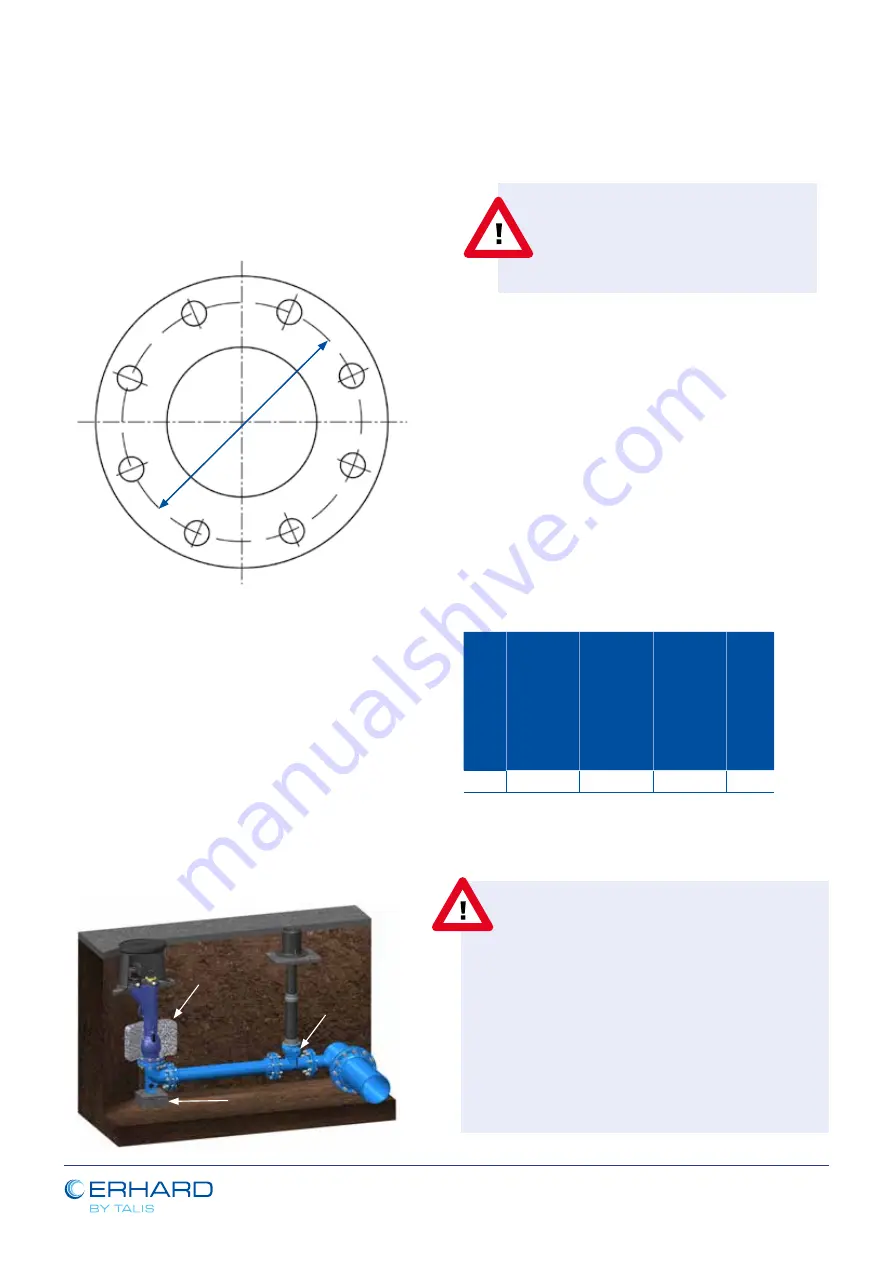
P12
/19
IOM_FIH210201_HALIOS STD-PREM_EN
The technical data and performance may be modified
without prior notice depending on the technical advances.
Draining area
Anchoring system of
the duck foot bend
Upstream
Isolating
valve
• Set up the bolts,
• Tighten them by hand,
• Tighten bolts gradually in a star-shaped pattern (see figure
6 – order from 1 to 8).
• At the end, tighten the connecting bolts evenly, without
distortion and crosswise, under a torque between 100 and
120 Nm. The value must not exceed 70% of the limit of
tightening torque of the bolts used.
Once the hydrant is assembled, the threads of the bolts/rods
should be greased with a brush or spray. MOLYCOTE or a similar
graphite based waterproof grease should be used to prevent
corrosion and facilitate subsequent dismantling operations.
After installation and before backfilling the trench and the
hydrant, perform a pressure test and functionality test (open and
close the hydrant) under pressure.
During backfilling of the hydrant, an adequate and sufficient
draining area must be established directly all around the hydrant
at the level of the two drainage devices, in order to allow the
emptying of its water volume. It may consist for example of an
adequate volume of pebbles, packed gravel, crushed rock or
any other appropriate means. When complete installation of
the hydrant is finished check that the drainage of the hydrant is
working perfectly by verifying that the hydrant empties after an
operation of opening/closing.
6 - COMMISSIONING
AND OPERATION
WARNING
Before installation, refer to technical
leaflet W331 from DVGW for deployment,
installation and implementation.
Before the hydrant is commissioned and installed, it must be
subject to a visual check. After installation, the hydrant must
be checked for movement of the inner valve: turn the square
cap over the total stroke (OPEN-CLOSE).
Each hydrant must be operated in respect of the operating
torque by a key according to DIN 3323-C.
Over-torque on the hydrant is strictly prohibited. According to
DIN standards, you will find in the table below the Maximum
Operating Torque (MOT) and Minimum Strength Torque (MST)
in Nm for gate underground fire hydrants to be operated by
key according to DIN 3323-C (see table 4). Operation by other
means or "Ring key and bar" is strictly prohibited.
Closing or opening operation of the hydrant must be done
under a torque that do not exceed the MOT stated in the table
below. In any case it is recommended to:
- turn 1/4 turn back after a complete opening operation,
- turn 1/4 turn back after a complete closing operation.
DN
Maximum
Operating
Torque (MOT)
according to
DIN EN14339
and DIN
EN1074-6
(in Nm)
Minimum
Strength
Torque (MST)
according to
DIN EN14339
and DIN
EN1074-6
(Nm)
Total number of
turns for
Opening or
Closing
(full stroke)
(Nm)
Number
of turns
before
flow
80
105
210
9
4
Table 4: Torques and number of turns
WARNING
Excessive torque may damage the hydrant body and
result in uncontrolled water leakage of up to 16 bar. In
this case, further work on the hydrant must be stopped
immediately and a safe distance to the hydrant must be
maintained, especially directly above the hydrant. The
isolating valve installed upstream of the hydrant must be
closed immediately in order to stop the supply of water.
If the torque necessary to close the hydrant is above
MOT values, plan a maintenance phase on the hydrant.
In case of over-torque applied to the hydrant, a proper
maintenance must be done including replacement of
the damaged components.
1
5
8
4
3
6
7
2
Figure 6: Flange DN80
Figure 7: Installation example