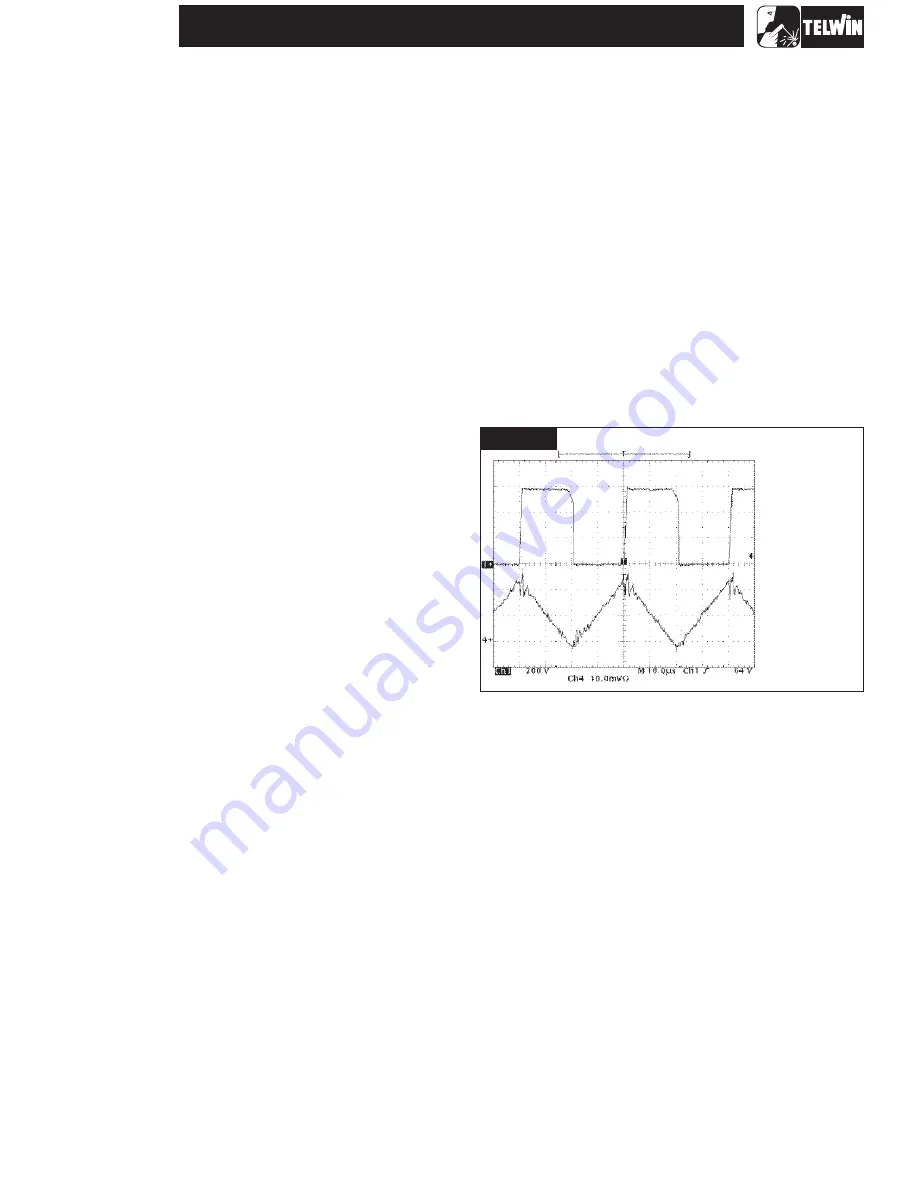
B) Removing the secondary board (fig. 5)
C) Replacing the control board (fig. 2A)
1.1 Preparation for testing
1.2 Scheduled tests
Unless the dissipator has been damaged by a destructive
explosion of the diodes, the secondary board should not generally
be removed and the diodes can be replaced directly with the board
mounted on the machine. In any case, it should be specified that to
remove it is necessary to
:
-
remove the base by undoing the 4 screws;
-
turn the machine upside down and undo the 6 screws
fastening the base assembly to the metal structure;
-
disconnect all wiring that hampers removal of the base
assembly;
-
after separating the base assembly disconnect the fastons
from the thermostatic capsule and make the replacement.
For assembly proceed in the reverse order.
-
operating on the upturned machine, undo the screws fastening
the damaged components to the dissipator and unsolder the
metal tab;
-
after removing the components clean the dissipator, removing
dirt and irregularities;
-
apply thermoconductive grease following the general
instructions;
-
place the components on the dissipator to correspond with the
soldering zones and fasten them down with the screws (torque
wrench setting 1.4 Nm 20%);
-
solder the rheofores taking care not to let the tin form short
circuits.
make sure that R1 and C1 (secondary snubber) are correctly
soldered to the PCB.
