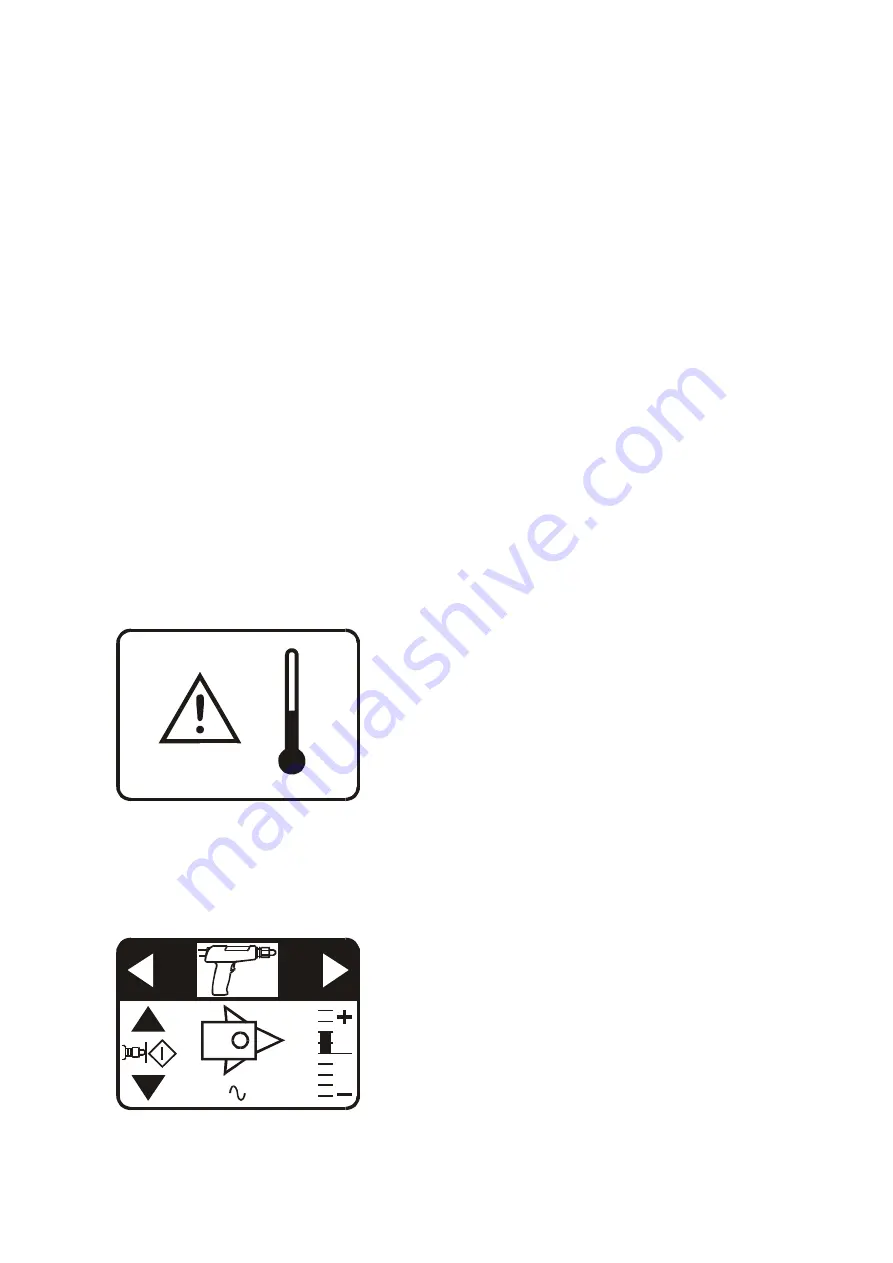
19
MAINTENANCE
The following maintenance operations must be carried out
by specialised personnel only, trained to accomplish them
under safety conditions. When possible, the welder must be
disconnected from electrical supply.
ORDINARY MAINTENANCE
GENERATOR
Keep the weld current connectors
(6-7) clean and clamped.
Remove possible oxidation with fine sandpaper.
Periodically check the status of the power supply cable and
plug. Replace the cable in the presence of cracks, cuts, severe
abrasion, etc.
Check that the welder is connected to the safety conductor and
that the ground wire inside the power cable is not interrupted.
Periodically check the ground efficiency of the system.
Keep the welder clean. Metal scraps are attracted by the
magnetic field generated by the welder during the operation.
Do not wash the welding unit with jets of water which could
enter it nor use strong solvents, thinner or benzine that could
damage paint or machine plastic components.
Check that the fan works efficiently.
MULTIFUNCTION GUN
Keep the weld current plugs and connections clean and
clamped. Remove possible oxidation with fine sandpaper.
The weld cables must be insulated and in perfect working
order. Pay special attention to the points where they bend.
EXTRAORDINARY MAINTENANCE
Only skilled technicians are allowed to make the required
interventions inside the welder.
The generator and the multifunction gun are equipped with
thermal overload protection. The following error is displayed on
starting the weld if overheating occurs.
The error resets by pressing a key or the set button on the handle
of the multifunction gun. The error resets automatically when the
machine cools.
If current is not supplied on starting the weld, check that the
generator receives the command to start welding. The reception
of the command is shown on the display with the change of the
drawing of the tool, as shown in the figure below.
1.5 30%
If during welding the machine causes strong current
consumption, such as to open the circuit breakers or trip the
fuses located on the power line, this might be due to the fact that
the machine had been turned off previously or a power failure
occurred while it was carrying out a weld. In this case perform the
following procedure before resuming work in order to restore the
normal transformer magnetisation condition. Carry out some
welds with an insulator placed between the electrodes with
different current adjustments, first low ones, then progressively
higher. Remove the insulator between electrodes and execute
some welds with a low current adjustment. Routine operating
conditions are restored at the end of the foregoing procedure.
If performance is lower than expected, check:
that, when welding, voltage does not drop more than 15 %.
Excessive voltage drop can be caused by a poor core section
of the power supply system cables or the use of extension
leads with insufficient core sections.
that the weld parameters set in the control unit are correct.