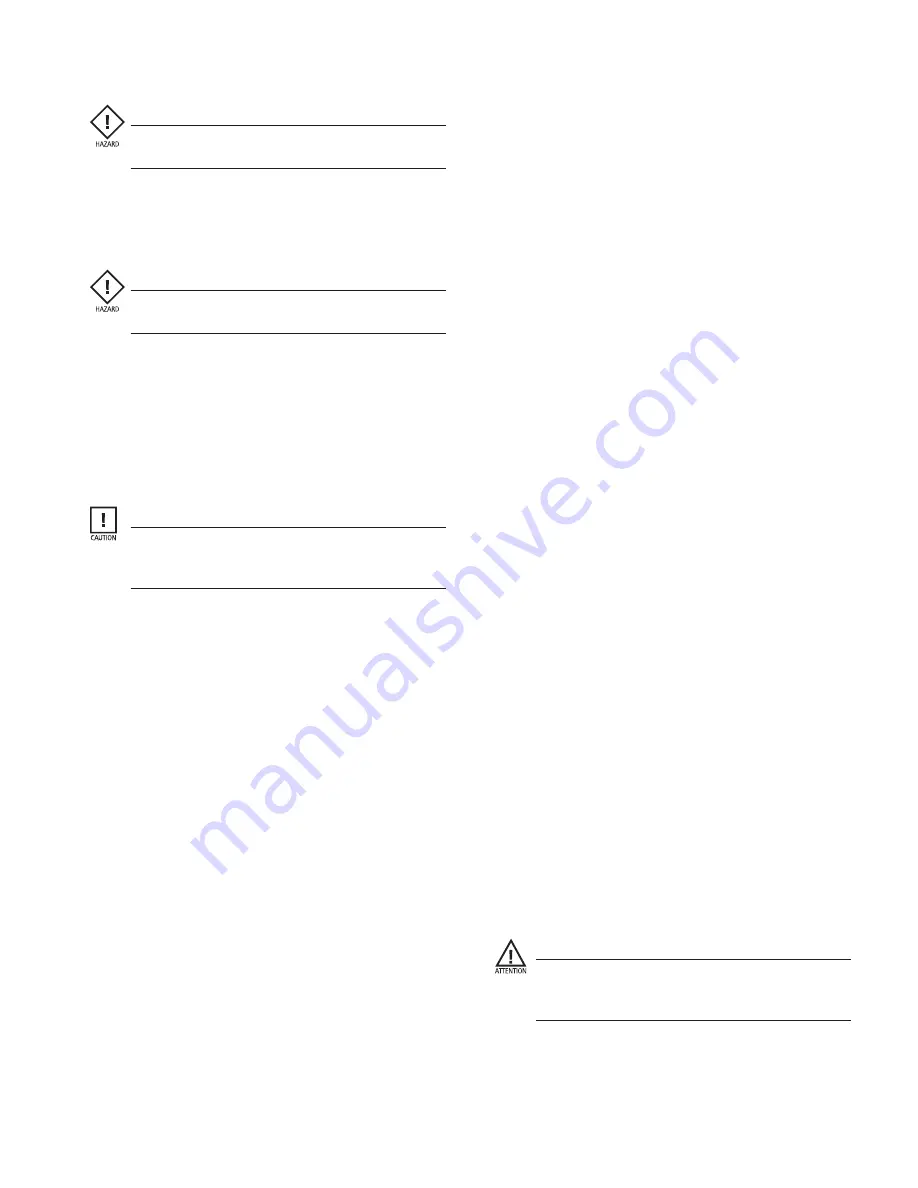
Teikoku USA | Chempump
Instruction Manual HE-12270 (1219)
16
33. Remove socket head cap screws and remove front bearing
housing from stator assembly.
Hazard!
Exercise care while removing this housing because of
liquids which may be contained in the stator assembly.
