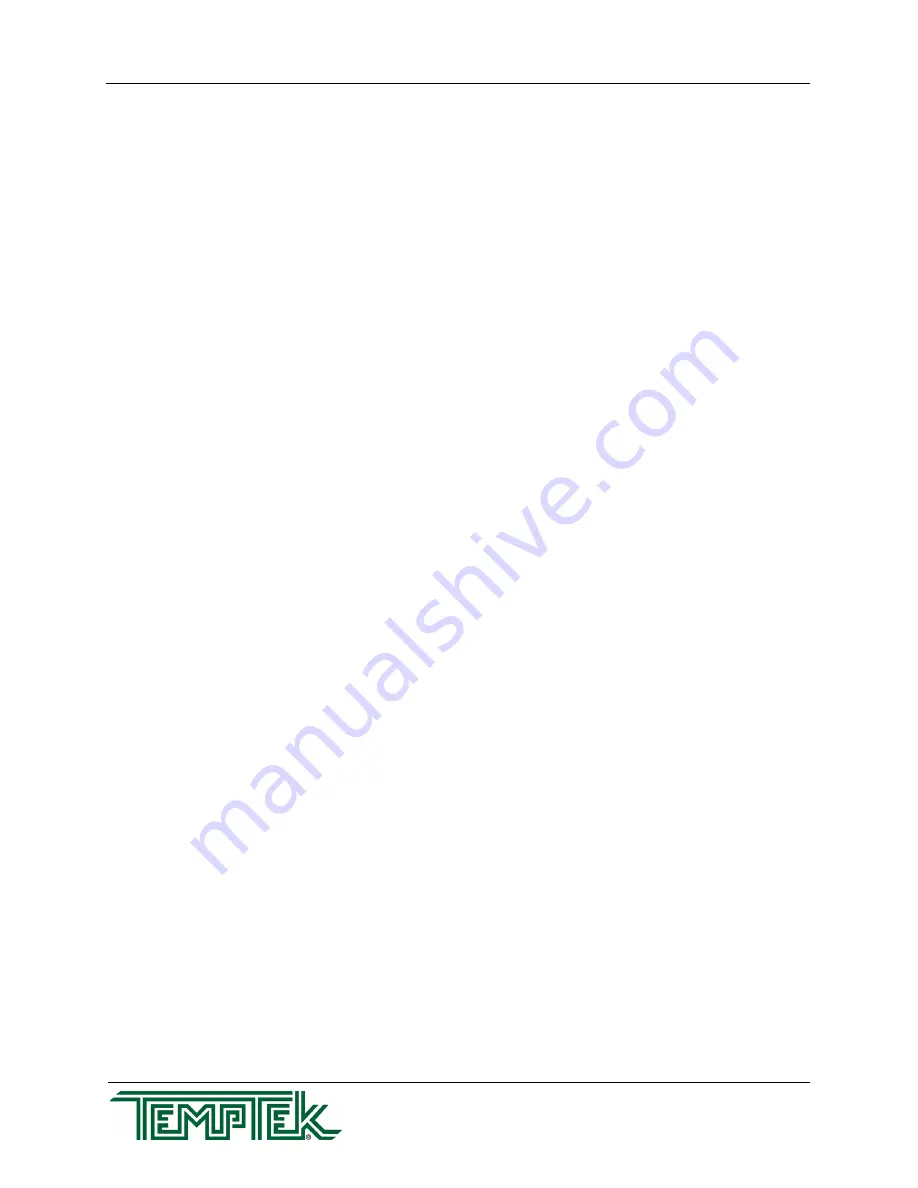
PTK Series Polyethylene Pump Tank Station with Checkmate Control System
Page: 24
TEMPTEK, INC.
525 East Stop 18 Road Greenwood, Indiana 46142
317-887-6352 Fax: 317-881-1277
Email: [email protected]
4.4
DISPLAY CALIBRATION
A.
There are two calibration potentiometers on the back of Checkmate instrument. One
potentiometer calibrates the To Process probe and the other potentiometer calibrates the
other probes (From Process, To Tower, From Tower).
B.
The procedure described here avoids the necessity of removing any of the probes from
the pipes or manifolds. It requires that you are able to independently determine the
temperature of the water on the ‘Cold’ side of the system water tank. This is the side of
the tank that receives cooled water from the tower cell.
C. Preparation.
1.
You will need the following to complete the calibration procedure.
a.
A small screw driver to adjust the potentiometers on the circuit board.
b.
A temperature measuring meter with a probe long enough to be
immersed on the system tank.
2.
Warning. The system must be powered to perform the calibration. Some of the
components on the Checkmate controller board are connected to 110 VAC.
Toughing any components (other than the potentiometers) carries the risk of
serious electrical shock. Calibration should only be performed by a qualified
technician.
D.
To Process Probe Calibration
1.
Observe the temperature of the independent temperature meter. Ensure that it is
stable.
2.
Configure the Checkmate Display to show the To Process Temperature.
3.
Adjust the ‘Probe Cal’ potentiometer by 1/4 turn. Wait 30 seconds for the
adjustment to take effect.
4.
Repeat step 3 until the temperature displayed by the Checkmate agrees with the
independent temperature meter.
Note: This potentiometer only affects the To Process temperature.
E.
From Process Probe Calibration
1.
Observe the temperature of the independent temperature meter. Ensure that it is
stable.
2.
Configure the Checkmate Display to show the From Process temperature.
3.
Adjust the ‘All Other’ potentiometer by 1/4 turn. Wait 30 seconds for the
adjustment to take effect.
Содержание PTK Series
Страница 30: ...Page 30 END 2019 TEMPTEK INC RE 09 30 2019 ...