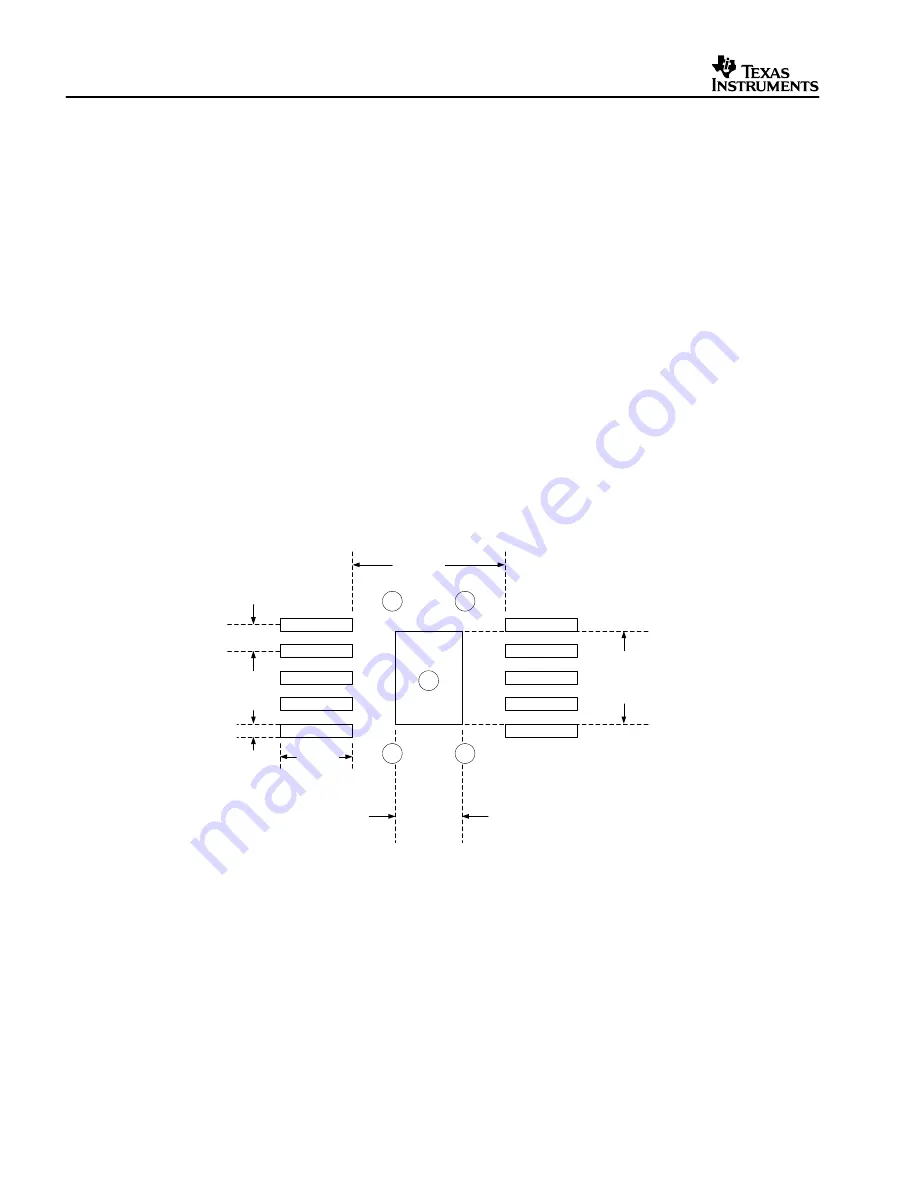
SLUU131A – September 2002 – Revised February 2003
10
TPS40001 Based Converter Delivers 10-A Output
5
PowerPAD Packaging
The TPS4000X family is available in the DGQ version of TI’s PowerPAD
t
thermally enhanced package. In the
PowerPAD
t
, a thermally conductive epoxy is utilized to attach the integrated circuit die to the leadframe die
pad, which is exposed on the bottom of the completed package. The leadframe die pad can be soldered to the
PCB using standard solder flow techniques when maximum heat dissipation is required. However, depending
on power dissipation requirements, the PowerPAD
t
may not need to soldered to the PCB.
The thermally conductive epoxy bonding the circuit die to the leadframe die pad causes a high resistance from
the leadframe die pad to the device ground pin 5. When the PowerPad
t
package is soldered to the PCB, the
leadframe die pad can be connected to ground (pin 5), but this is not required. The leadframe die pad should
not be connected to other potentials in the circuit.
The PowerPAD
t
package helps to keep the junction temperature rise relatively low even with the power
dissipation inherent in the onboard MOSFET drivers. This power loss is proportional to switching frequency,
drive voltage, and the gate charge needed to enhance the N-channel MOSFETs. Effective heat removal allows
the use of ultra small packaging while maintaining high component reliability.
To effectively remove heat from the PowerPAD
t
package, a thermal land should be provided directly
underneath the package. This thermal land usually has vias that help to spread heat to internal copper layers
and/or the opposite side of the PCB. The vias should not have thermal reliefs that are often used on ground
planes, because this reduces the copper area to transfer heat. Additionally, the vias should be small enough
so that the holes are effectively plugged when plated. This prevents the solder from wicking away from the
connection between the PCB surface and the bottom of the part. A typical footprint pattern is shown in Figure 2,
but does not include the additional copper plane which includes the vias above and below the device.
2.92mm
(0.115”)
0.5mm
(0.0197”)
0.28mm
(0.011”)
1.40mm
(0.055”)
Via Dia.
0.33mm
(0.013”)
Miminum
PowerPad ”X”
1.3mm
(0.050”)
Minimum
PowerPad ”Y”
1.7mm
(0.068”)
Figure 3. PowerPAD
t
PCB Layout Guidelines
The Texas Instrument document, PowerPAD
t
Thermally Enhanced Package Application Report (Texas
Instrument Literature Number SLMA002) should be consulted for more information on the PowerPAD
t
package. This report offers in-depth information on the package, assembly and rework techniques, and
illustrative examples of the thermal performance of the PowerPAD
t
package.