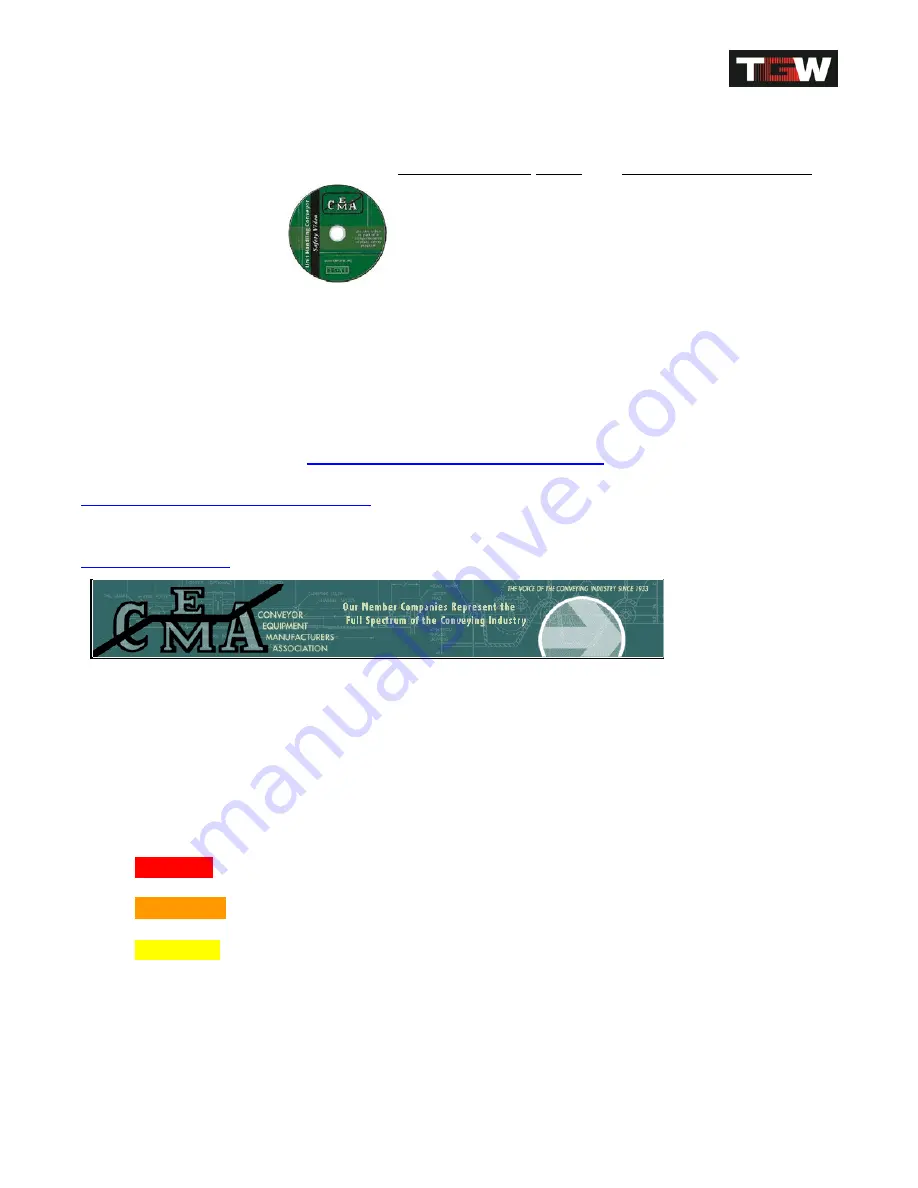
Natrix IOM
Conveyor Equipment Manufacturers Association (CEMA)
The Conveyor Equipment Manufacturers Association (CEMA) provides safety information
related to conveyor systems. There are Conveyor Safety Video and Conveyor Safety Poster
produced by CEMA.