If the fault is in the control board we strongly advise replacing it
without further intervention.
-
undo the 4 screws on the front panel;
-
disconnect all the connectors.
For assembly proceed in the reverse order.
Testing should be carried out on the assembled machine before
closing the top cover. During tests never ever commute the
selectors or operate the ohmic load contactor with the machine in
operation.
A) Using cables with suitable dinse connectors, connect the
machine to the ohmic load (two ohmic loads connected in parallel
should be available).
To connect the negative of the ohmic loads to the torch
connector it is necessary to use the adapter with torch button
simulator. If no adapter is available, it can always be ordered from
Telwin.
B) Connect a voltage probe x100 between the collector (probe)
and emitter (earth) of IGBT 6.
C) Pass the current probe of the Hall effect transducer along the
cable connecting the power transformer at eyelet C BASSO with
the reference arrow pointing into C BASSO.
D) Lastly, connect the Hall Probe and the current probe to the
oscilloscope.
E) Keep the auxiliary cables (
and
) connected to the
machine as previously.
F) On the control board position the current potentiometer to
minimum.
G) Connect the power supply cable of the machine to a 3-phase
variac with variable output 0-500 Vac.
To obtain the waveform it is necessary to press the torch
button simulator several times, because the machine remains
switched on for a maximum of about 2 seconds.
-
with the loads switched off, set the machine in “
”, by
first pressing the air button on the front panel and then closing
switch SW1 (ON) of the wiring in fig. A. Keep the air button
pressed for more than 6 sec, after which diode D3 will start to
flash (this status will remain until the machine is switched off).
In this mode we disable HF (which is lethal to any
instrument connected to the machine) and air input. Before
continuing testing make sure the machine is in test mode.
-
switch on the machine and the variac and take the latter to 400
Vac.
-
press the torch button simulator and make sure the voltage
and current waveforms displayed on the oscilloscope
resemble those in
-
switch off the auxiliary power supply, the machine and the
variac;
-
disconnect the wiring shown in fig. A from the machine and
restore the original wiring on the auxiliary transformer and on
the power supply board;
-
disconnect the wiring shown in fig. B from the machine and
restore the original wiring between the control board and the
primary board;
-
connect the machine to the 3-phase 400Vac power line.
-
switch on the machine and set it to “
”, by first
pressing the air button on the front panel and then closing the
main switch (ON). Keep the air button pressed for more than 6
sec, after which diode D3 will start to flash (this status will
remain until the machine is switched off).
In this mode we disable HF (which is lethal to any
instrument connected to the machine) and air input.
Before continuing with testing make sure the machine is in test
mode.
set up the ohmic loads with the switch settings as in the table in
-
on the front panel position the current potentiometer to
minimum;
-
start up the ohmic load, press the torch button simulator and
verify that:
-
the waveforms displayed on the oscilloscope resemble
those in
;
-
the output current is equal to +20Adc 10% and the output
voltage is equal to +88Vdc 10%;
(fig. 4)
N.B.
B) Take special note of the procedure for replacing the
secondary diodes:
N.B.
N.B.
N.B.
fig. A
fig. B
N.B.
A) Loadless test:
test mode
N.B.
fig. F.
B) Minimum load test:
test mode
N.B.
fig. G;
fig. G
±
Before proceeding with testing, we should
remind you that during these tests the power source is powered
and therefore the operator is exposed to the danger of electric
shock. The tests described below can be used to check the power
source under load.
±
±
TESTINGTHE MACHINE
WARNING!
-
17
SUPERIOR PLASMA 90 HF
FIGURE F
SETTINGS
PROBE CH1 x10;
5V/Div;
PROBE CH4 = 5A/Divv;
10mV/Div;
10 sec/Div.
VERIFY THAT:
THE FREQUENCY IS
25KHz 5%;
THE AMPLITUDE CH1 IS
560V 10%.
·
·
·
·
·
±
·
±
·
±
Содержание Superior Plasma 90 HF
Страница 7: ...SUPERIOR PLASMA 90 HF 7 General wiring diagram WIRING DIAGRAMS Wiring diagram input filter board...
Страница 8: ...SUPERIOR PLASMA 90 HF 8 Wiring diagram primary board power Wiring diagram primary board driver...
Страница 9: ...SUPERIOR PLASMA 90 HF Wiring diagram control board B Wiring diagram control board A 9...
Страница 10: ...SUPERIOR PLASMA 90 HF Wiring diagram control board D Wiring diagram control board C 10...
Страница 20: ...ILLUSTRATIONS SCREWS SCREW SCREWS TOP COVER SCREWS BOTTOM SCREWS 20 SUPERIOR PLASMA 90 HF SCREW SCREWS SCREWS...