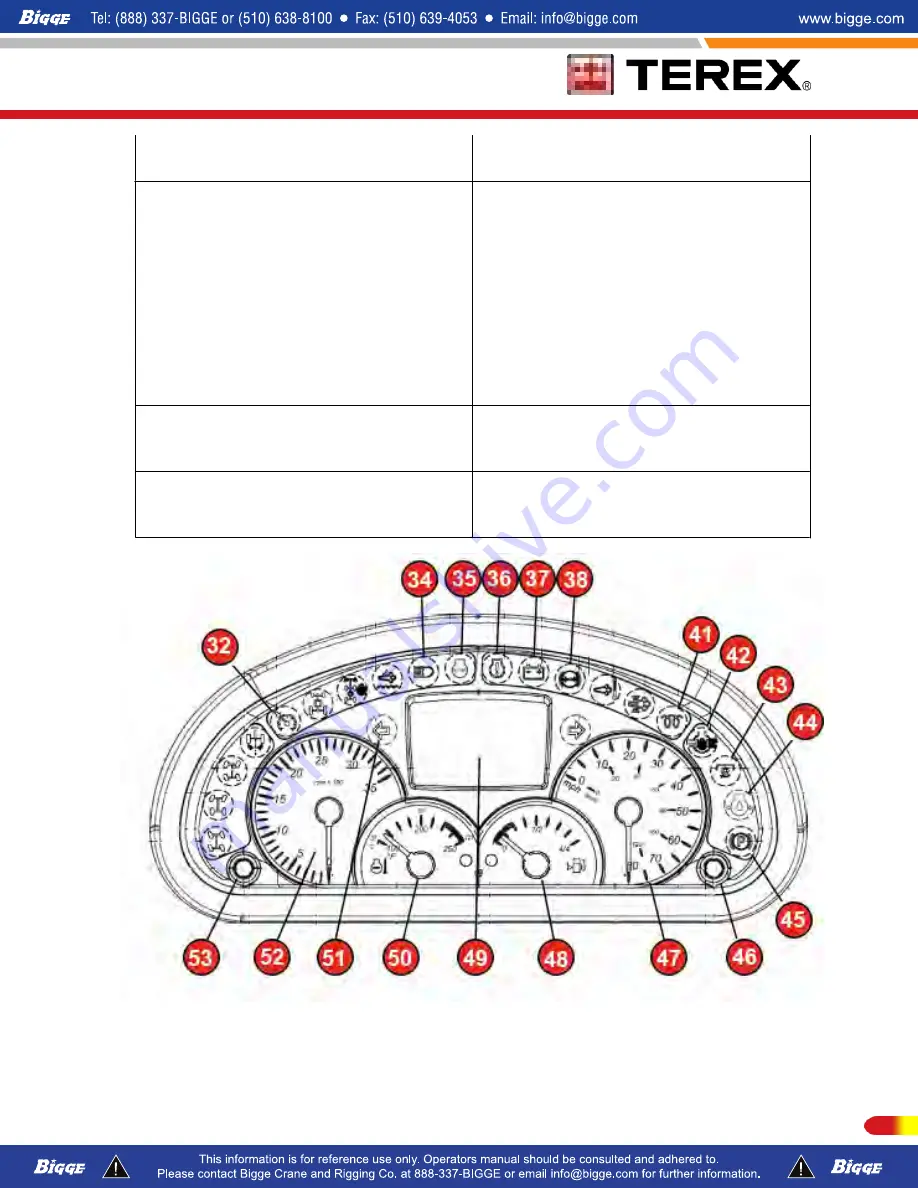
13. PTO AIR VALVE SWITCH-Push up to
engage pumps, push down to disengage.
29. ACCELERATOR PEDAL-Depress to
accelerate.
