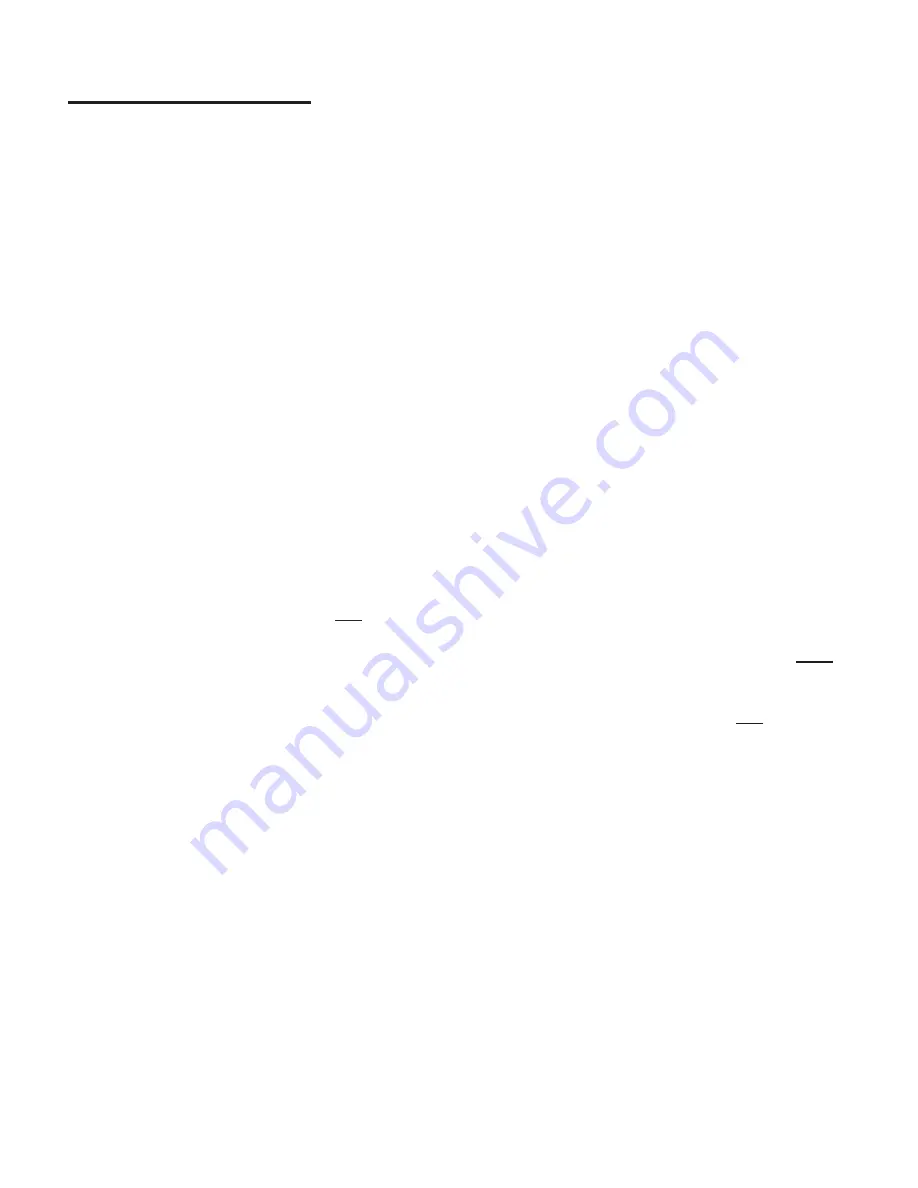
9
TH-750-IMI-REV-
5
Section 4 – Maintenance
1. Gasket creep is inherent to most gasketed joints, and retorquing is required. The greater the
operating temperature and pressure, the greater the problem can become. It is imperative
that the head bolts be torqued after installation, after initial setup, and inspected several
times a year to be sure that the bolts are torqued correctly and there are no leaks. See
section 1 paragraph 19 for correct torque procedure.
2. Located at the lower rear of the unit, the TH-750 has a manual, shell blow down valve that
should be piped to a suitable drain. On a monthly to quarterly frequency, this valve should be
quickly opened for 2 seconds to remove scale buildup and any normal sediment that may
collect in the shell.
3. The intra-tank circulation pump is critical for the accurate operation of the TH-750. This
pump
circulates the water in the shell across the temperature sensor and back into the shell
through
the cold water supply inlet. This action allows the system to not only detect changes
in flow
demand, but also temperature changes as well. The recirculation pump is fitted with
permanently lubricated bearings and therefore does not require any additional lubrication. If
however the TH-750 suddenly becomes unable to maintain accurate control, the pump
should
be checked for operation.
4. On a yearly basis, the operation of the recirculation pump should be verified, and isolation
valves have been fitted on each side of the pump for this service. If the pump is not running,
make sure the pump ON-OFF switch (black in color and located on the right side of the
EC800 control panel) is in the ON position.
5. If the recirculation pump requires replacement, turn the pump ON-OFF switch to the OFF
position, isolate pump and remove.
6. Install new pump, open isolation valves and turn pump ON-Off switch to the ON position.
This can be done while the TH-750 heater remains in service so that hot water flow to end
users is not interrupted.
7. All TH-750 units must be fitted with a steam drip trap station (trap and strainer) at the steam
inlet before the control valve. The satisfactory operation of this trap is critical. On at least a
quarterly basis, this trap should be checked for condition and operation and the strainer
should be blown down to clean.
8. On a yearly basis it is good practice to operate each valve on the TH-750 unit to ensure all
valves operate and shut off as required.
9. Each TH-750 heater is fitted with a pressure gauge and steam siphon. At least once a year
the operation of this gauge should be verified by closing off the steam inlet valve and making
sure the gauge registers zero. If it does not, the accuracy may be off and it should be
replaced.
10. Each TH-750 heater is fitted with a pressure and temperature relief valve. Scale from hard
water can build up on the element and cause the valve to malfunction. We recommend that
this valve be replaced every two years to make sure operation is verified. A record of the