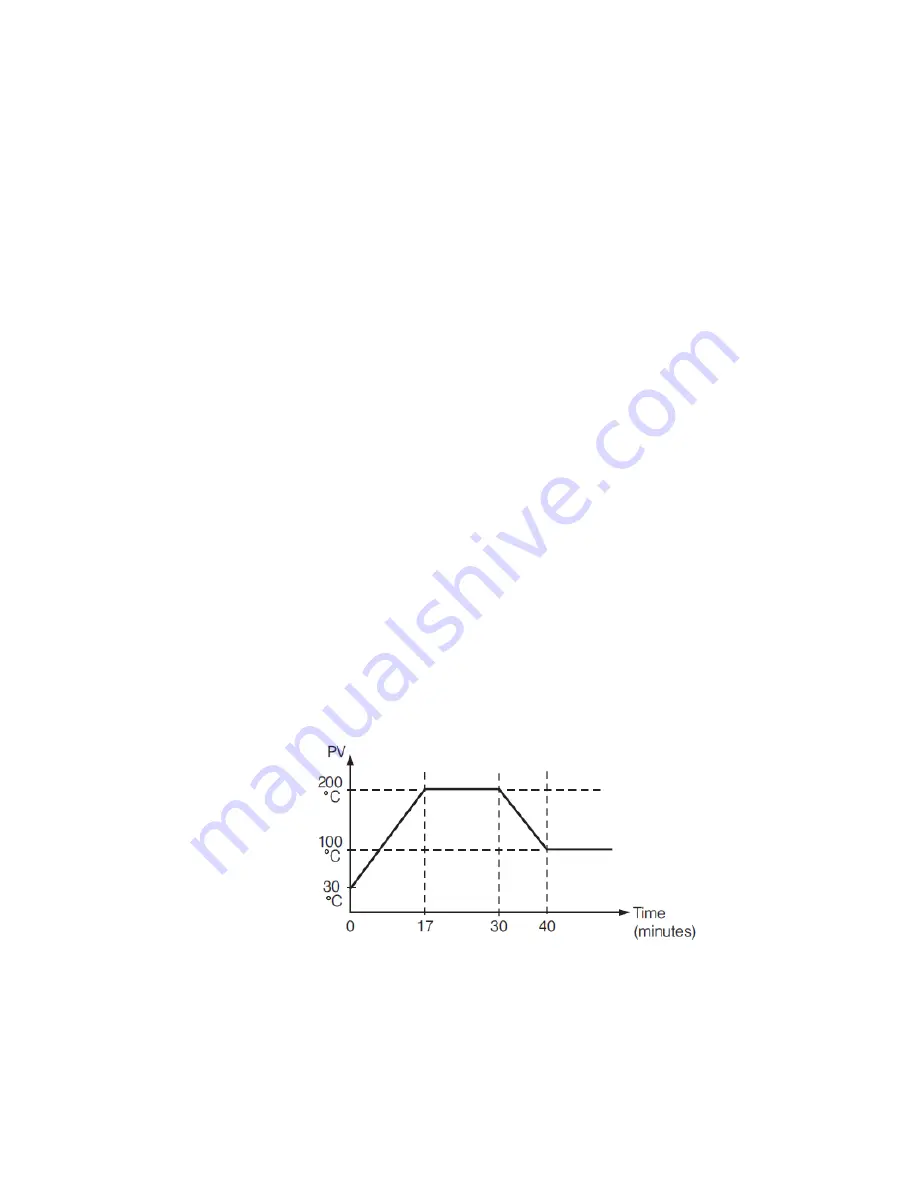
Page 13 of 18
2.3.3
Heat only PID Control – (Default for Electric Heaters)
Select REVR for OUT1. PB and TI should not be zero. Perform Auto-Tuning for initial startup. If the control
result is not satisfactory, use manual tuning or try Auto-Tuning a second time to improve the control
performance.
2.3.4
Cool only Control
ON-OFF control, Proportional control, and PID control can be used for cooling control. Set “OUT1” to DIRT
(direct action).
NOTE: ON-OFF control may result in excessive overshoot and undershoot in the process. Proportional
control could result in a deviation of the process value from the set point. It is recommended to use PID
control for Heating or Cooling control to produce a stable process value.
When selecting parameters, all of the above parameters may not be available. The number of visible
parameters depends on the configuration of the controller.
2.4
Ramp
The ramping function is performed during power up or any time the set point is changed. Choose “MINR”
(ramp in minutes) or “HRR” (ramp in hours) for the “RAMP” setting, and the controller will perform the
ramping function. The ramp rate is programmed by adjusting the “RR” setting. The ramping function is
disabled whenever the controller enters Failure mode, Manual control mode, Auto-Tuning mode or
Calibration mode.
2.4.1
Ramping Example without Dwell Timer
Set the “RAMP” setting to “MINR” to ramp in minutes.
Set the ramp rate (RR) to 10.
The starting temperature is 30°C.
The setpoint is initially set to 200°C.
After the process warms up, the user changed the setpoint to 100°C after 30 minutes.
After power up, the process will behave as shown below.
2-2.Ramp Function