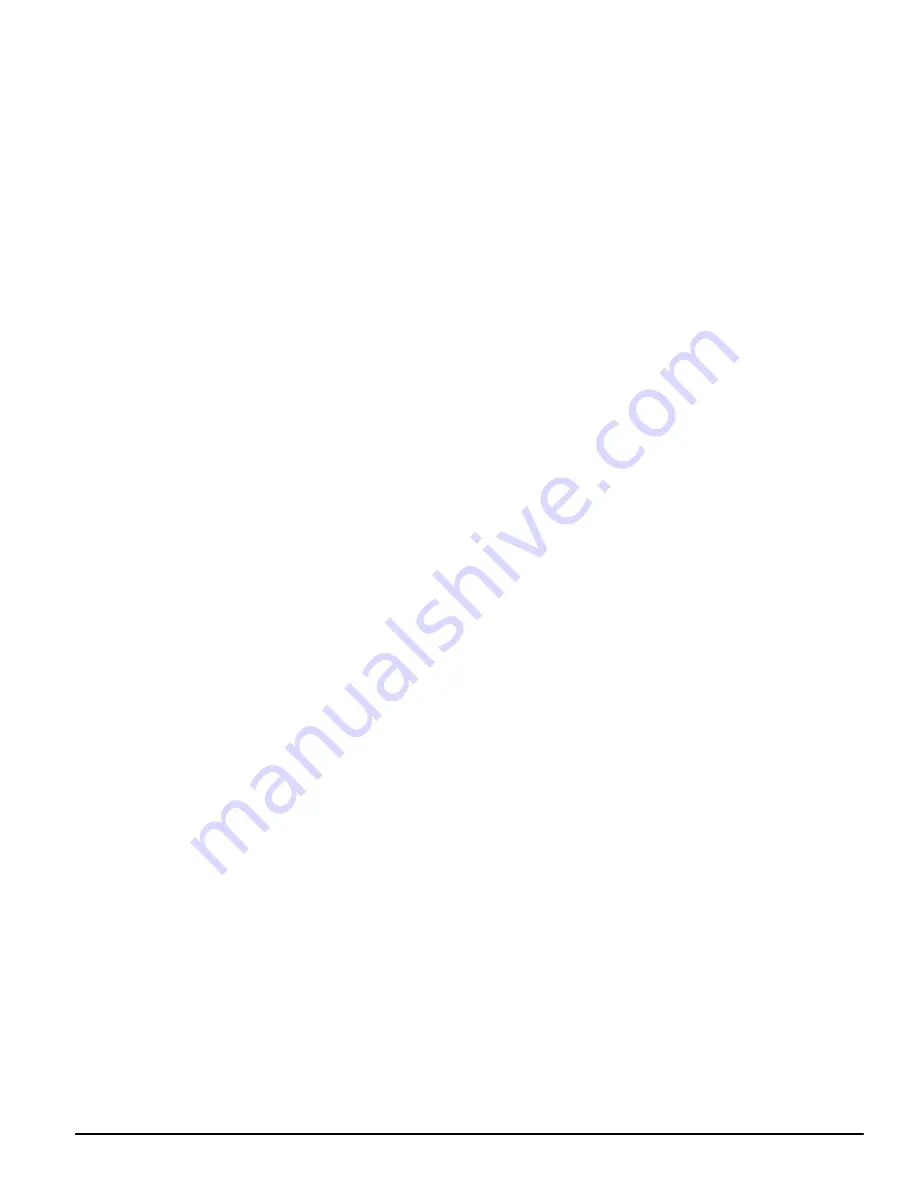
46
441 01 2101 05
Specifications are subject to change without notice.
a. Inducer Prepurge Period (see Figure 55 schematic
diagram)
(1.) Low heat (W/W1) the inducer motor IDM comes
up to high
−
speed, the low
−
heat pressure switch
LPS closes. After the low
−
heat pressure switch
closes the furnace control CPU will begin a
15
−
second prepurge period, and continue to run
the inducer motor IDM at high
−
speed.
(2.) High Heat (W/W1+W2) the inducer motor IDM
comes up to high speed and the high
−
heat
pressure switch relay HPSR is de
−
energized to
close the NC contact. When sufficient pressure
is available, the high
−
heat pressure switch HPS
closes, and the high
−
heat gas valve solenoid
GV
−
HI is energized. After LPS closes, 24VAC
power is supplied for a field
−
installed humidifier
at the HUM 24VAC terminal and the furnace
control CPU begins a 15
−
second prepurge
period. If the high
−
heat pressure switch HPS fails
to close and the low
−
heat pressure switch LPS
closes, the furnace will operate at low
−
heat gas
flow rate until the high
−
heat pressure switch
closes for a maximum of 2 minutes after ignition.
If HPS doesn’t close after 2 minutes from LPS
closing, GV is turned off and heat off delay is
completed. Then a new cycle will begin if a call
for heat remains.
b.
Igniter Warm
−
Up
−
At the end of the prepurge period,
the (Hot Surface Igniter) HSI is energized for a
17
−
second igniter warm
−
up period.
c.
Trial
−
for
−
Ignition Sequence
−
When the igniter
warm
−
up period is completed the main gas valve relay
contacts GVR close to energize the gas valve solenoid
GV
−
M, the gas valve opens. The gas valve solenoid
GV
−
M permits gas flow to the burners where it is
ignited by the HSI. 5 sec after the GVR closes, a 2
−
sec
flame proving period begins. The HSI igniter will
remain energized until the flame is sensed or until the
2
−
sec flame proving period begins. If the furnace
control CPU operates in high
−
heat operation, the
high
−
heat gas valve solenoid GV
−
HI is also
energized.
d.
