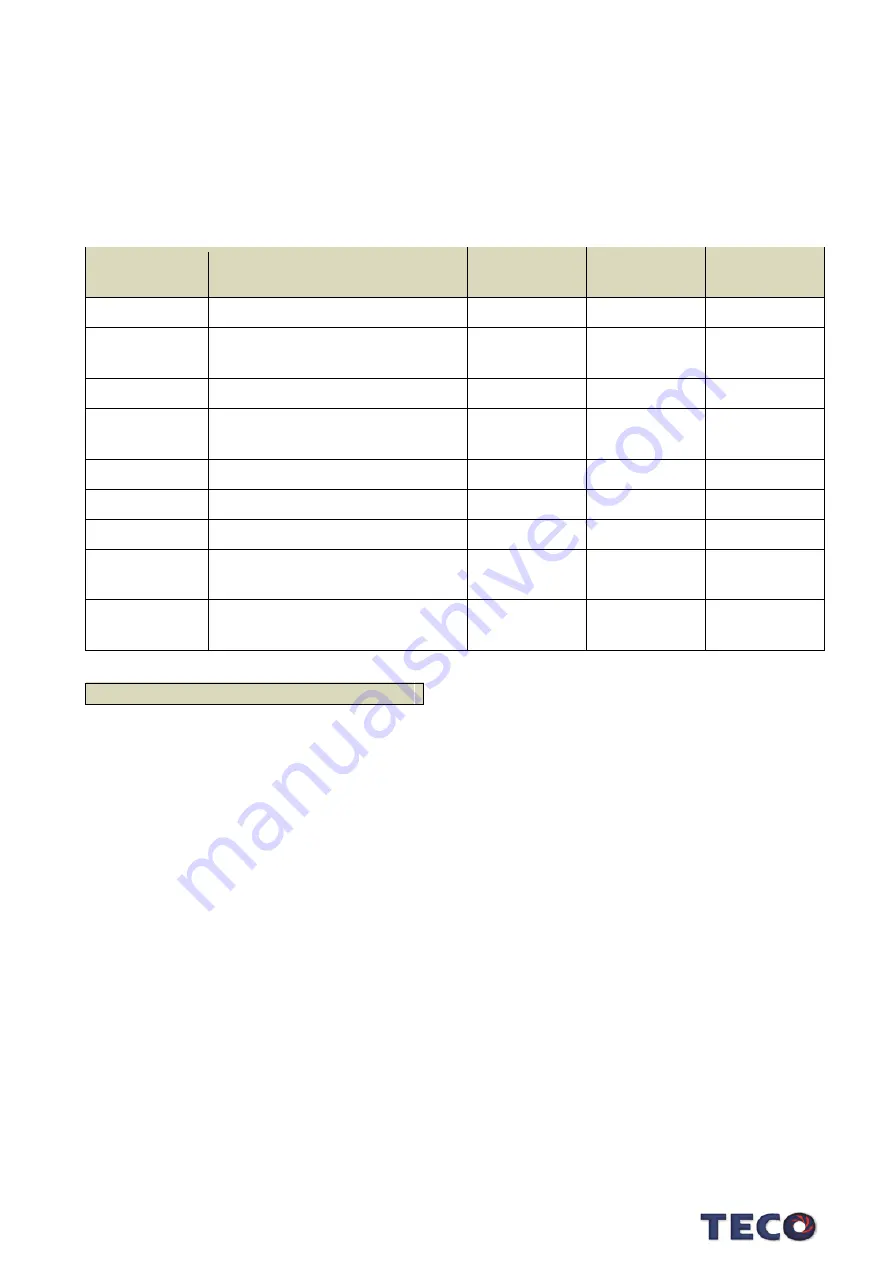
6-9
6-3 Automatic Gain Adjustment (Off-line tuning) Instructions
Automatic gain adjustment refers to the Servo Driver that can be automatically operated
(Forward and Reverse reciprocating motions) without Commands issued by the Supervisory Device
and run adjusting function in accordance with mechanical system characteristics during operations.
