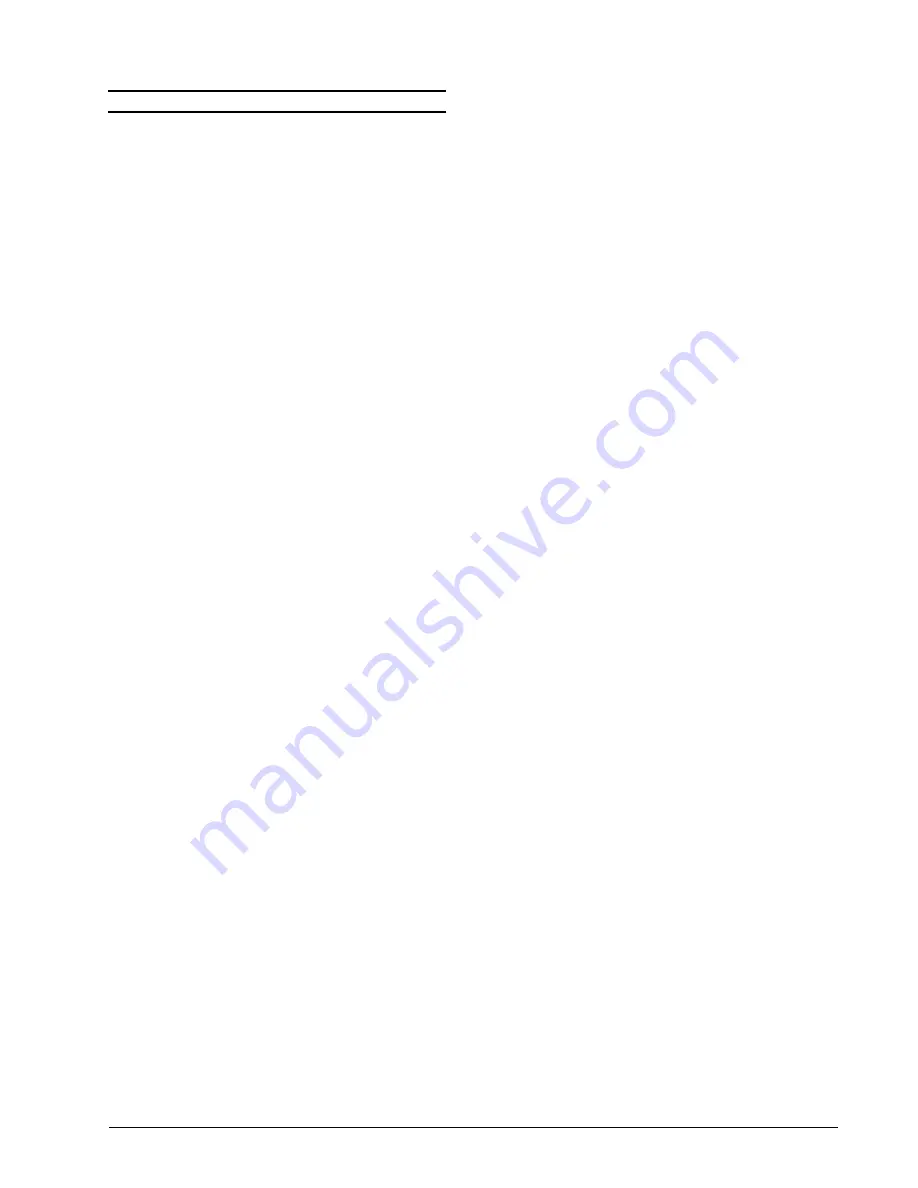
Model 1700 / 1750 Rotary Platform Abraser
17
Operating Instructions ver. 1.0
p/n 135505
TEST PROCEDURE
As you start your testing, use of these guidelines
should assist you in developing a test procedure
that will yield reproducible test results, accurate
within the variations of quality inherent in the
material itself.
Establishing a Test Procedure
The purpose of this section is to outline all the
elements of a typical test procedure from analysis
of the testing problem to final evaluation of results.
Knowledge of the mere mechanics of testing, the
preparation and mounting of specimens, and the
setup and operation of the Abraser is presumed.
To aid in the establishment of a test procedure, the
following recommendations are offered. It is
important to recognize that these recommendations
may not apply to all variations of materials and that
modifications may be required in performing a
practical abrasion test. They should not be
construed as fixed test specifications.
Analyze Test Problem
– The value of the Taber
Abraser in research and quality control programs
depends to a considerable extent on the operator’s
knowledge of the test problem; the service
requirements and the desired wear characteristics
of the material examined. Analyzing this problem
before embarking on a test series may save time
and material. As nearly as possible, the test should
reproduce the wear experience of the specimen in
actual use.
Control Test Environment
– Both heat and
moisture may affect the abrasion resistance of most
materials, particularly organic materials. Therefore,
an environmentally controlled test room is strongly
recommended where reproducible precision results
are required. Abrasion research projects are
normally carried out in an atmosphere maintained
at 23 °C ± 2 °C (73.4 °F ± 3.6 °F) with 50 ± 5%
relative humidity. For materials that are susceptible
to humidity, samples should be conditioned in the
test atmosphere for at least 24 hours
– organic
materials preferably for 48 hours or more. When
research is conducted to determine wear life under
changing atmospheric conditions, as in automobile
and aircraft materials, the atmosphere of the
laboratory may be controlled accordingly.
NOTE:
If an environmentally controlled test laboratory is
not available, test specimens should be conditioned and
tested with a minimum lapse of time.
NOTE:
When it is necessary to interrupt a test of organic
material for several hours, or overnight, the sample should
be discarded and a new test begun. In the course of a few
hours the weight of a sample may change by moisture
absorption or for other unexplained reasons.
Determine Test Procedure
– Standard test
procedures for a number of materials have been
established and, in the interest of uniformity and the
ready exchange of information, are very generally
accepted. To ensure that test results will be
comparable, the procedure described should be
followed exactly.
In the absence of a standard specification, the
technician must work out his or her own test
procedure. Choice of abrading wheels, load
weights, method of mounting the sample, duration
of test, and other details may best be decided by
preliminary testing of the specimen material.
Begin by estimating the nature and degree of wear
that the specimen would receive in actual service.
Select an abrasive wheel that will most nearly
reproduce this wear. Under ordinary conditions a
load and wheel combination should run on a
specimen a minimum of 300 cycles before the end
point occurs, otherwise the test may be too harsh.
In certain instances there may be exceptions to this
rule since there are many varieties of material that
can be tested with the Abraser.
When setting up a test procedure, always keep in
mind to avoid wearing the material too fast as this
will result in ripping and tearing action.
Record Test Procedure
– It is essential that
careful record of every phase of the test procedure
be kept for purposes of comparison. This will also
enable others to duplicate the test at a later date.
Select Evaluation Method
– Test results are
commonly expressed as a wear factor or numerical
abrasion index of the test specimen. The most
common methods for calculating this index are by
measuring a visual or physical change. For
additional information see page 19.
Содержание 1700
Страница 1: ...Taber Rotary Platform Abrasion Tester Model 1700 1750 Operating Instructions...
Страница 2: ......