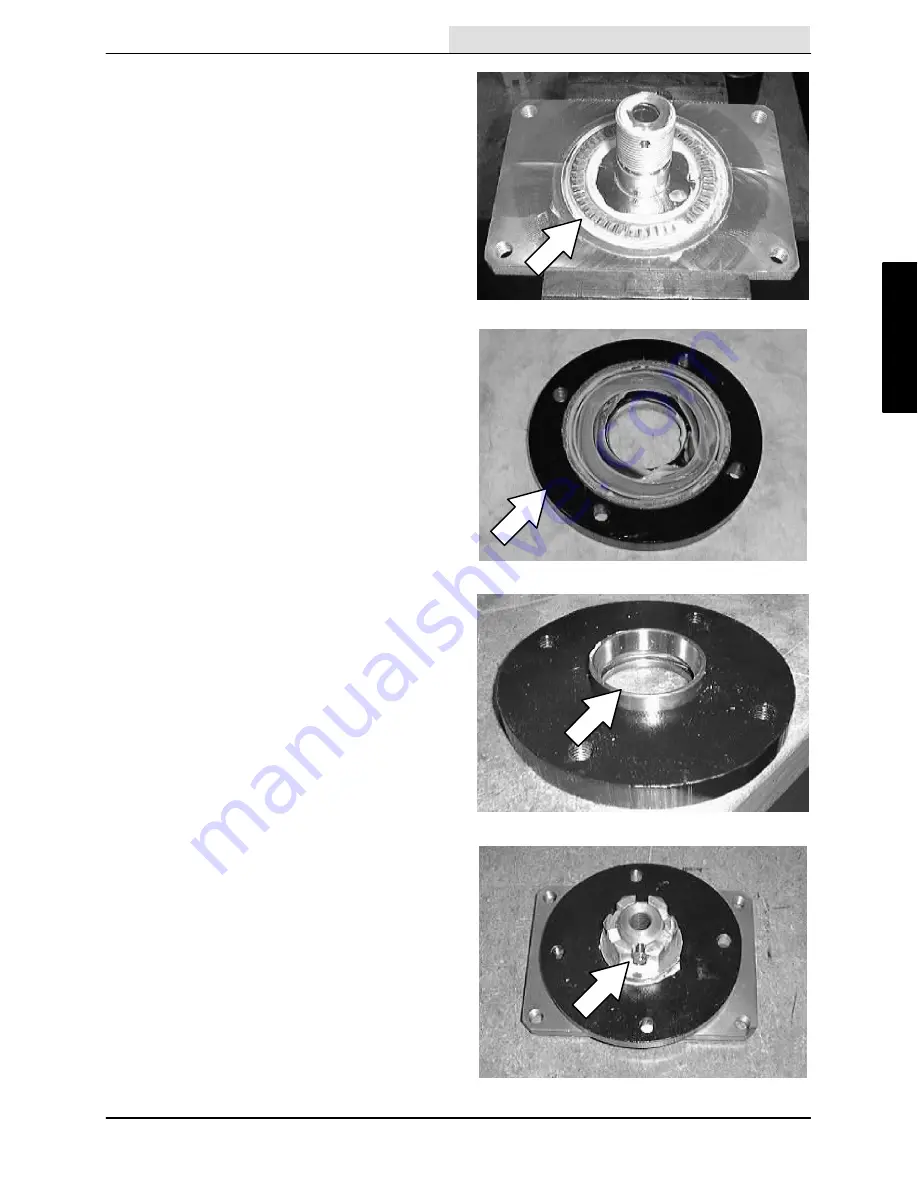
CHASSIS
2--47
6100 G/LP 330235 (9--00)
12. Remove and discard the upper thrust
washer. Remove and discard the needle
bearing and lower thrust washer.
13. Install the new thrust washer onto the swivel
plate weldment.
14. Grease the new needle bearing and position
on top of the new thrust washer. Install the
second thrust washer on top of the needle
bearing.
15. Reinstall the swivel plate onto the swivel
plate weldment.
