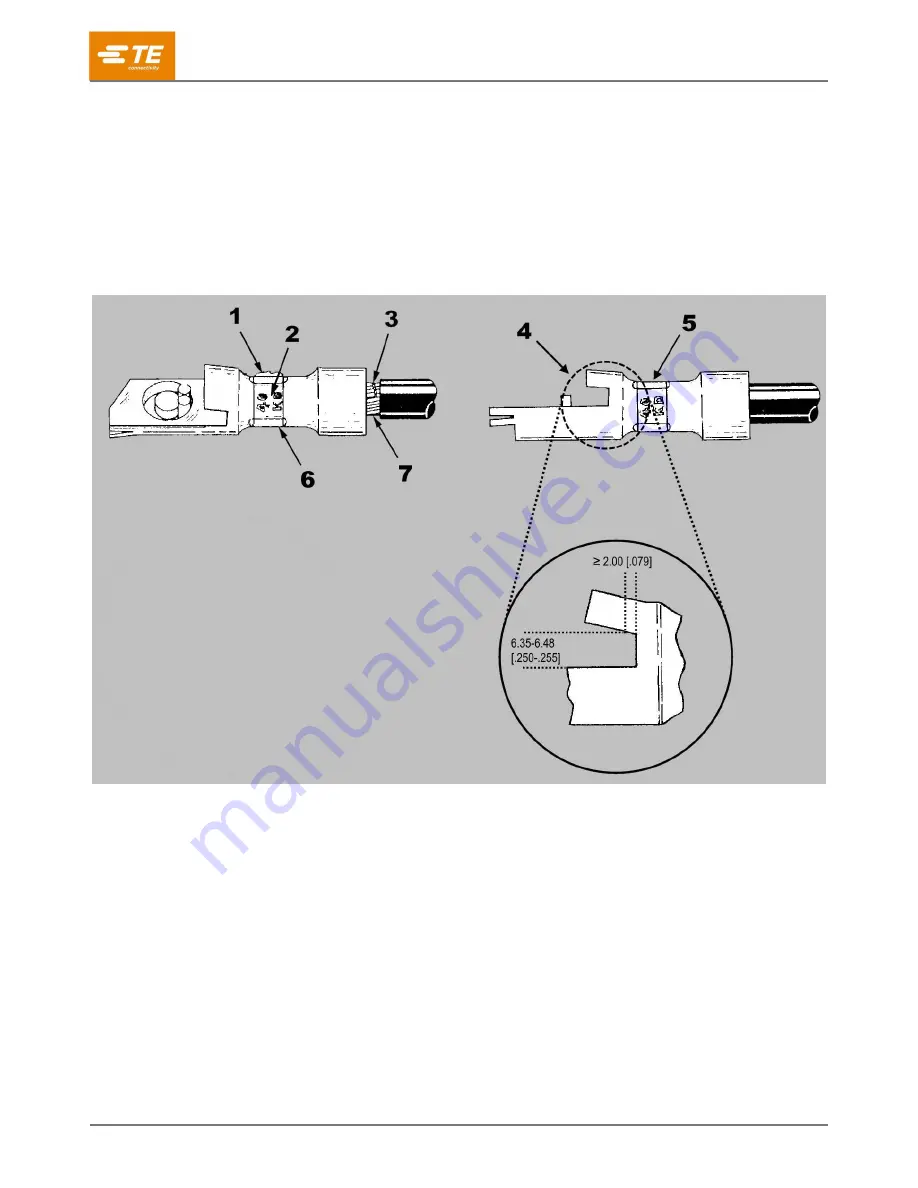
408-2710
Rev
H
6
of 10
Figure 6 shows problems that mean a crimp should be rejected. Most of these are the caused by a terminal
that is not properly aligned with the dies. Avoid unacceptable crimps by carefully following the procedures in
section 4 and performing regular tool maintenance (section 6).
As shown in Figure 6, the large slot in the terminal must meet the following requirements:
The height of the slot must be 6.35 to 6.48 mm [.250 to .255 in.].
At least 2.00 mm [.079 in.] of slot flat must exist.
If the slot is spread open too far, you can correct this by squeezing it in a vise.
Figure 6: Reasons to reject a crimp
1
Excessive flash. Damaged dies or wrong wire, terminal, or tooling combination was used.
2
Embossed wire size does not match size stamped on terminal or CMA of wire.
3
Strands are nicked or missing.
4
Large slot is deformed (spread open).
5
Incorrect crimp orientation.
6
Crimped too far off center, causing large slot to spread open.
7
Wire was not inserted far enough into terminal. Wire insulation did not enter insulation barrel.