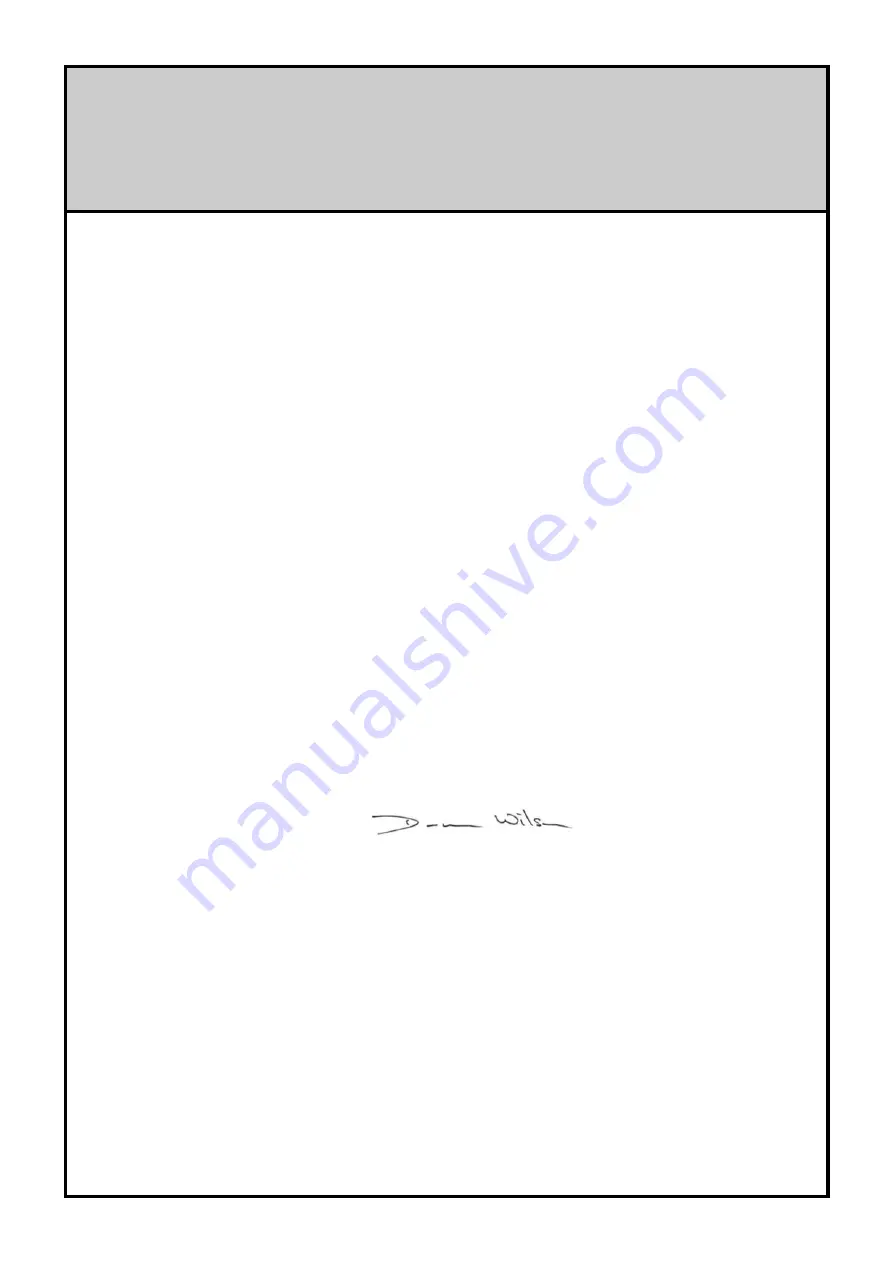
EC Declaration of Conformity
conforming to EEC Directive 2006/42/EC
Teagle Machinery Ltd.
Blackwater
Truro
Cornwall
TR4 8HQ
United Kingdom
declares in sole responsibility that the
Tomahawk
C12
to which this certificate applies
conforms to the essential Health and Safety requirements of
EEC Directive 2006/42/EC & 2004/108/EC.
To effect correct application of the essential
Health and Safety requirements stated in
the EEC Directives, the following harmonised standards were consulted:
BS EN ISO 12100:2010
BS EN ISO 4254-1:2015
Signed:
Duncan Wilson
(Engineering Director)
Dated: 1
st
June, 2016
Person authorised to compile Technical File
Duncan Wilson,
Teagle Machinery
Blackwater, Truro
Cornwall, TR4 8HQ
United Kingdom
Machine Serial No. . . . . . . . . .
Содержание Tomahawk C12
Страница 1: ......
Страница 22: ...19 Rotor Hammer Layout...
Страница 23: ...Notes...
Страница 24: ......