NOTE: Make sure the rubber seal ring is in place
on the swivel plate before installing.
16. Reinstall the cone bearing in the swivel
plate.
Grease the bearing if needed.
17. Reinstall the large flat washer and castle
nut. Tighten to 37 -- 48 Nm (26 -- 34 ft. lb).
Reinstall the small thread roller into the
cross hole.
Back off the castle nut if needed
to align cross hole.
Содержание 6100 G/LP
Страница 1: ...330235 Rev 02 9 01 Service Manual 6100 G LP ...
Страница 4: ...GENERAL INFORMATION 1 2 6100 G LP 330235 9 01 ...
Страница 18: ...CHASSIS 2 2 6100 G LP 330235 9 00 ...
Страница 27: ...CHASSIS 2 11 6100 G LP 330235 9 00 7 Remove the hub assembly from the tire assembly ...
Страница 72: ...CHASSIS 2 56 6100 G LP 330235 9 00 ...
Страница 74: ...SWEEPING 3 2 6100 G LP 330235 9 00 ...
Страница 152: ...ELECTRICAL 4 2 6100 G LP 330235 9 00 ...
Страница 175: ...ELECTRICAL 4 25 6100 G LP 330235 9 01 ...
Страница 176: ...ELECTRICAL 4 26 6100 G LP 330235 9 01 ELECTRICAL SCHEMATIC GAS 1 2 3 4 ...
Страница 177: ...ELECTRICAL 4 27 6100 G LP 330235 9 01 ELECTRICAL SCHEMATIC GAS 1 2 3 4 ...
Страница 178: ...ELECTRICAL 4 28 6100 G LP 330235 9 01 ELECTRICAL SCHEMATIC LP 1 2 3 4 ...
Страница 179: ...ELECTRICAL 4 29 6100 G LP 330235 9 01 ELECTRICAL SCHEMATIC LP 1 2 3 4 ...
Страница 180: ...ELECTRICAL 4 30 6100 G LP 330235 9 01 WIRE DIAGRAM GAS LP ...
Страница 181: ...ELECTRICAL 4 31 6100 G LP 330235 9 01 WIRE DIAGRAM GAS LP ...
Страница 182: ...ELECTRICAL 4 32 6100 G LP 330235 9 01 ...
Страница 190: ...ELECTRICAL 4 40 6100 G LP 330235 9 00 ...
Страница 192: ...HYDRAULICS 5 2 6100 G LP 330235 9 00 ...
Страница 198: ...HYDRAULICS 5 8 6100 G LP 330235 9 00 9 Disengage the prop rod and close the seat support ...
Страница 205: ...HYDRAULICS 5 15 6100 G LP 330235 9 00 10 Disengage the seat rod and close the seat assembly ...
Страница 217: ...HYDRAULICS 5 27 6100 G LP 330235 9 00 HYDRAULIC SCHEMATIC ...
Страница 218: ...HYDRAULICS 5 28 6100 G LP 330235 9 00 OUT IN B A B A HYDRAULIC HOSE DIAGRAM ...
Страница 220: ...HYDRAULICS 5 30 6100 G LP 330235 9 00 ...
Страница 221: ......
Страница 222: ......
Страница 223: ......
Страница 224: ......
Страница 225: ......
Страница 226: ......
Страница 227: ......
Страница 228: ......
Страница 229: ......
Страница 230: ......
Страница 231: ......
Страница 232: ......
Страница 233: ......
Страница 234: ......
Страница 235: ......
Страница 236: ......
Страница 237: ......
Страница 238: ......
Страница 239: ......
Страница 240: ......
Страница 241: ......
Страница 242: ......
Страница 243: ......
Страница 244: ......
Страница 245: ......
Страница 246: ......
Страница 247: ......
Страница 248: ......
Страница 249: ......
Страница 250: ......
Страница 252: ...ENGINE GAS LP 6 2 6100 G LP 330235 9 00 ...
Страница 274: ...ENGINE GAS LP 6 24 6100 G LP 330235 9 00 ...