34. Remove adjusting washers. Record quantity and thickness.
35. Remove rear bearing housing bolts and remove rear bearing
housing from stator assembly. Remove rear bearing housing
gasket.
Hazard!
Exercise care while removing this housing because of
liquids which may be contained in the stator assembly.
36. Remove rotor assembly. Place on a clean cloth to avoid dam-
age. During the removal of the rotor, take care in handling to
prevent damage to the rotor or stator because the rotor will
drop once the armature clears the stator assembly and the
rotor shaft may hit the stator liner if not properly supported.
37. Remove set screw and slide spacer off rotor shaft. Remove
front shaft sleeve and front thrust collar. Anti-rotation pin/key
may be loose and fall out.
Caution!
Do not forcibly remove shaft sleeve. If shaft sleeve does
not slide off easily it may be required to machine or cut
the shaft sleeve off the rotor shaft.
38. To remove rear shaft sleeve and thrust collar, bend tabs up on
lock washer and unscrew bolt. This bolt has left hand threads.
39. Remove rear shaft sleeve and rear thrust collar. Anti-rotation
pin/key may be loose and fall out.
40. To remove bearings, remove set screw, slide out bearing, and
remove flat washer.
41. Remove bearing adjusting washer(s) from rear bearing hous-
ing. Note quantity and measure thickness.
4.3 Inspection
4.3.1 Bearings
Check the following points:
1. Thrust face for scratches and chips. Refer to
Figure 4-3
(L),
for excess wear on thrust surface. (Check this dimension after
bearing has been removed.)
2. Wear inside of bearing bore. Refer to
Figure 4-3
(A-B).
4.3.2 Shaft Sleeves and Thrust Collars
The rotor assembly shaft sleeves and thrust surfaces should also
be visually inspected at the bearing contact area for general ap-
pearance and uniform wear.
Excessive undercutting, pitting, or scoring is cause for replace-
ment.
Check the following points:
1. Corrosion
2. Contact marks and wear.
4.3.3 Rotor Assembly Inspection
The complete rotor assembly should be visually inspected for
cracks, breaks, pitting, or corrosion which might destroy the ef-
fectiveness of the hermetically sealed rotor end covers and sleeve.
Check rotor assembly shafts for straightness.
4.3.4 Stator Assembly Inspection
The complete stator assembly should be visually inspected for
cracks, breaks, pitting, or corrosion of the stator liner which may
destroy the effectiveness of the barrier. Inspect the inside of the
electrical junction box for corrosion and moisture. Teikoku recom-
mends performing a megger and resistance check on the motor
winding.
4.3.5 General Inspection
1. Inspect the threads on both ends of the rotor shaft to ensure
they are not damaged. Type-F (Plan 1-SD) pressurized circula-
tion ALP multi-stage pumps have right-hand threads, except
the rear rotor bolt which has left-hand threads.
2. Be sure that all mating faces are free of nicks and burrs so that
they will have a smooth face ensuring a good seal. Clean off
any trace of old gasket material.
3. Make sure all parts are clean. Inaccessible area may be cleaned
with a small brush or pointed tool.
4. The impeller, casing, and front bearing housing should be in-
spected for wear. If excessive grooving or scoring of the rings
areas, hubs, and bores is evident, these components must be
repaired or replaced.
5. On the rear bearing housing, inspect the ports for circulation
line to ensure that the ports are clear and free of obstructions.
6. Inspect the circulation line restriction orifice for evidence of
corrosion and/or erosion. Verify orifice hole size is correct.
4.4 Reassembly
1. Clean and dry all parts. Reassemble in the reverse manner of
disassembly. Reassembly requires adjustment of end play and
impeller “g” gap.
2. Install adjusting washer(s) into rear bearing housing. Quantity
and thickness of adjusting washers is as required for proper
rotor end play.
Attention!
Both motor bearings have spiral and straight grooves
Figure 4-2
. The front bowl bearing has only straight
grooves.
Figure 4-1