14. INTER AXLE LOCKOUT VALVE-Lock out
inter-axle differential. Should the machine
become stuck, a spinning whell will receive
all power transmitted by the drivetrain
causing tha wheel to spin faster and worsen
the condition. Use of the lockout divides the
available power between the two axles of
the rear tandem. With the lockout engaged,
the stuck wheel may continue to spin but the
other side of the tandem will begin "driving",
thus
30. BRAKE PEDAL-Depress to actuate.
15. AIR GUAGE (REAR) -indicates air
pressure in rear air tank. Maintain 110 to 115
psi normal system air pressure.
31. CIRCUIT BREAKERS-Electrical circuit
breakers are under this panel.
16. PARKING BRAKE CONTROL VALVE -
Controls parking brakes. Pull to apply, push
to release.
123
P/N 12261-683 REVISED: January 2015
Содержание T300-1
Страница 22: ...General Safety Safety Sign Locations 21 P N 12261 683 REVISED January 2015...
Страница 78: ...77 P N 12261 683 REVISED January 2015...
Страница 81: ......
Страница 86: ...Carrier Controls and Instruments EPA 2013 Engines 85 P N 12261 683 REVISED January 2015...
Страница 97: ...T300 1_T500 1_T780 Description Of Machine and Controls 96 P N 12261 683 REVISED January 2015...
Страница 98: ...97 P N 12261 683 REVISED January 2015...
Страница 99: ...T300 1_T500 1_T780 Description Of Machine and Controls 98 P N 12261 683 REVISED January 2015...
Страница 100: ...99 P N 12261 683 REVISED January 2015...
Страница 101: ...T300 1_T500 1_T780 Description Of Machine and Controls 100 P N 12261 683 REVISED January 2015...
Страница 102: ...101 P N 12261 683 REVISED January 2015...
Страница 103: ...T300 1_T500 1_T780 Description Of Machine and Controls 102 P N 12261 683 REVISED January 2015...
Страница 104: ...103 P N 12261 683 REVISED January 2015...
Страница 105: ...T300 1_T500 1_T780 Description Of Machine and Controls 104 P N 12261 683 REVISED January 2015...
Страница 106: ...105 P N 12261 683 REVISED January 2015...
Страница 107: ...T300 1_T500 1_T780 Description Of Machine and Controls 106 P N 12261 683 REVISED January 2015...
Страница 108: ...107 P N 12261 683 REVISED January 2015...
Страница 110: ...109 P N 12261 683 REVISED January 2015...
Страница 111: ...T300 1_T500 1_T780 Description Of Machine and Controls 110 P N 12261 683 REVISED January 2015...
Страница 112: ...111 P N 12261 683 REVISED January 2015...
Страница 113: ...T300 1_T500 1_T780 Description Of Machine and Controls 112 P N 12261 683 REVISED January 2015...
Страница 114: ...113 P N 12261 683 REVISED January 2015...
Страница 115: ...T300 1_T500 1_T780 Description Of Machine and Controls 114 P N 12261 683 REVISED January 2015...
Страница 116: ...115 P N 12261 683 REVISED January 2015...
Страница 117: ...T300 1_T500 1_T780 Description Of Machine and Controls 116 P N 12261 683 REVISED January 2015...
Страница 118: ...117 P N 12261 683 REVISED January 2015...
Страница 119: ...T300 1_T500 1_T780 Description Of Machine and Controls 118 P N 12261 683 REVISED January 2015...
Страница 120: ...119 P N 12261 683 REVISED January 2015...
Страница 121: ...T300 1_T500 1_T780 Description Of Machine and Controls 120 P N 12261 683 REVISED January 2015...
Страница 122: ...Carrier Controls and Instruments EXPORT 121 P N 12261 683 REVISED January 2015...
Страница 130: ...129 P N 12261 683 REVISED January 2015...
Страница 139: ......
Страница 146: ...145 P N 12261 683 REVISED January 2015...
Страница 157: ......
Страница 166: ...Aftertreatment Regeneration Lamp Behaviors 165 P N 12261 683 REVISED January 2015...
Страница 167: ...T300 1_T500 1_T780 Operating Instructions 166 P N 12261 683 REVISED January 2015...
Страница 168: ...167 P N 12261 683 REVISED January 2015...
