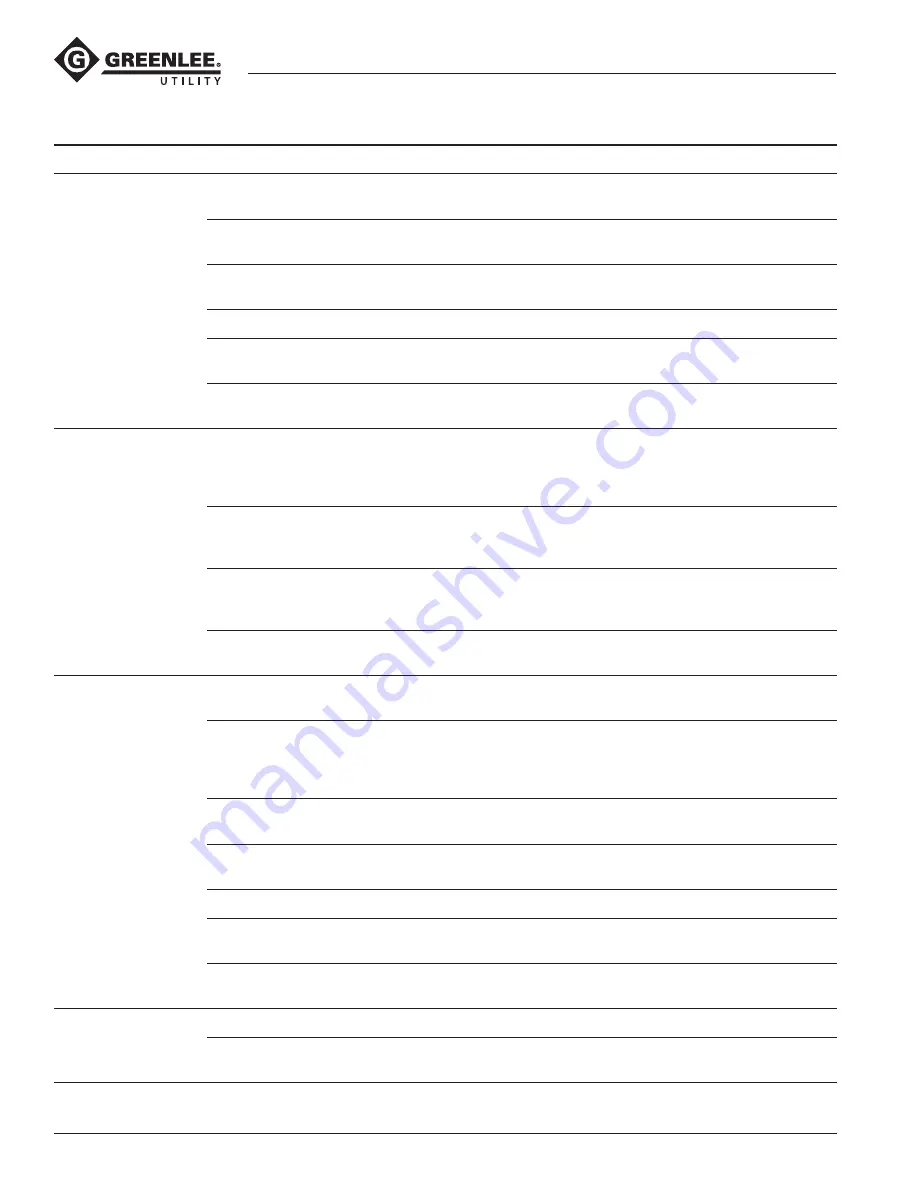
LHFS-210003 Pruner
Greenlee / A Textron Company
4455 Boeing Dr. • Rockford, IL 61109-2988 USA • 815-397-7070
8
Troubleshooting
(cont’d)
Problem
Probable Cause
Probable Remedy
Tool inoperative.
Tool connected to improper power
source hydraulic system.
Verify that the power source meets the specifications.
Refer to the Specifications and Parts manual.
No hydraulic fluid in system or fluid
level low.
Check fluid level. Fill to FULL mark. Check system
for leaks.
Incorrect fluid viscosity.
Use fluid viscosity recommended. Refer to the
Specifications and Parts manual.
Tool components loose.
Tighten component hardware.
Dirt, contaminants, etc., in tool
components.
Disassemble tool and clean components.
Tool components worn or
damaged.
Disassemble tool. Replace worn or damaged
components.
Tool operates
erratically.
Hydraulic fluid cold.
Viscosity of oil may be too high at start of tool
operation. Allow oil to warm to operating temperature.
Actuating tool intermittently will reduce time required
to warm oil to an efficient operating temperature.
Air in hydraulic system.
Check pump suction line for damage or loose clamps.
Tighten clamps or replace components if necessary.
Fill reservoir.
Tool components sticking or
binding.
Check for dirt or gummy deposits. Clean components.
Check for worn or damaged components.
Replace components.
Dirt, contaminants, etc., in tool
components.
Disassemble tool and clean components.
Tool operates slowly. Power source components not
adjusted correctly.
Refer to power source operator’s manual for
recommended speed, flow, and pressure settings.
Hydraulic fluid cold.
Viscosity of oil may be too high at start of tool
operation. Allow oil to warm to operating temperature.
Actuating tool intermittently will reduce time required
to warm oil to an efficient operating temperature.
Hydraulic fluid level low.
Check fluid level. Fill to FULL mark. Check system
for leaks.
Hydraulic fluid viscosity too heavy.
Use fluid viscosity recommended. Refer to the
Specifications and Parts manual.
Tool components loose.
Tighten component hardware.
Dirt, contaminants, etc., in tool
components.
Disassemble tool and clean components.
Tool components worn or
damaged.
Disassemble tool. Replace worn or damaged
components.
Tool leaks hydraulic
fluid.
Tool components loose.
Tighten component hardware.
Tool components worn or
damaged.
Disassemble tool. Replace worn or damaged
components.