The following are the parameters that will be automatically adjusted:
Parameter
Code
Name and Function
Initial Value
Unit
Setting
Range
Cn025
Load Inertia Ratio
10
0.1
0 ~ 2000
Cn034
Torque Command Smoothing
Filter
0
Hz
0 ~ 5000
Sn211
Speed Loop Gain 1
40
Hz
2 ~ 1500
Sn212
Speed Loop Integration Time
Constant 1
2000
0.01ms
40 ~ 50000
Pn310
Position Loop Gain 1
40
rad/s
1 ~ 2000
Cn013
Notch Filter First Set
0
Hz
0 ~ 2000
Cn066
Notch Filter Second Set
0
Hz
0 ~ 2000
Pn339
First Set Low Frequency
Vibration Suppression Frequency
1000
0.1Hz
10 ~ 1000
Pn340
First Set Low Frequency
Vibration Suppression Parameter
0
-
0 ~ 30
Automatic Gain Adjustment Pre-cautions
The Automatic Gain Adjustment is a function that accompanies the Motor Operation, please pay
special attention to the following points:
(1) The Automatic Gain Adjustment will be adjusted using the set Load Inertia Ratio (Cn025) as the
standard. If the system cannot operate steadily when the adjustment is started, correct adjustments
cannot be performed. Please increase the Load Inertia Ratio (Cn025) until after the system can run
steadily, and then perform the adjustment.
(2) The Automatic Gain Adjustment will be adjusted using the set System Rigidity (Cn026) as the
standard. If vibration occurs at the beginning of the adjustment, correct adjustments cannot be
performed. Please decrease the System Rigidity (Cn026) until no vibration occurs, and then
perform the adjustment.
(3) The Automatic Gain Adjustment function performs automatic operations with vibrations, please
execute in the situation of Emergency Stop (Power OFF) that can be done at any time during
execution. In addition, since the two-way rotation is performed within the set movement range,
please confirm the movement range and directions.
Содержание JSDG2S Series
Страница 1: ......
Страница 44: ...2 5 400V Class...
Страница 303: ...5 178 2 3 1...
Страница 586: ...8 81 Method 7 to 14 Homing on the home switch and index pulse Method 19 to 20 Homing without an index pulse...
Страница 662: ...9 1 Chap 9 Error Alarm Clearing 9 1 Error Alarm List 9 2 9 2 Countermeasures to Clear Error 9 5...
Страница 693: ...10 7 10 2 Servo Drive Dimension 1 JSDG2S 10A 15A E 200V Class 2 JSDG2S 20A 30A E 200V Class...
Страница 694: ...10 8 3 JSDG2S 10A 15A EL 200V Class 4 JSDG2S 20A 30A EL 200V Class...
Страница 695: ...10 9 5 JSDG2S 10A 15A L 200V class 6 JSDG2S 20A 30A L 200V Class...
Страница 697: ...10 11 9 JSDG2S 200A3 E 200V Class JSDG2S 100B E 400V Class 10 JSDG2S 300A3 E 200V Class JSDG2S 150B 200B E 400V Class...
Страница 700: ...10 14 Up to 130 Frame Series Up to 220 Frame Series...
Страница 702: ...10 16 Up to 80 Frame Series Up to 80 Frame Series LL Without brake LL With brake JSMA PBC Series JSMA PLC Series...
Страница 703: ...10 17 Up to 130 Frame Series Up to 130 Frame Series LL Without brake LL With brake MB Series BH Series...
Страница 704: ...10 18 Up to 220 Frame Series Up to 130 Frame Series LL Without brake LL With brake IH Series...
Страница 705: ...10 19 Up to 220 Frame Series Up to 130 Frame Series LL Without brake LL With brake BH Series MH Series...
Страница 713: ...11 1 Chap 11 Appendix 11 1 Manual Revision History 11 2...
Страница 718: ......