Flame
−
Proving
−
When the burner flame is proved at
the flame
−
proving sensor electrode FSE, the inducer
motor IDM switches to low
−
speed unless running at
high
−
heat, and the furnace control CPU begins the
blower
−
ON delay period and continues to hold the gas
valve GV
−
M open. If the burner flame is not proved
within two seconds, the control CPU will close the gas
valve GV
−
M, and the control CPU will repeat the
ignition sequence for up to three more
Trials
−
For
−
Ignition before going to Ignition
−
Lockout.
Lockout will be reset automatically after three hours,
or by momentarily interrupting 115 vac power to the
furnace, or by interrupting 24 vac power at 24VAC or
COM to the furnace control CPU (not at W/W1, G, R,
etc.). If flame is proved when flame should not be
present, the furnace control CPU will lock out of
Gas
−
Heating mode and operate the inducer motor
IDM on high speed until flame is no longer proved.
e.
Blower On Delay
−
If the burner flame is proven, the
blower on delay for low
−
heat and high
−
heat are as
follows:
Low
−
Heat
−
45 seconds after the gas valve
GV
−
M is energized the blower motor (BLWM) is
energized at LO HEAT speed.
High
−
Heat
−
25 seconds after the gas valve GV
−
M is
energized the BLWM is energized at HI HEAT speed.
Simultaneously, the electronic air cleaner (EAC 1
AMP) terminal is energized and remains energized as
long as the BLWM is energized.
f.
Switching from Low
−
to High
−
Heat
−
If the furnace
control CPU switches from low
−
heat to high
−
heat, the
furnace control CPU will switch the inducer motor IDM
speed from low to high. The high
−
heat pressure switch
relay HPSR is de
−
energized to close the NC contact.
When sufficient pressure is available the high
−
heat
pressure switch HPS closes, and the high
−
heat gas
valve solenoid GV
−
HI is energized. The blower motor
BLWM will switch to HI HEAT speed 5 seconds after
the furnace control CPU switches from low
−
heat to
high
−
heat.
g.
Switching from High
−
to Low
−
Heat
−
The furnace
control CPU will not switch from high
−
heat to low
−
heat
while the thermostat R
−
to
−
W circuit is closed when
using a single stage thermostat.
h.
Heat
−
Off Delay
−
When the thermostat is satisfied, the
R to W circuit is opened, de
−
energizing the gas valve
GV
−
M, stopping gas flow to the burners, and
de
−
energizing the humidifier terminal HUM 24VAC.
The inducer motor IDM will remain energized for a
5
−
second post
−
purge period then turn off, also
turning off HUM for 115V humidifier. The blower motor
BLWM and air cleaner terminal EAC 1 AMP will remain
energized for 90, 120, 150, or 180 seconds
(depending on selection at heat
−
off delay switches).
The furnace control CPU is factory
−
set for a
120
−
second heat
−
off delay.
2.
Two
−
Stage Thermostat and Two
−
Stage Heating
(See Figure 31 for thermostat connections)
NOTE
: In this mode the TT switch (SW1
−
1) must be ON to
select the two
−
stage thermostat mode in response to closing
the thermostat R
−
to
−
W1 circuit. Closing the thermostat
R
−
to
−
W1
−
and
−
W2 circuits always causes high
−
heat
operation, regardless of the setting of the thermostat type.
The wall thermostat “calls for heat”, closing the R
−
to
−
W1
circuit for low
−
heat or closing the R
−
to
−
W1 and
−
W2 circuits
for high
−
heat. The furnace control performs a self
−
check,
verifies the low
−
heat and high
−
heat pressure switch contacts
LPS and HPS are open, and starts the inducer motor IDM in
high
−
speed.
The start up and shut down functions and delays described in
item 1. above apply to the two
−
stage heating mode as well,
except for switching from low
−
to high
−
heat and vice versa.
a.
Switching from Low
−
to High
−
Heat
−
If the
thermostat R
−
to
−
W1 circuit is closed and the
R
−
to
−
W2 circuit closes, the furnace control CPU will
switch the inducer motor IDM speed from low to high.
The high
−
heat pressure switch relay HPSR is
de
−
energized to close the NC contact. When sufficient
pressure is available the high
−
heat pressure switch
HPS closes, and the high
−
heat gas valve solenoid
GV
−
HI is energized. The blower motor BLWM will
switch to HI HEAT speed five seconds after the
R
−
to
−
W2 circuit closes.
b.
Switching from High
−
to Low
−
Heat
−
If the
thermostat R
−
to
−
W2 circuit opens, and the R
−
to
−
W1
circuit remains closed, the furnace control CPU will
switch the inducer motor IDM speed from high to low.
The high
−
heat pressure switch relay HPSR is
energized to open the NC contact and de
−
energize
the high
−
heat gas valve solenoid GV
−
HI. When the
inducer motor IDM reduces pressure sufficiently, the
high
−
heat pressure switch HPS will open. The gas
valve solenoid GV
−
M will remain energized as long as
the low
−
heat pressure switch LPS remains closed.
The blower motor BLWM will switch to LO HEAT speed
5 seconds after the R
−
to
−
W2 circuit opens.
3.
Cooling Mode
−
The thermostat “calls for cooling.”
a.
Single
−
Speed Cooling
−
(See Figure 23 for thermostat connections)
The thermostat closes the R
−
to
−
G
−
and
−
Y circuits.
The R
−
to
−
Y circuit starts the outdoor unit, and the
furnace control R
−
to
−
G
−
and
−
Y/Y2 circuits start the