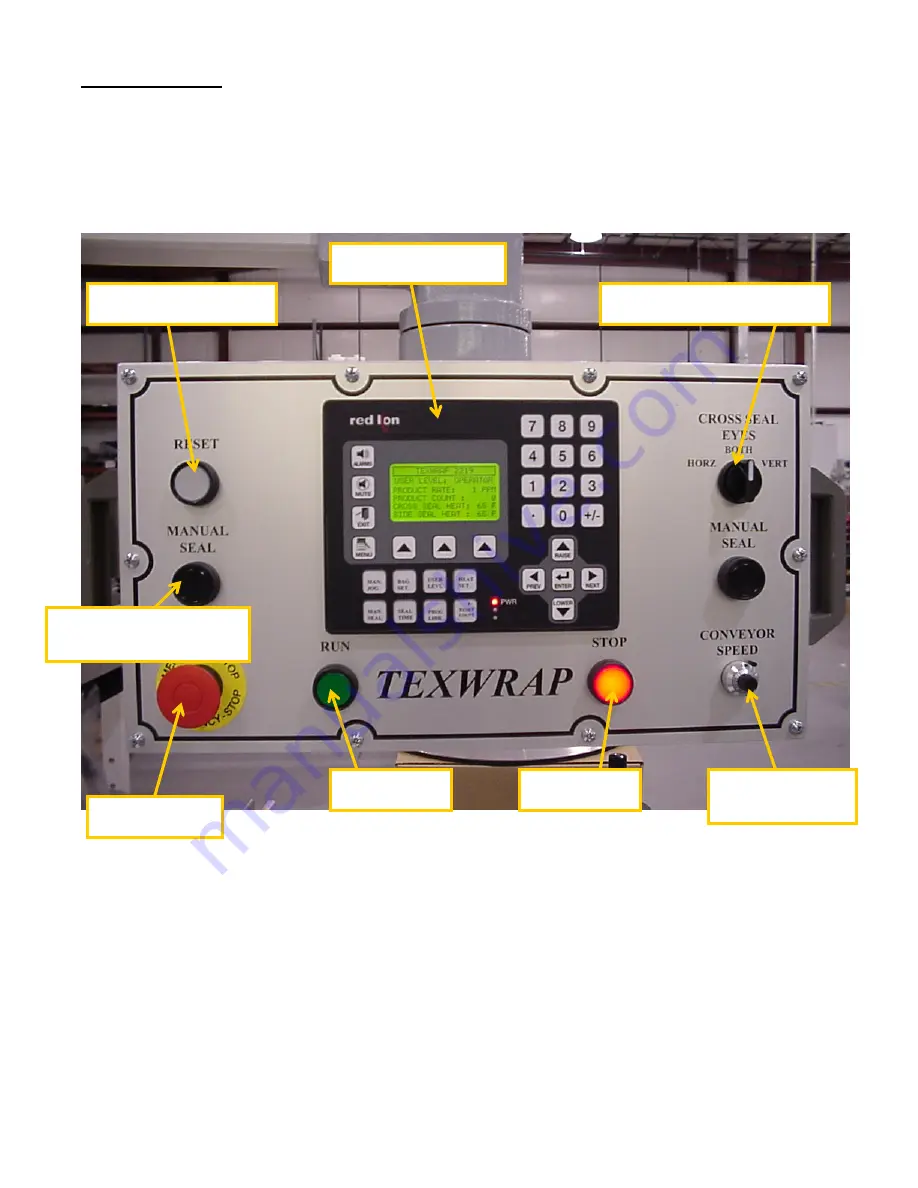
Machine Interface
This Texwrap model features a swivel user interface with touch-pad control. All controls and electrical
settings can be modified by the user through this interface.
**
With the seal area door open, a manual seal can be made by pressing BOTH Manual Seal buttons on
the control panel. When the door is closed, only the touch pad Manual Seal button will be active.
NOTICE:
To reset the machine to factory defaults, press and hold the Stop and Reset button for 5
seconds. Display will acknowledge when procedure is done.
Door Open Manual Seal
Over-ride**
Touch-pad Interface
Conveyor Speed
Control
Run Button
Stop Button
E-stop Button
Machine Reset Button
Selectable seal eyes switch
10
Содержание 2219 Series
Страница 2: ...This page intentionally left BLANK 2 ...
Страница 8: ...This page intentionally left BLANK 8 ...
Страница 9: ...TEXWRAP 2219 OPERATIONS MANUAL 9 ...
Страница 16: ...This page intentionally left BLANK 16 ...
Страница 29: ...Service Press the corresponding number to access the desired screen 29 ...