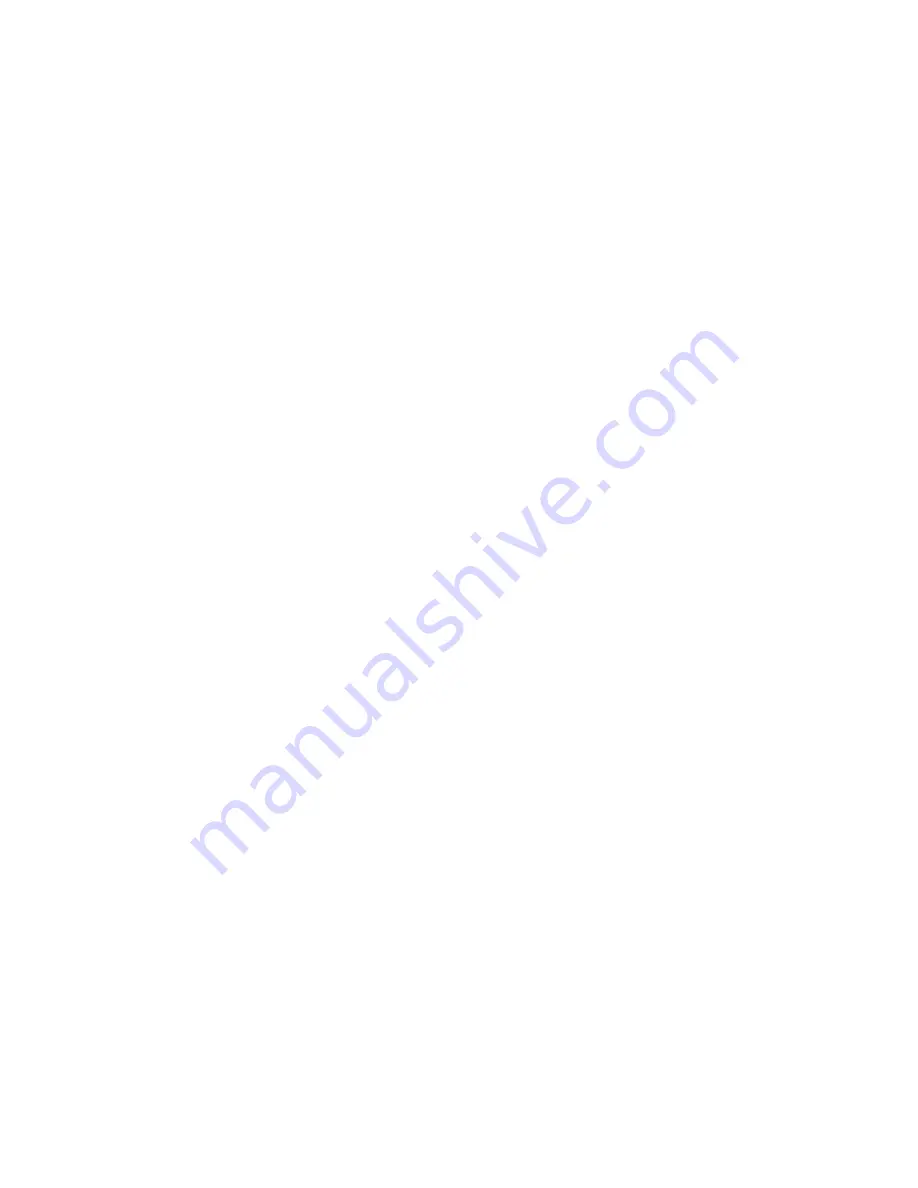
Page 3 of 4
Wiring Precautions:
• Before wiring, verify the correct model number and
options on the label. Switch off the power while
checking.
• Care must be taken to ensure that the maximum voltage
rating specified on the label is not exceeded.
• It is recommended that the power for these units be
protected by fuses or circuit breakers rated at the
minimum value possible.
