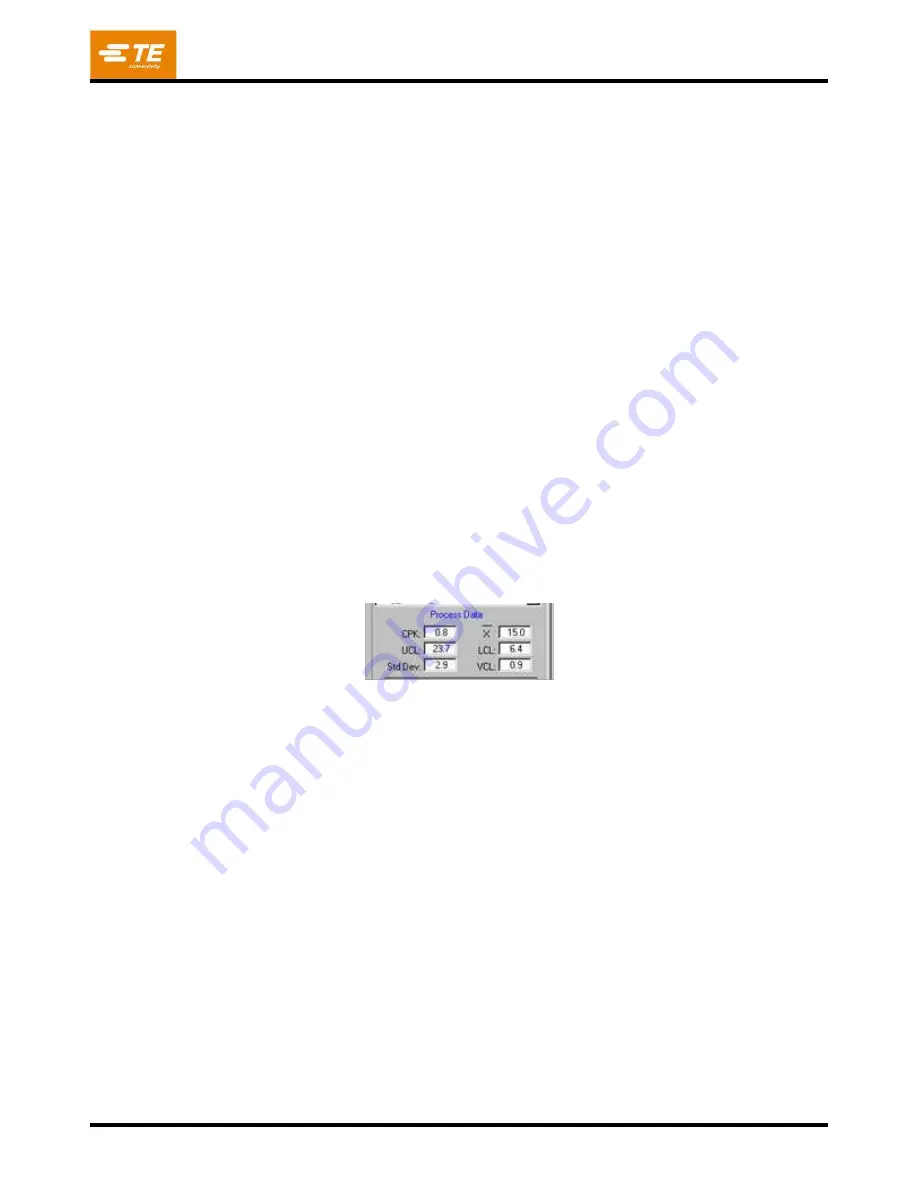
409-32048
Rev A
28
of 64
6.1.
Overview
Raw data for the
average force per pin
for each connector pressed is maintained in a file with the same name
as the connector, with a .RAW extension. SPC information is calculated from the raw data and displayed on
command.
Please refer to the “Connector Database” section above for SPC related
parameters that are entered for each
connector type.
To view data for a connector, select the connector name from the drop down list in the upper left corner of the
SPC screen. All data on the SPC screen is for the
specific connector type
selected. The force data for a
connector is stored in the same file regardless of the specific PCB type (part number, model, etc.) it is pressed
into. In other words, the SPC data for a specific connector pressed into PCB type ABC is stored in the same file
as the data for connectors pressed into PCB type XYZ.
The raw data is stored on the hard drive indefinitely. It includes the PCB model, serial number (if used), date,
time, operator, the SPC force reading point, the maximum force read, and the maximum force reading point.
The header at the top of the raw data file explains the data format in detail.
An average force reading for each connector of a given type on a PCB is calculated and plotted as one point
on the X-bar chart. In other words, each point on the chart is the
average of all connectors of the same type
on a specific PCB.
The difference between the highest and lowest force readings for
the same connector type
on a specific PCB
is plotted on the “R” (Range) chart. The “R” chart becomes an “S” (Standard Deviation
) chart when the
subgroups size is greater than 5 connectors.
The “S” chart plots the standard deviation of
all connectors of
the same type
on a specific PCB.
6.2.
Process Data
This area (Figure 29) shows data that is calculated for the process. It is a measure
of the “health” of the
process for a number of PCBs.
Figure 29
CPK (Process Capability) -
This quality measure is often used to evaluate the capability of the process being
monitored. A number between 1 and 1.5 is generally considered to indicate a process is “in control”. The CPK
is higher for a tighter and more centered distribution, and conversely lower for a broad or poorly centered
distribution. A distribution is “centered” when the average of the measured data is near the target value for that
data. A distribution is “tight” when all measured values are close to each other.
X-Bar (Process Average) -
This is the average of all the points on the X-bar chart. Each point on the chart is
the average of a connector type on a specific PCB.
Std Dev. (Standard Deviation) -
This is the standard deviation (Inter Quartile Range method) of the plotted X-
bar points.
UCL (Upper Control Limit) -
If the plotted X-bar point exceeds this value, the process is considered out-of-
control.
LCL (Lower Control Limit) -
If the plotted X-bar point is less than this value, the process is considered out-of-
control.
VCL (Variability Control Limit) -
If the plotted variability point (R or S) exceeds this value, the process is
considered out of control.
6.3.
Point Data
This area (Figure 30) displays the data for a specific point. To view the data for any point on the chart, point to
it and click the left mouse button.