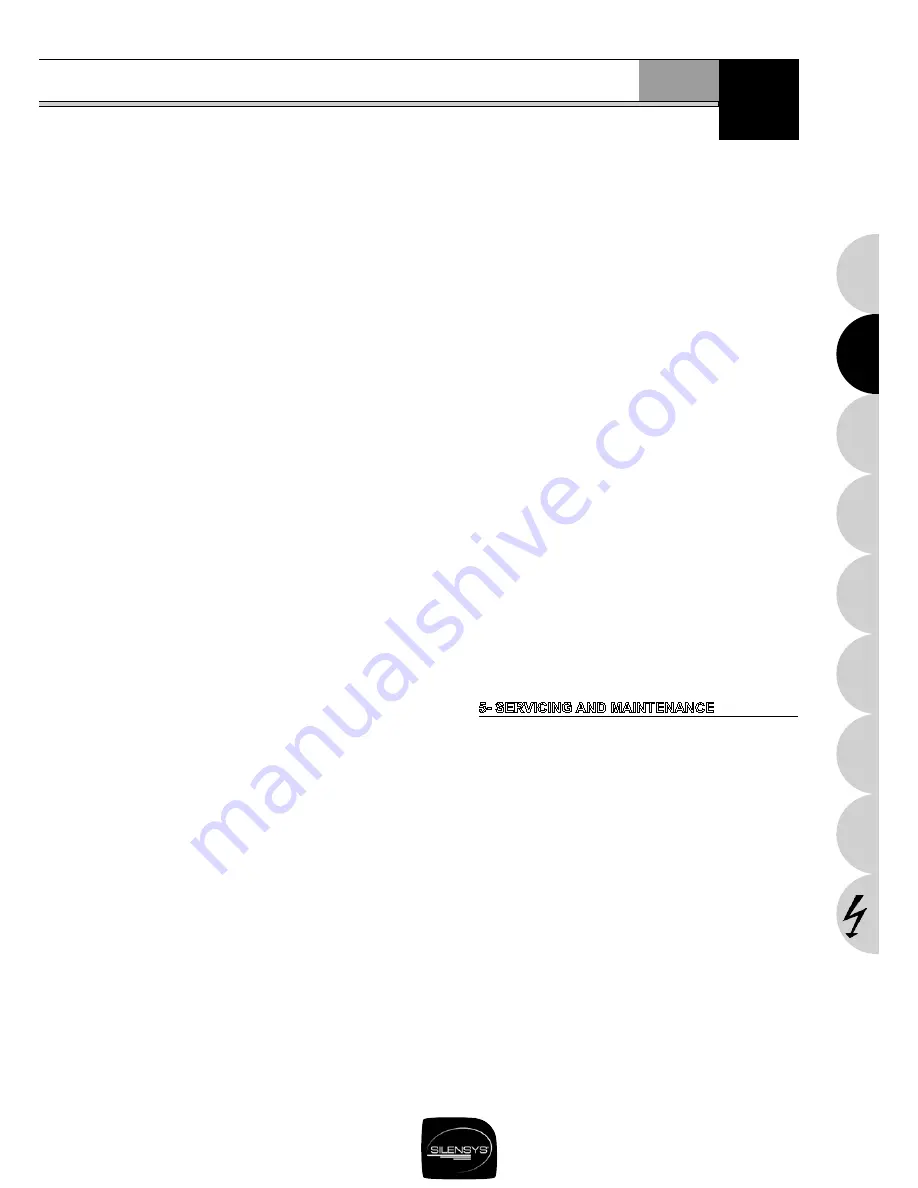
366430 / 04.2013_b
11/40
EN
ES
RU
ANNEXE
S
FR
DE
IT
PL
|
Installation Instructions
■
4.1. Preventing leakage
All connections must be systematically checked for any leakage
with an electronic leakage detector suitable for the type of
refrigerant used. A leak test can be carried out before pulling a
vacuum by using a pre-charge of nitrogen and a leak detection
aerosol (refrigerant tracers not approved) around the joints.
Do not over pressurize the system when using nitrogen. A
more accurate check using an electronic leakage detector can
be carried out after charging with refrigerant.
■
4.2. Pulling a vacuum
Pull a deep vacuum on the installation to about 200 microns
mercury or 0,27 mBar, with a suitable vacuum pump.
