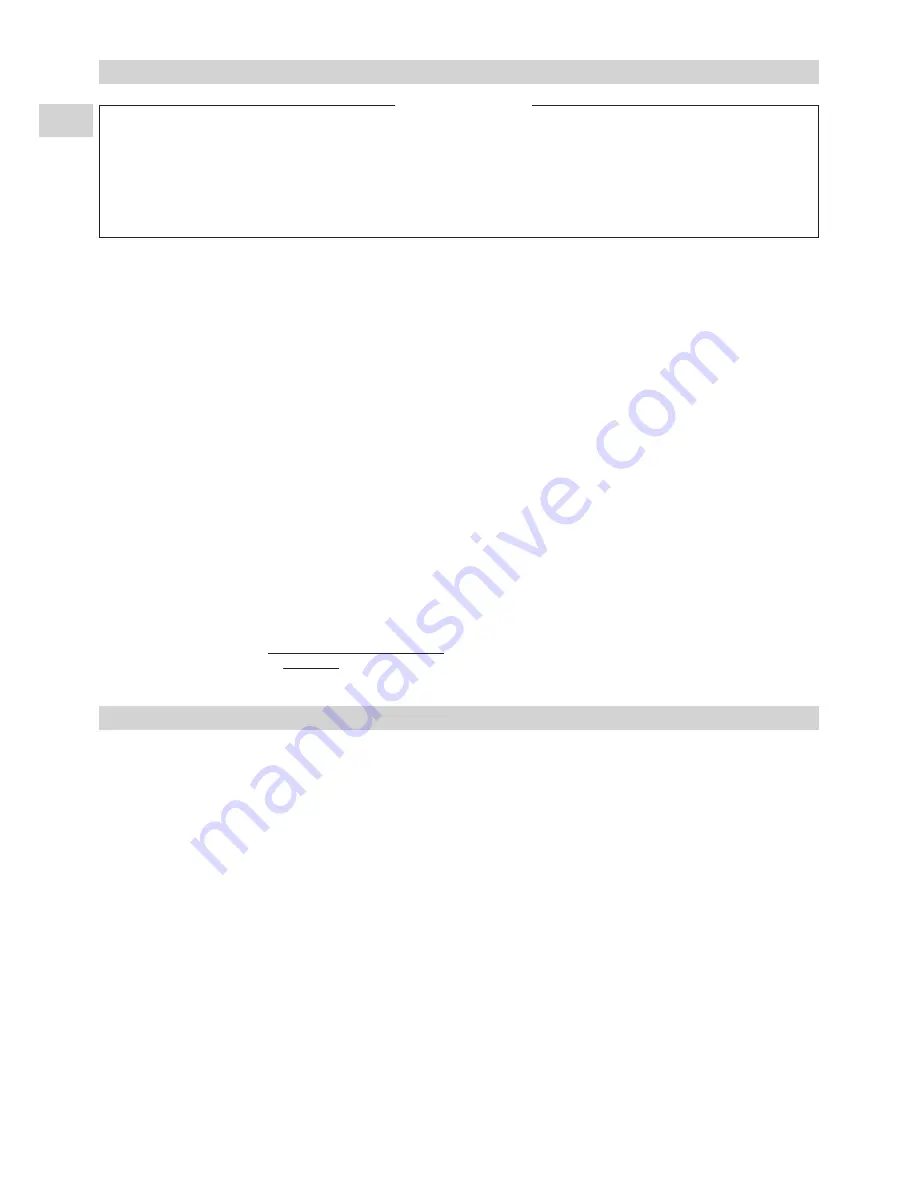
GB
22
8 - MAINTENANCE INSTRUCTIONS
8.1 - MAINTENANCE
All equipment must be properly maintained in order to provide optimum performance over time. Faulty maintenance can result in
the cancellation of the product guaranty. Depending on the products, maintenance operations consist in the cleaning of filters (air,
water), internal and external exchangers, casings, and the cleaning and protection of condensate tanks. Treating odours and the
disinfection of room surfaces and volumes also contributes to the cleanliness of the air breathed by users.
•
Carry out the following operations at least once a year
(the frequency depends on the installation and operating conditions):
- check for leaks on the refrigerating circuit,
- check for traces of corrosion or oil stains around the refrigerating components,
- inspect the composition and the condition of the coolant and check that it does not contain traces of refrigerating fluid,
- cleaning the exchangers,
- checking the wear parts,
- checking the operating instructions and points,
- check the safety devices: particularly check that the high and low-pressure controllers are properly connected on the
refrigerating circuit and that they disengage the electrical circuit if triggered,
- de-dusting the electrical equipment cabinet,
- checking that the electrical connections are secure,
- checking the earth connection,
- check the hydraulic circuit (clean the filter, water quality, purge, flowrate, pressure, etc.),
- verification of the unit's safety valve (and that of the tank, if any).
8.2 - GENERATOR SHUT-DOWN DURING WINTER
•
2 possibilities:
1) Drain the unit and disconnect the power supply.
2) Unit full of water and power on:
as the unit is equipped with an antifreeze device which actuates the water circulating
pump when the temperature drops below zero, it is imperative to ensure that the water can circulate within the unit.
• Before doing any work on the machine, make sure that it is switched off and locked out, with special attention
given in the case of a tank with supplementary heating (different power supplies).
• Any work must be carried out by personnel qualified and authorised to work on this type of machine.
• Prior to all maintenance and servicing on the refrigerating circuit, one must first shut down the unit then wait a
few minutes before installing temperature or pressure sensors. Certain equipment, such as the compressor and
piping, may reach temperatures above 100°C and high pressures may lead to serious burns.
IMPORTANT NOTE
9 - TROUBLESHOOTING
• All maintenance and servicing operations on the refrigerating circuit must be conducted in accordance with standard trade
practices and safety rules: recovery of the refrigerant, inert shielded (nitrogen) brazing, etc…
• All brazing operations must be conducted by qualified welders.
• For equipment loaded with R 407 C, refer to the specific instructions at the beginning of the installation manual.
• This unit is equipped with pressurized equipment, for example piping.
Use only genuine parts listed in the spare parts list for replacing defective refrigeration components.
• Pipes may only be replaced by copper tubing in compliance with standard NF EN 12735-1.
• Leak detection, in the case of pressure testing:
- Never use oxygen or dry air, as the risk of fire or explosion is present.
- Use dehydrated nitrogen or a nitrogen and refrigerant mix indicated on the manufacturer's plate.
- For units equipped with pressure gauges, the test pressure must not exceed the gauges' maximum allowable pressure
rating.
• All part replacement with other than genuine parts, all modifications of the refrigerating circuit, all replacement of refrigerant by
a fluid other than that indicated on the manufacturer's plate, all use of the unit outside the application limits defined in the
documentation, shall result in the cancellation of PED CE marking compliance which shall fall under the liability of the individual
who carried out these modifications.
• The technical information, relative to the safety requirements of the various applicable directives, is indicated on the
manufacturer's plate of the unit and mentioned on the 1
st
page of this manual.