TGW recommends these video for training and education purposes for a safe working
environment around conveyor equipment. The video introduces awareness of operation
personnel maintenance technicians, and management to safety hazards commonly associated
with the automated material handling conveyor equipment.
Safety poster reviews the important safety labels and is intended to be posted in public places
as a day-to-day reinforcement of good safety practices. These posters can be downloaded
from the CEMA Web Site at
http://cemanet.org/safety/posters.htm
the CEMA Safety Program visit the CEMA Web Site’s Safety Page at
http://cemanet.org/safety/index.html.
Both the safety poster and the video can be purchased from CEMA. Visit their web site –
for additional information or contact them at:
Conveyor Equipment Manufacturers Association
6724 Lone Oak Blvd. Naples FL 34109
Phone (941) 514-3470
CEMA Safety Label Meanings
The word or words that designate a degree or level of hazard seriousness. The signal words for product
safety signal are: DANGER, WARNING, and CAUTION.
•
DANGER
-Indicates an imminently hazardous situation which, if not avoided, will result in
death or serious injury. This signal word is to be limited to the most extreme situations.
•
WARNING
– Indicates potentially hazardous situation which, if not avoided, could result in
minor or moderate injury. It may also be used to alert against unsafe practices.
•
CAUTION
– Indicates a potentially hazardous situation which, if not avoided, may result in
minor or moderate injury. It may also be used to alert against unsafe practices.
Revision Date: 12/10/2014
Page
12
of
111
Содержание Natrix
Страница 1: ...INSTALLATION OPERATION MAINTENANCE MANUAL Natrix Shoe Sorter Revision Date February 5 2015 ...
Страница 18: ...Natrix IOM Revision Date 12 10 2014 Page 18 of 111 ...
Страница 19: ...Natrix IOM Symbols and Units Revision Date 12 10 2014 Page 19 of 111 ...
Страница 29: ...Natrix IOM Pictures of packing units or structures continued Revision Date 12 10 2014 Page 29 of 111 ...
Страница 39: ...Natrix IOM Revision Date 12 10 2014 Page 39 of 111 ...
Страница 46: ...Natrix IOM Sorter Link Chain Revision Date 12 10 2014 Page 46 of 111 ...
Страница 48: ...Natrix IOM Blank page for placement Revision Date 12 10 2014 Page 48 of 111 ...
Страница 59: ...Natrix IOM Monitoring of Chain Tension Picture Revision Date 12 10 2014 Page 59 of 111 ...
Страница 60: ...Natrix IOM Replace Sliding Shoe Revision Date 12 10 2014 Page 60 of 111 ...
Страница 62: ...Natrix IOM Blank page for placement Revision Date 12 10 2014 Page 62 of 111 ...
Страница 66: ...Natrix IOM Blank page for placement Revision Date 12 10 2014 Page 66 of 111 ...
Страница 68: ...Natrix IOM Replace Divert Switch Assembly Revision Date 12 10 2014 Page 68 of 111 ...
Страница 72: ...Natrix IOM Adjust Switch Blade Revision Date 12 10 2014 Page 72 of 111 ...
Страница 76: ...Natrix IOM Replace Electrical Components Revision Date 12 10 2014 Page 76 of 111 ...
Страница 85: ...Natrix IOM Charge End Chain Tensioning Unit Revision Date 12 10 2014 Page 85 of 111 ...
Страница 90: ...Natrix IOM Electrical Proximity Switch Revision Date 12 10 2014 Page 90 of 111 ...
Страница 92: ...Natrix IOM Sorter Link Chain Revision Date 12 10 2014 Page 92 of 111 ...
Страница 97: ...Natrix IOM Reading Value Revision Date 12 10 2014 Page 97 of 111 ...
Страница 100: ...Natrix IOM Replace Support Roller Revision Date 12 10 2014 Page 100 of 111 ...
Страница 102: ...Natrix IOM Replace Belt Drive Motor Revision Date 12 10 2014 Page 102 of 111 ...