We recommend that a vacuum is pulled simultaneously from
both high and low pressure sides of the system to ensure
a uniform vacuum throughout the system including the
compressor and to reduce the amount of time required to
obtain the vacuum.
■
4.3. Refrigerant charge
Charge the installation using only the refrigerant for which the
unit has been designed (see identification plate).
Charging with refrigerant will always take place in the liquid
phase in order to maintain the correct blend of zeotropic
refrigerants.. Pre charge will be realized on the liquid line.
Additional charge will be conducted on the suction line until
obtaining the nominal operating mode of the installation
(installation operation). See paragraph “Pre-start check list”
before powering.
NEVER START THE COMPRESSOR UNDER VACUUM, WHETHER
HBP OR LBP and ensure before starting that the compressor
casing is under positive pressure. We therefore recommend to
de charger lentement le circuit frigorifique entre 4 et 5 bars s’il
est au R-404A et à environ 2 bars s’il est au R-134a.
Pre-start check list
Make sure that:
1.
The power supply voltage is compatible with that of the
condensing unit.
2.
Electrical safety devices are set correctly for the
condensing unit.
3.
Service valves are fully open.
4.
The crankcase heater is working.
5.
Condensing unit fan blades rotate freely.
6.
The installation is given a final check for any possible
faults.
7.
In the case of three-phase scroll compressors, control
the order of the phases of the power supply so that the
rotation of the motor allows the compression of the
refrigerant. Reverse 2 phases if necessary.
8.
In the case of the presence of a controller, read the
enclosed leaflet and check the setting values set by
default.
9.
The design of the refrigeration system must be such that
it does not allow the compressor to start more than 6 to
8 times per hour.
Check list after start up
After the installation has been running for several hours, carry
out the following checks.
1.
Voltage and current drawn by the condensing unit are
correct.
2.
Direction of rotation of Scroll and Rotary compressors.
3.
Pressure switch adjustment.
4.
High and low operating pressures of the installation are
correct.
5.
Fan blades are rotating freely
6.
Superheat and sub cooling
7.
Oil level check for multi piston and scroll compressors
8.
The system is checked again for leaks.
9.
For remote installation please refer to the
‘recommendations of use handbook’.
Make sure that the installation is running smoothly.
Carry out a general inspection of the installation (e.g.
cleanliness, vibration and/or unusual noises). Ensure the
settings and the functions of the electrical circuits are correct.
The lack of refrigerant may be characterized by:
- High and low pressure values that are too low
- An evaporator that is partially frozen
- The presence of bubbles on the sight glass.
The excess of refrigerant may be characterized by:
- A high pressure value that is too high
- Over consuming compressor
- Important sub cooling
- A liquid return
■
4.4. Fan speed control
The rotational speed of the fan(s) is controlled by a pressure
actuated fan speed control. Its function is to:
- Prevent an excessive drop in condensing pressure in winter
which would adversely affect the correct operation of the
expansion valve,
- Further reduce noise levels when the ambient temperature
allows.
See Appendix 5, page 35 on fan speed control
2 types of commands for compressors assembled in parallel
are possible:
- Piston compressor: a simple contact activated by a
thermostat or pressure controller (operation in pump down).
- Scroll compressor: electronic controller set up in Silensys®
activates on-off control of compressors according to the
suction pressure and running time.
5- SERVICING AND MAINTENANCE
Unauthorized modifications to Silensys® condensing units are
prohibited. Authorization from Tecumseh must be obtained
prior to any modification whatsoever.
Any faulty part must be replaced with a genuine spare part. In
order to maintain the low noise levels of the condensing unit
over time, we recommend replacing the anti-vibration mounts
and/or isolating pads as soon as any change in the noise or
vibration level of the unit is noticed.
Connections, fan and compressor compartments can be
accessed from either the side door panel or the front of the
unit, without removing the lid.
■
5.1. Condenser
The condenser and the condensing unit should be cleaned at
least once a year. Access from the inside of the unit can be
gained by removing the fan cover.
■
5.2. Replacing the fan
- Switch off and isolate the condensing unit.
- Disconnect the fan motor cable from the junction box.
- Undo the 4 mounting bolts.
- Take off the fan motor assembly.
- Replace the fan motor and its capacitor ( size S model).
Содержание SILENSYS
Страница 45: ......