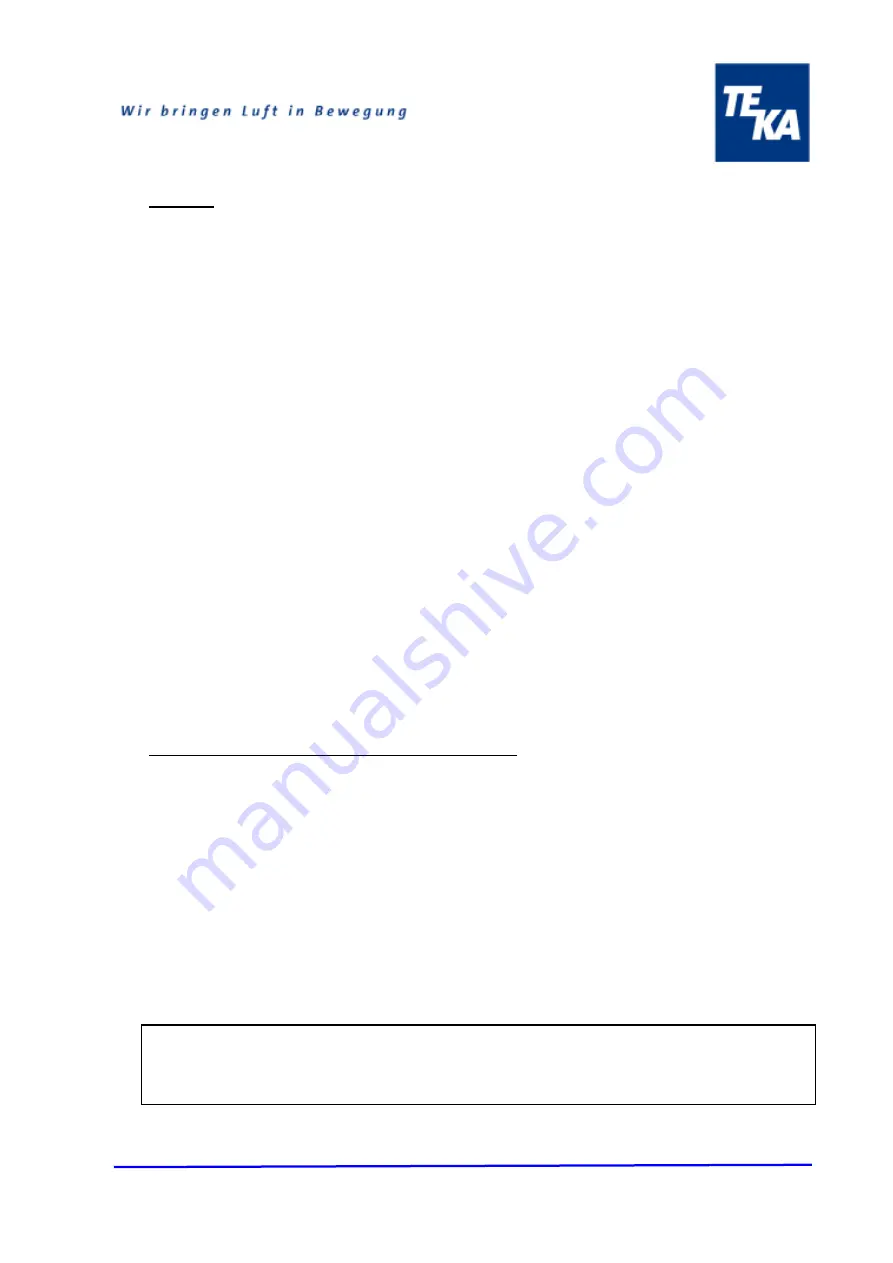
BA_Caremaster-SF1-SF2_BGIA_110901_GB.doc
- 5 -
01.09.2011
2 Preface
One sector of extraction equipment has become very significant in recent years. The filtering of
extracted pollutants and the recycling of filtered air to the working area.
This is a surely a sign that the environmental consciousness of every one of us has altered very
strongly in favour of our environment. For a long time now, no one has denied that pollution occurs
during production. However, the pollutants depend on the process that is used. One can basically
distinguish between gases and fumes (smoke). Fumes could also really be described as dust. If
you examine this dust under a microscope, you will find that they consist of very fine particles, often
with a size of 1
µ
m or smaller, that can enter the lungs.
The classical method of trying to improve the working conditions of polluted workplaces is general
ventilation. In this case, the general rule is a multiple change of air in the workshop, i.e. the
complete volume of air in the workshop is replaced. However, this method only achieves a small
reduction in the level of pollution within the breathing space of the user.
The same applies to “overhead” extraction, i.e. the installation of large extractor hoods above the
workplaces. This is the worst airflow imaginable, since the pollutants first pass through the
breathing space of the user, and only afterwards are they contained and extracted. This is surely
not the point of the exercise. A much more effective method than overhead/wide-area extraction is
the removal of pollutants directly at their source, with localised extraction. Both the investment and
the operating costs are much, much lower if localised extraction is used.
The environmental and workplace-safety measures are especially important requirements for
succesSF-BIAul application of a technology, in addition to the technological optimisation of the
processing method. In a time of increasing sensitivity and tougher legislation, the task therefore lies
in making an early assessment of the potential hazards for the workplace and the environment, and
reducing them as appropriate.
3 Function of the TEKA-CAREMASTER-BGIA
The TEKA–CAREMASTER-BGIA filter unit is primarily used for localised extraction of dust and
smoke particles. For this purpose, the unit can be equipped with one arm.
Limits of application:
welding fumes with oil mist, aluminium dust, gases, water etc.
(If you are uncertain, please contact the manufacturer!)
The polluted air is sucked into the extractor hood (or application-specific fitting) and transported
through the extractor arm (or extractor hose) to the filter unit. Here, the coarse dust particles are
collected in the pre-filter mat (Pos.14). The subsequent particle filter (Pos.15) traps extremely fine
dust particles with an efficiency of better than 99%. The clean air passes the fan and the noise
attenuation module and returns upward into the room via the exhaust grid. The filtered air is then
sucked in by the ventilator and recycled to the air in the workshop through the exhaust grille at the
back of the unit.
Caution:
As soon as the resistance to the air flow from the accumulated dust particles on the filter cartridge
markedly effects the suction performance, the filter elements shall be exchanged.
(refer to chapter 7.1: “Changing of pre-filter mat“ , chapter 7.2: “Change of particle filter“ )