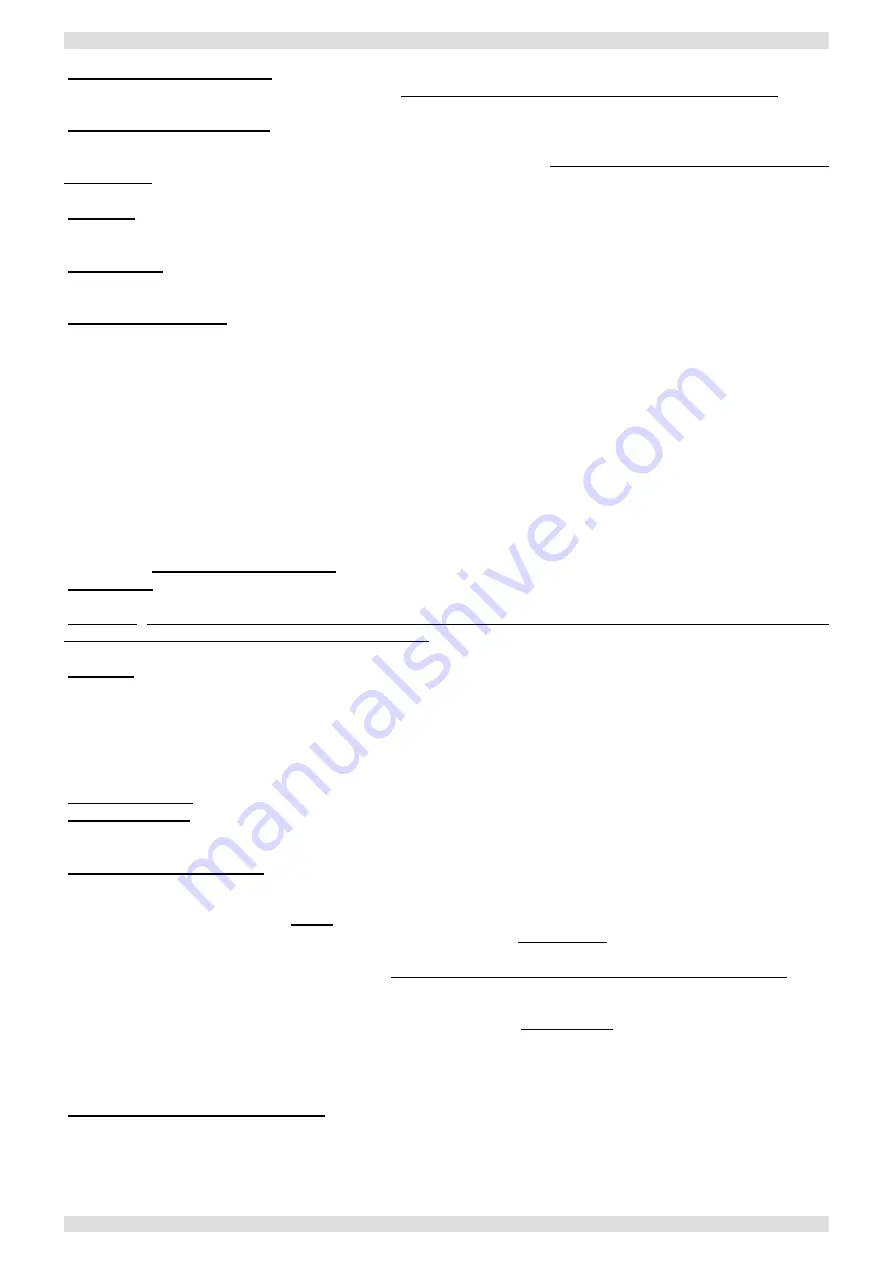
IST-2126.KM03.01
Istruzione / User’s Manual / Manuel d’utilisation
Pag.5/8
TECNOCONTROL S.r.l. Via Miglioli 47 SEGRATE ( MI )
Tel: 02/26 92 28 90 Fax: 02/21 33 734
Model SE126KM positioning:
Methane
(CH
4
) is a combustible gas lighter than air. Its density related to air is
0.55; its LEL (
Lower Explosion Limit
) is 4.4% volume.
The instrument should be fixed at 30 cm from the ceiling
and be
placed at 1-1.5 meter from the gas appliance, far from the room corners or from ventilation intakes.
Model SE126KG positioning
:
LPG
is a gas mixture composed by 20-30% Propane (C
3
H
8
) and by 70-80% Bu-
tane (C
4
H
10
). LPG calibration must be carried out with
Butane
which is a combustible gas heavier than air. Its den-
sity related to air is 2 and its LEL (
Lower Explosion Limit
) is 1.4% volume.