Страница 169: ...Regeneration Modes T300 1_T500 1_T780 Operating Instructions 168 P N 12261 683 REVISED January 2015...
Страница 172: ...Operating the Unit Operating the Engine 171 P N 12261 683 REVISED January 2015...
Страница 173: ...T300 1_T500 1_T780 Operating Instructions 172 P N 12261 683 REVISED January 2015...
Страница 174: ...173 P N 12261 683 REVISED January 2015...
Страница 176: ...175 P N 12261 683 REVISED January 2015...
Страница 177: ...T300 1_T500 1_T780 Operating Instructions 176 P N 12261 683 REVISED January 2015...
Страница 178: ...177 P N 12261 683 REVISED January 2015...
Страница 181: ...Engine Cold Weather Operation T300 1_T500 1_T780 Operating Instructions 180 P N 12261 683 REVISED January 2015...
Страница 182: ...181 P N 12261 683 REVISED January 2015...
Страница 183: ...T300 1_T500 1_T780 Operating Instructions 182 P N 12261 683 REVISED January 2015...
Страница 207: ...4 Air Yoke 5 Switch T300 1_T500 1_T780 Operating Instructions 206 P N 12261 683 REVISED January 2015...
Страница 235: ......
Страница 242: ...Crane Maintenence Specification Acronyms and Abbreviations 241 P N 12261 683 REVISED January 2015...
Страница 243: ...T300 1_T500 1_T780 Maintenance 242 P N 12261 683 REVISED January 2015...
Страница 244: ...General Safety Instructions 243 P N 12261 683 REVISED January 2015...
Страница 245: ...T300 1_T500 1_T780 Maintenance 244 P N 12261 683 REVISED January 2015...
Страница 246: ...Flow Diagram Exhaust System 245 P N 12261 683 REVISED January 2015...
Страница 247: ...T300 1_T500 1_T780 Maintenance 246 P N 12261 683 REVISED January 2015...
Страница 249: ...T300 1_T500 1_T780 Maintenance 248 P N 12261 683 REVISED January 2015...
Страница 250: ...Engine Cooling System Maintenence Schedule 249 P N 12261 683 REVISED January 2015...
Страница 251: ...T300 1_T500 1_T780 Maintenance 250 P N 12261 683 REVISED January 2015...
Страница 252: ...251 P N 12261 683 REVISED January 2015...
Страница 253: ...T300 1_T500 1_T780 Maintenance 252 P N 12261 683 REVISED January 2015...
Страница 254: ...Aftertreatment Diesel Exhaust Fluid Dosing Unit Filter 253 P N 12261 683 REVISED January 2015...
Страница 255: ...T300 1_T500 1_T780 Maintenance 254 P N 12261 683 REVISED January 2015...
Страница 256: ...255 P N 12261 683 REVISED January 2015...
Страница 257: ...T300 1_T500 1_T780 Maintenance 256 P N 12261 683 REVISED January 2015...
Страница 258: ...257 P N 12261 683 REVISED January 2015...
Страница 259: ...Engine Indicator Lamps T300 1_T500 1_T780 Maintenance 258 P N 12261 683 REVISED January 2015...
Страница 260: ...259 P N 12261 683 REVISED January 2015...
Страница 261: ...T300 1_T500 1_T780 Maintenance 260 P N 12261 683 REVISED January 2015...
Страница 262: ...261 P N 12261 683 REVISED January 2015...
Страница 263: ...T300 1_T500 1_T780 Maintenance 262 P N 12261 683 REVISED January 2015...
Страница 264: ...263 P N 12261 683 REVISED January 2015...
Страница 266: ...Operating Characteristics with Aftertreatment Particulate Filter 265 P N 12261 683 REVISED January 2015...
Страница 267: ...T300 1_T500 1_T780 Maintenance 266 P N 12261 683 REVISED January 2015...
Страница 268: ...267 P N 12261 683 REVISED January 2015...