• All units should be installed in a suitable enclosure to
prevent live parts from being accessible to human hands
and metal tools. Metal enclosures and/or subpanels
should be grounded in accordance with national and
local codes.
• All wiring must conform to appropriate standards of
good practice and local codes and regulations. Wiring
must be suitable for the voltage, current, and
temperature rating of the system.
• Beware not to over-tighten the terminal screws. The
torque should not exceed 1 N-m (8.9 lb-in or 10 KgF-cm).
• Unused control terminals should not be used as jumper
points as they may be internally connected, causing
damage to the unit.
• Verify that the ratings of the output devices and the
inputs as specified are not exceeded.
• Except for thermocouple wiring, all wiring should use
stranded copper conductor with a maximum gage of 14
AWG.
• Electrical power in industrial environments contains a
certain amount of noise in the form of transient voltage
and spikes. This electrical noise can adversely affect the
operation of microprocessor-based controls. For this
reason the use of shielded thermocouple extension wire
which connects the sensor to the controller is strongly
recommended. This wire is a twisted-pair construction
with foil wrap and drain wire. The drain wire is to be
attached to ground in the control panel only.
General Operation
Adjust the digital set point to the temperature desired. The
“OUT” lamp will glow red, indicating that the control is
calling for heat, and the relay is closed. As the process
temperature approaches the set point, the control will
begin to cycle the heaters on and off. When the heater load
is turned off, the “OUT” lamp will not be lit. The actual
process temperature measured by the sensor is indicated
on the digital LED display.
Calibration Instructions
Calibration is performed using the four potentiometers
located on the bottom of the left-hand circuit board. Open
the control by unlatching the clamps on the top and
bottom of the front of the control. Allow the control to
warm up for at least half an hour before checking the
calibration. The functions of the potentiometers is as
follows: VR1 Low scale calibration
VR2 Low scale switching point
VR3 High scale switching point
VR4 High scale calibration
You must set the “reset” adjustment to zero before
calibration. VR1 and VR4 affect each other, so you should
calibrate low scale and high scale at least three times each.
Alarm Operation (Optional)
The TEC-805 has the option of coming equipped with a
form-A relay that can be used as a deviation alarm. It is
called a deviation alarm because the alarm set point
maintains the same deviation from the control set point, so
if the control set point is changed, the alarm set point will
change with it. The relay is rated for a maximum load of 2
amps, 240 volts. On units that have been ordered with the
alarm option, there will be an alarm set point adjustment
on the front of the control. The alarm can be adjusted from
0–10% of the range of the control from the set point, in
either direction. If the alarm adjustment is set to the
positive side, it will act as a deviation high alarm, if it is set
to the negative side, it will act as a deviation low alarm. If
it is set at 0, the alarm will energize at the control set point.
WARNING:
Failure of the thermocouple-RTD sensor, heater output
relay, temperature control, or other devices can result in
severe damage to a product while in process, melting of
the heater, or a damaging fire. An over-temperature
protection device must be included in your process that
will remove all power from the heater circuit if any of the
above failures occur. It is recommended that this device be
classified as a safety control. Failure to install such a
device where a potential hazard exists could result in
damage to equipment and property, and injury to
personnel.
Troubleshooting
Common causes of failures:
• Line wires improperly connected
• Incorrect voltage between line terminals
• No voltage between line terminals
• Connections to terminals are loose, open, or missing
• Short across terminals
• Shorted thermocouple leads
• Thermocouple is open at tip
• Thermocouple lead is broken
• Open or shorted heater circuit
• Open coil in external contactor
• Burned out contactor
• Burned out line fuses
• Defective line switches
• Defective circuit breakers.
If the control still does not function after these points have
been checked, the instrument should be returned to
Tempco for inspection. Make sure to use adequate
packing materials to prevent damage during shipment.
Note that no products returned can be accepted without a
completed Return Material Authorization (RMA) form.