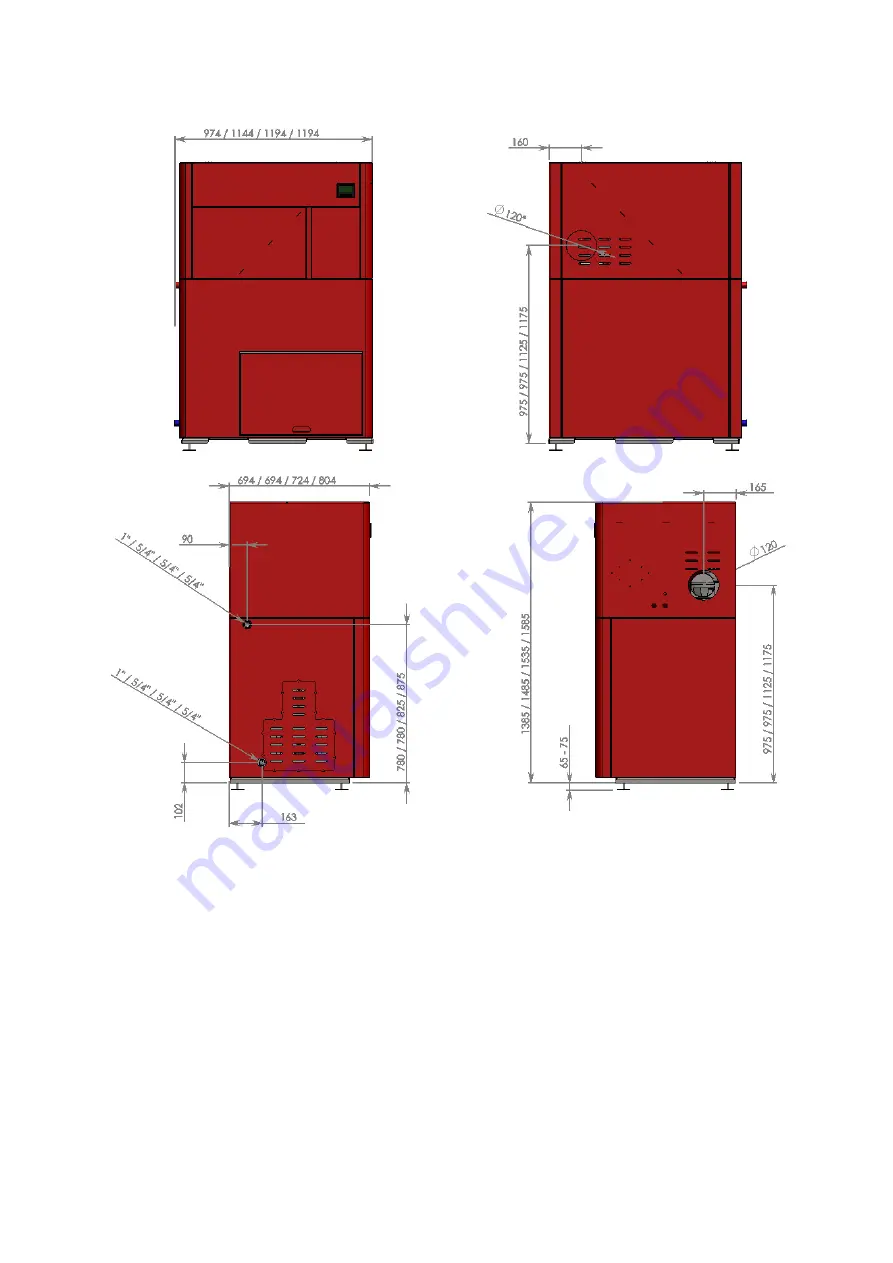
1
Boiler data
Boiler measures are given in the form X / Y / Z where first value is for the 20 KW model and second
value for 30 KW and third value for a 50 KW model where measures differ. Single measure is shown
elsewhere valid for all the models.
Boiler connections to the central heating system are on its left hand side. Flow line is painted red.
Return line is painted blue. Fill/Drain tap is located at the return line.
Flue gas exit is located on the right hand side of the boiler. It can be also on the back side of the boiler.
2