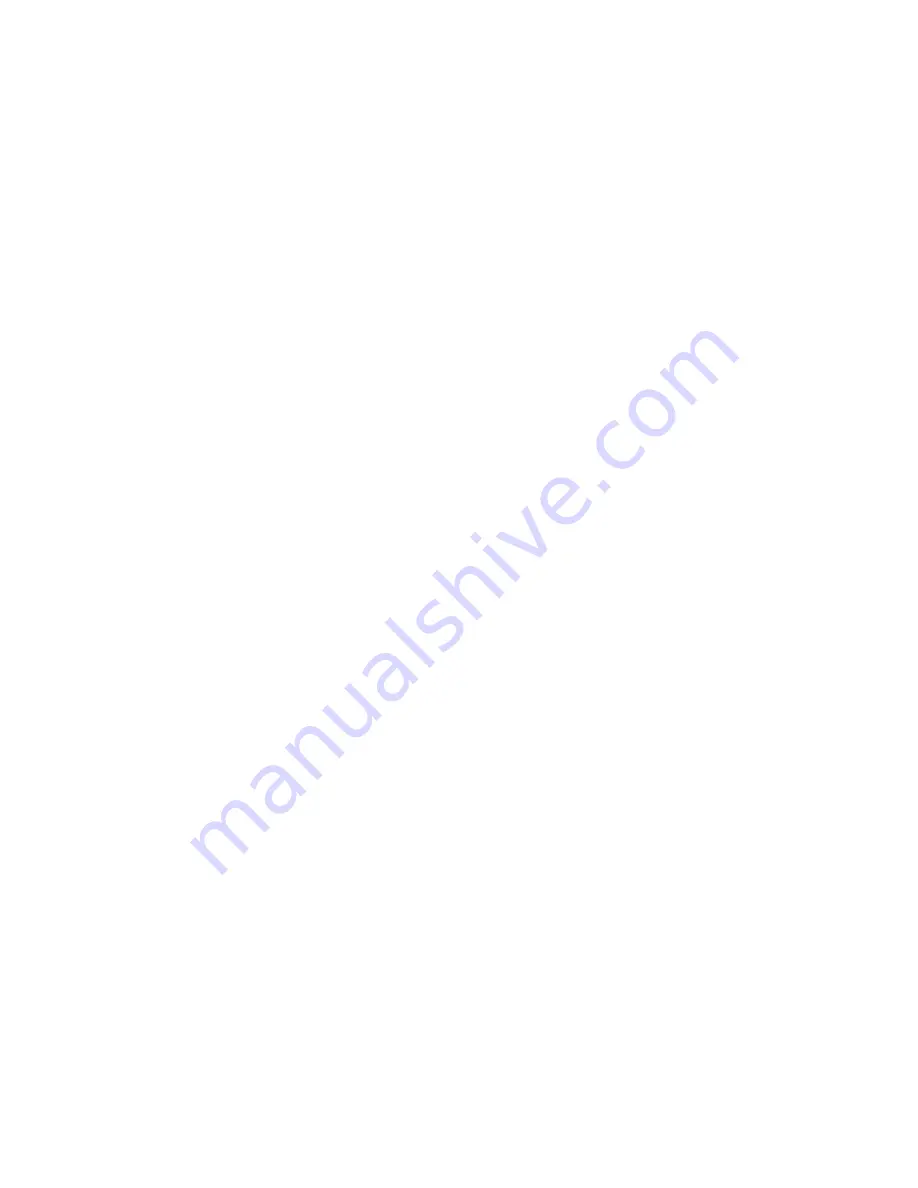
30
HYDRAULIC SYSTEM
MAJOR COMPONENTS OF THE WATER INLET SYSTEM (Right Side)
Drain Tube (from brew tanks):
This copper manifold allows water from the brew valves to discharge safely
down the drain after shots are completed.
Expansion Valve:
The brew tanks are completely saturated with water. As they heat, the water expands and
the pressure increases. The expansion valve allows this water to release safely into the drain box. The re-
lease point is 12 bar and is adjustable by turning the end of the valve with a wrench clockwise to increase or
counterclockwise to decrease the maximum achievable pressure.
Heat Exchanger Tubes:
In order to maintain extremely stable brewing temperatures, Synesso
™
incorporates
heat exchanger tubes which run through the steam tank, then supply water to each coffee boiler. The heat
exchangers are precisely designed to aid in the energy efficiency and thermal stability of the brew system.
Cold Water Valve:
Synesso
™
machines have 2 valves which provide water to the hot water tap (tea tap or
Americano tap): the hot and cold water valves. Mixing in cold water allows the user to moderate the tem-
perature at the spout. Boiling water is not appropriate for all beverages.
Hot Water Valve:
This valve supplies hot water from the steam tank (which is mixed with cold water from
the cold water valve) to the hot water tap.
Mix Valve Adjuster:
This pin valve allows the user to increase or decrease the flow of cold water (from the
cold water valve above) going to the hot water tap. Turning this valve completely clockwise shuts the cold
water off, while turning it counterclockwise allows more cold water in.
Pressure Relief Valve (PRV):
The PRV is a safety release for the steam boiler which opens and releases pres-
sure if the boiler rises above 3.5 bar (50 psi). The PRV is housed inside the yellow tubing which directs any
releases to the drain box.
Sight Glass:
Connected to the steam tank by two tubes, the sight glass provides a visual representation of
the level of water in the steam tank. It should be 1/2 to 2/3 full during normal operation.
Steam Inlet Check Valve:
See Brew tank check valve description. (Page 29).
Steam Inlet Water Control Valve:
When the upper level probe (Page 32) detects an absence of water, the
control board will send a signal to open this valve and allow water into the steam tank.
Steam Tank Inlet Fill Line:
This is the incoming
3/8”
steel braided line which supplies the steam tank with
water. It will be labeled with a pink tag.
Vacuum Breaker:
Prevents steam tank pressure from dropping below atmospheric pressure. As the tank
heats, the pressure from the steam pushes an internal rod and o
-
ring up, sealing the vacuum breaker. When
the tank cools below the boiling point, steam will condense and shrink in volume potentially pulling a vacu-
um in the steam tank. At this point, the internal rod and seal will drop down and allow air into the tank to
replace the cooling steam, preventing a vacuum.
Содержание MVP
Страница 12: ...12 INSTALLATION DIMENSIONS ...
Страница 26: ...26 HYDRAULIC SCHEMATIC MVP ...
Страница 27: ...27 HYDRAULIC SCHEMATIC MVP HYDRA ...
Страница 34: ...34 ELECTRICAL SYSTEM Main Electronics Board MVP MVP Hydra ...
Страница 38: ...38 ELECTRICAL SYSTEM Electrical Schematic ...
Страница 44: ...44 PROGRAMMING Brew System Error Codes ...
Страница 45: ...45 PROGRAMMING Brew System Error Codes ...
Страница 46: ...46 PROGRAMMING Brew System Error Codes ...
Страница 48: ...48 PROGRAMMING Steam System Error Codes ...
Страница 49: ...49 PROGRAMMING Steam System Error Codes ...
Страница 50: ...50 PROGRAMMING Steam System Error Codes ...
Страница 71: ...71 TEMPERATURE OFFSETS ...