The instrument should be fixed at 30 cm.
from the floor
and be placed at 1-1.5 meter from the gas appliance, far from the room corners or from ventilation in-
takes
Mounting
: The
Fig. 2
shows the instrument size. It has to be wall-mounted by four screw anchors. The
normally
closed manually resetting valve
for the gas cut-off should be installed outside the room in a clearly indicated posi-
tion and should be protected from rain.
Cable glands
: the lower side of the housing has 3 inputs designed for metric cable glands (
M20x1.5 that accept
external cables Ø 6÷12 mm
). These passages are closed, but they are not
manually breakable
, according to the in-
stallation requirements, they must be drilling. To facilitate the operation, they have a centering for the drill bit.
Electrical Connection:
The installation must be provided for the mains, a bipolar disconnect switch dedicated for
the gas detection system. The device, clearly identified, must act only on Phase and Neutral. If it is necessary, you
may install a surge or lightning protector, etc.
The instrument is supply with non-reversible and plug-in terminals. Therefore the cables should be anchored to the
case in order to avoid terminal overstress. The connection to the detector does not need any hearting.
Fig. 3
shows the 230VAC powering connection with alarm siren and normally closed manual resetting valve.
Fig. 4
shows the 230VAC powering connection with alarm siren and normally open manual resetting valve.
Fig. 5
shows the 230VAC powering connection with alarm siren and our normally closed manual resetting valve
with positioning sensor (models VR420÷VR480,) to verify, if an alarm occurs, the really gas cut-off.
Fig. 5
shows the 12VDC powering connection with both 12VDC alarm siren and normally closed manual resetting
valve with, for example, our power supply unit PS175 (1,2A) or PS180 (2,5A) with internal 12VDC-7Ah battery to
maintain the system powered on in absence of Main power supply.
In this case, it is possible to connect the power
supply also to 230VAC.
WARNING
The detector
doesn't need adjustments
after being installed.
Average life
:
the sensitive element used in this detector has an excellent stability in time. In fresh air and in normal
working condition the sensor's life is more than 5 years from the date of installation.
Important
: Catalytic sensors can operate only in presence of Oxygen. Do not use pure gases or a lighter directly
on the sensor since they could damage it irremediably
. The detector is not able to detect gas leaks occurring out-
side the room where it is installed, neither inside walls nor under the floor.
Attention
: please note that in polluted environments, where vapours of flammable agents, especially solvents,
might be present, the sensor's life can be reduced. Some substances cause a permanent reduction in sensitivity.
Avoid contacts of the sensor with vapours of Silicone compounds (paintings and sealing paste), Tetra-ethyl Lead
and Phosphate esters. Some other substances produce a temporary loss of sensitivity. These “inhibitors” include
Hydrogen sulphide, Chlorine, Chlorinated hydrocarbons and halogenated compounds. The sensitivity is recovered
after a short period of running in clear air.
FUNTIONAL TESTING
Periodical testing
:
we advise to carry out working tests every 6-12 months.
PAY ATTENTION
: This procedure has to be made with extreme attention and by authorized and trained people;
because starting this procedure it will start both Outputs (relays) causing the activation of connected alarm devices.
The
TEST
key is deactivating when an alarm condition occurs.
Instrument operation check
: push the
TEST
button for 3 seconds until all Led and relays deactivates.
Then the LED will illuminate in sequence. With the LEDs the corresponding relays will activate (Yellow LED and
FAULT relay, 2
nd
red LED and PREAL. Relay, 3
rd
red LED and ALARM relay). After 5 seconds the instrument re-
turns to normal working condition. NOTE: during the Test some conditions occur:
All 5 LEDs illuminates
:
ONLY
when the detector is connected with a control wire for certain types of valves. In this
case the test results correct.
Yellow LED off (after red LEDs)
: indicates the lack of control wire of the valve or that the valve is closed. If this
wire is disconnected from the detector the test results correct, if not please check the valve and repeat test. If test
result is unchanged, electrical problems are in place, please contact the supplier.
The 3rd Red LED off
:
ONLY
when the detector is connected with a control wire for certain types of valves. The
control wire is disconnected or the valve is open. Please check both the valve status and the wire connection and
repeat the test. If wire is disconnected, check if the wire on the terminal “AUX” is connected and repeat the test.
All other cases:
If some LEDs do not light on or some relays do not switch, the detector is damaged. In this case
please replace it or send it back to the supplier.
Calibration testing with gas mixture
:
the calibration is carried out with specific gas in our laboratory. We advise
to check the calibration only
using sample gas bottles with a mixture about 20% or 25%LEL Gas in Air (
20.9%
Oxygen
) (Gas Methane for SE126KM and Butane for SE126KG). Catalytic sensors cannot work without Oxy-
gen
. The calibration testing should be done with Calibration Kit model TC011 (See specific user’s manual). Connect
the sample gas bottle to the flow meter, open Gas (0.3 l/min flow rate), wait for 3 minutes and check that the in-