Страница 269: ...T300 1_T500 1_T780 Maintenance 268 P N 12261 683 REVISED January 2015...
Страница 270: ...269 P N 12261 683 REVISED January 2015...
Страница 271: ...Engine Indentification T300 1_T500 1_T780 Maintenance 270 P N 12261 683 REVISED January 2015...
Страница 272: ...271 P N 12261 683 REVISED January 2015...
Страница 273: ...T300 1_T500 1_T780 Maintenance 272 P N 12261 683 REVISED January 2015...
Страница 274: ...273 P N 12261 683 REVISED January 2015...
Страница 275: ...T300 1_T500 1_T780 Maintenance 274 P N 12261 683 REVISED January 2015...
Страница 276: ...275 P N 12261 683 REVISED January 2015...
Страница 277: ...Diesel Exhaust Fluid Specification T300 1_T500 1_T780 Maintenance 276 P N 12261 683 REVISED January 2015...
Страница 278: ...277 P N 12261 683 REVISED January 2015...
Страница 279: ...T300 1_T500 1_T780 Maintenance 278 P N 12261 683 REVISED January 2015...
Страница 280: ...279 P N 12261 683 REVISED January 2015...
Страница 281: ...T300 1_T500 1_T780 Maintenance 280 P N 12261 683 REVISED January 2015...
Страница 284: ...Lubrication Charts 283 P N 12261 683 REVISED January 2015...
Страница 285: ...T300 1_T500 1_T780 Maintenance 284 P N 12261 683 REVISED January 2015...
Страница 286: ...285 P N 12261 683 REVISED January 2015...
Страница 306: ...305 P N 12261 683 REVISED January 2015...
Страница 317: ...T300 1_T500 1_T780 Maintenance 316 P N 12261 683 REVISED January 2015...
Страница 345: ...T300 1_T500 1_T780 Maintenance 344 P N 12261 683 REVISED January 2015...
Страница 348: ...Recommeded Fluid Filter Change Intervals 347 P N 12261 683 REVISED January 2015...
Страница 349: ...T300 1_T500 1_T780 Maintenance 348 P N 12261 683 REVISED January 2015...
Страница 354: ...353 P N 12261 683 REVISED January 2015...
Страница 365: ...T300 1_T500 1_T780 Maintenance 364 P N 12261 683 REVISED January 2015...
Страница 381: ......
Страница 433: ......
Страница 437: ...1 Proximity Sensor Outrigger Position T300 1_T500 1_T780 Service Parts 436 P N 12261 683 REVISED January 2015...
Страница 439: ...T300 1_T500 1_T780 Service Parts 438 P N 12261 683 REVISED January 2015...
Страница 455: ...1 Lock Nut 2 Adjusting Nut T300 1_T500 1_T780 Service Parts 454 P N 12261 683 REVISED January 2015...
Страница 465: ...Engine Clutch Adjustment Repair T300 1_T500 1_T780 Service Parts 464 P N 12261 683 REVISED January 2015...
Страница 466: ...465 P N 12261 683 REVISED January 2015...
Страница 467: ...T300 1_T500 1_T780 Service Parts 466 P N 12261 683 REVISED January 2015...
Страница 473: ...1 SELECTION LEVER 2 SHIFT ARM T300 1_T500 1_T780 Service Parts 472 P N 12261 683 REVISED January 2015...
Страница 476: ...1 Swing Reducer Dipstick 2 Shim 3 Thrust Bushings 475 P N 12261 683 REVISED January 2015...
Страница 501: ...T300 1_T500 1_T780 Service Parts 500 P N 12261 683 REVISED January 2015...
Страница 510: ...509 P N 12261 683 REVISED January 2015...
Страница 512: ...511 P N 12261 683 REVISED January 2015...
Страница 513: ......
Страница 520: ...Torque Specs SAE Metric 519 P N 12261 683 REVISED January 2015...
Страница 521: ...T300 1_T500 1_T780 Appendix 520 P N 12261 683 REVISED January 2015...
Страница 527: ...Notes T300 1_T500 1_T780...