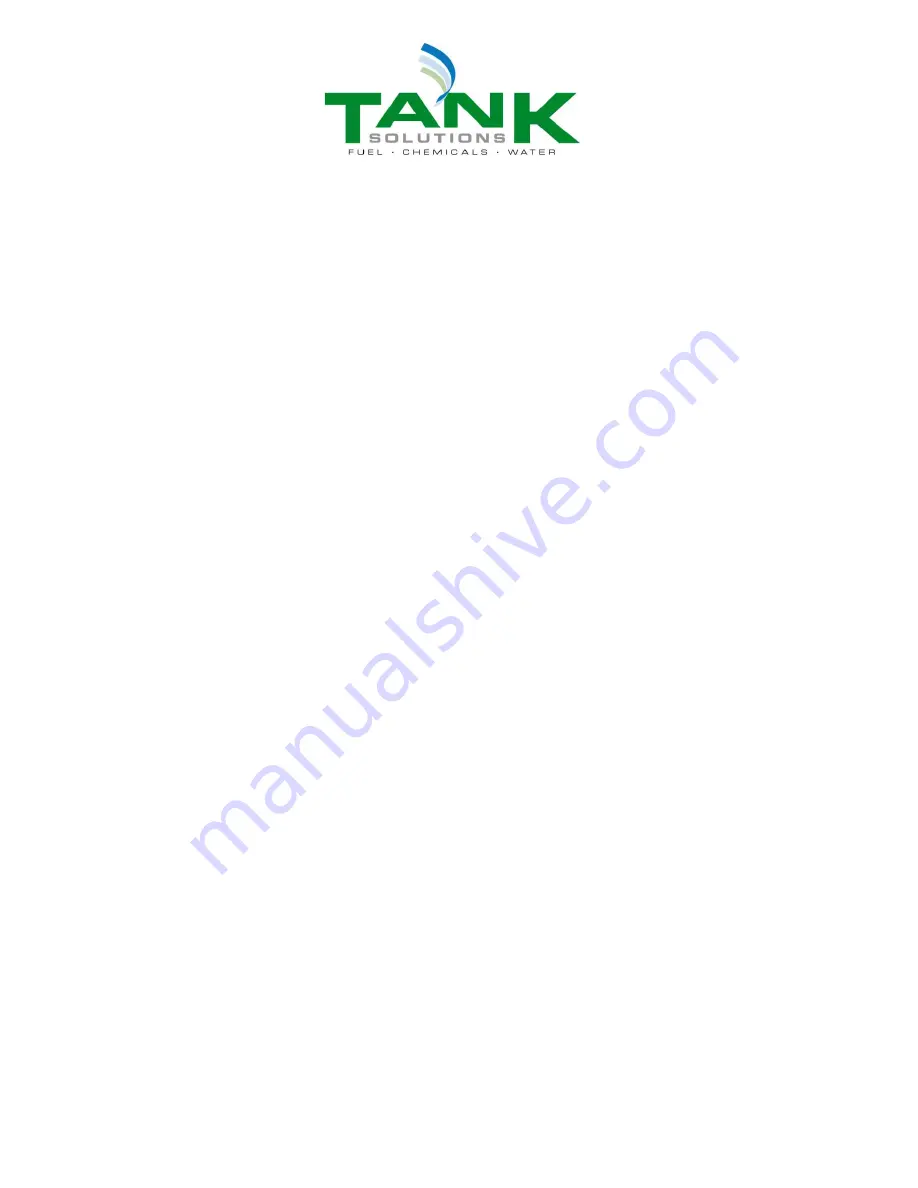
TD_IM_009
Page 2 of 11
Rev 3
Operation, Inspection and Maintenance
All parts which have to be regularly maintained shall be at all times accessible.
Inspections and maintenance of the Aquator should be carried out by experienced personnel at
three, six or twelve monthly intervals depending upon the site
conditions. The maintenance
shall be carried out in accordance with the manufacturer
’s instructions and should include the
following as a minimum;
a) Sludge trap
- determination of sludge volume
b) Separator
- measure the thickness of light liquids
- check the operation of the automatic closure device
- check the coalescing devices for permeability, if the water levels in front and behind
the coalescing device show significant difference
- check the function of the warning device
c) Sampling port
- clean the drain channel
Light liquid and sludge shall be removed as required. Before putting in service the Aquator
shall be filled with fresh water.
Note: emptying is recommended when on half of sludge volume or 80% of the storage
capacity of the separator is reached.
In exceptional circumstances, when personnel need to enter the separator, it shall be fully
drained and thoroughly ventilated.
The regulations / decrees for avoiding accidents and the handling of dangerous materials shall
be followed.
Every five years the separator shall be emptied and then submitted to general inspection
covering the following items;
- tightness of the system
- structural condition
- internal coating, if present
- state of inbuilt parts
- state of electrical devices and installations
- Checking of adjustment of automatic closure device.
The cleaning and maintenance records shall be kept and made available to the
authorities upon request and shall contain remarks on specific events (e.g. repairs,
accidents).